It can be seen from Figure 1 that compared with the normal pressure, the hardness of the alloy can be improved by pressure casting. The hardness of the sample of alloy 1 is increased by about 17% at 170Mpa, and that of alloy 2 is increased by about 25% at 160MPa. The reasons for the increase of hardness are as follows: the solidification rate of the alloy increases under pressure, and the hardness increases due to fine grain strengthening; In addition, according to the phase transformation of carbides studied in the previous paper, it can be concluded that the pressure can make part of m3c and M23C6 transform into more stable M7C3, and the hardness value of M7C3 is the highest among carbides by querying the hardness value of different carbides.
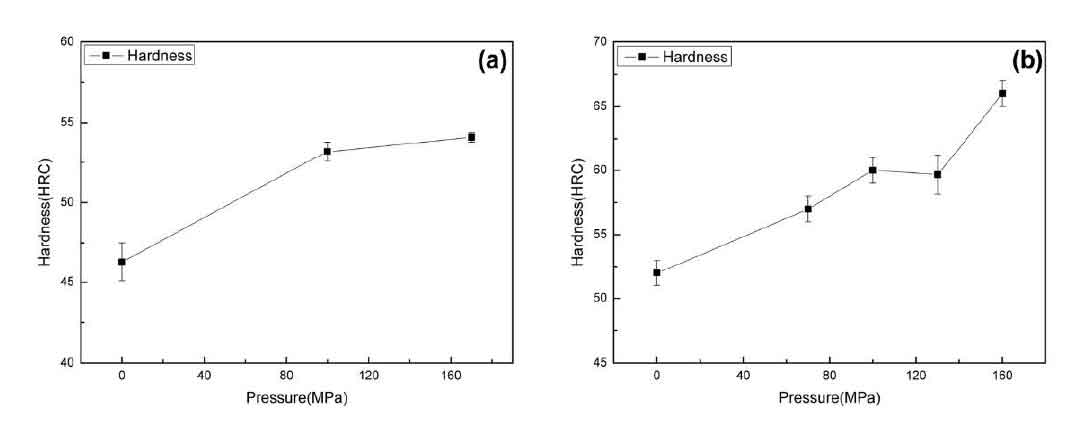
The wear resistance is affected not only by the macro hardness of the material, but also by the stress distribution at the interface between matrix and carbide. By changing the ratio of matrix hardness to carbide hardness, different stress concentration points may lead to different material displacement and wear loss. The deformation mismatch caused by the hardness difference between the matrix and carbide will also cause the separation of the interface between the matrix and carbide, leading to the formation of microcracks and reducing the wear performance. Therefore, it is necessary to test the microhardness of carbide and matrix to discuss the matching degree between them.
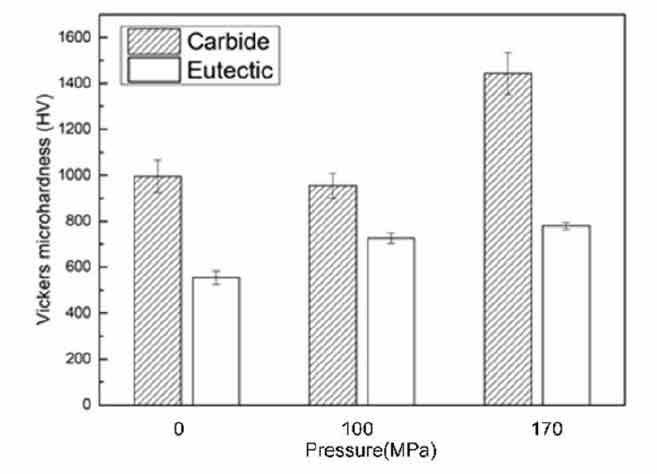
As shown in Figure 2, the hardness of primary carbide increases to a certain extent with the increase of pressure, but it is not obvious. The hardness of eutectic matrix increases significantly with the increase of pressure. The microhardness of the alloy first increases and then decreases with the increase of pressure. On the one hand, the solid solubility of alloy elements increases with the increase of pressure, resulting in the effect of solid solution strengthening. On the other hand, due to the grain refinement, the number of grain boundaries increases greatly, and the number of dislocations increases significantly when the pressure and rapid solidification are non-equilibrium solidification, which means that the dislocation work to be overcome is greatly increased. From the macro effect, the strength of the material is enhanced, from the micro effect, the alloy defects are reduced, and the mechanical properties of the structure are improved, that is, the fine grain strengthening. Therefore, the microhardness of the pressurized sample is higher than that of the normal pressure casting sample, which is the result of the combination of fine grain strengthening and solid solution strengthening. According to the length of the error bar, the error bar of the high pressure sample is shorter than that of the normal pressure sample, which indicates that the microhardness of the microstructure becomes uniform and the size difference decreases.
In addition, pressure not only affects the type transformation of carbides, but also affects the phase composition of matrix. Through the calibration of X-ray diffraction pattern, it can be seen that in addition to austenite phase, there are some retained austenite phase and martensite phase. However, these phases are not common in the solidification structure without heat treatment.
The precipitation of carbides in cast iron is very slow even at high temperature, which leads to that the austenite formed during solidification often contains supersaturated Cr and C, which is very stable and still exists in the form of austenite phase and carbide phase below eutectic temperature. When the alloy continues to cool, with the precipitation of Cr containing carbides, the alloy content and stability in austenite are reduced. When the temperature is below the eutectoid transformation condition, the unstable austenite can be transformed into pearlite, bainite or martensite at different cooling rates.
According to the composition of the alloy, the martensitic transformation temperature ms of the experimental alloy can be calculated by Steven formula as follows:
πs= 561 β 474πΆ β 33ππ β 17πΆπ β 17ππ β 21ππ
The results show that the martensite transformation temperature of alloy 1 is 549 Β± 1 β and that of alloy 2 is 541 Β± 1 β. No martensite can be obtained at room temperature. While pressure provides cooling conditions for austenite to martensite transformation, it also reduces the diffusion coefficient of elements, resulting in that the dissolved carbon atoms in austenite have no time to diffuse outside the cell. When the austenite reaches the martensite transformation temperature (MS), the martensite begins to transform and the parent austenite is unstable.