Because the composition of low chromium white cast iron alloy 1 is far away from eutectic point, the carbides are eutectic carbides. The solidification structure under normal pressure is shown in Fig. 1 (a), and the as cast structure is composed of honeycomb ledeburite, strip carbide and pearlite. The carbides are long and straight, and their size is very large, even across the whole field of view. And the thickness distribution is very uneven, even though it is a thin slab, its length is also very large. At the same time, the edge of the lath is relatively smooth, the two ends are sharp, and all the laths present the same direction. With the increase of pressure, the coarse lath becomes smaller and smaller along the length direction, there is no length across the field of view, and the directivity of the lath becomes disordered, which is distributed unevenly in all directions. In addition, the edge of the lath is not smooth enough, and there are small curved laths and cross shaped strip carbides. When the pressure reaches 170Mpa, as shown in Fig. 1 (c), the straight lath like carbides can not be found basically, they become curved laths, and most carbides become polygonal lumps. Compared with the distribution of carbides at lower pressure, the distribution of carbides becomes relatively uniform when the pressure increases to 170 MPa.
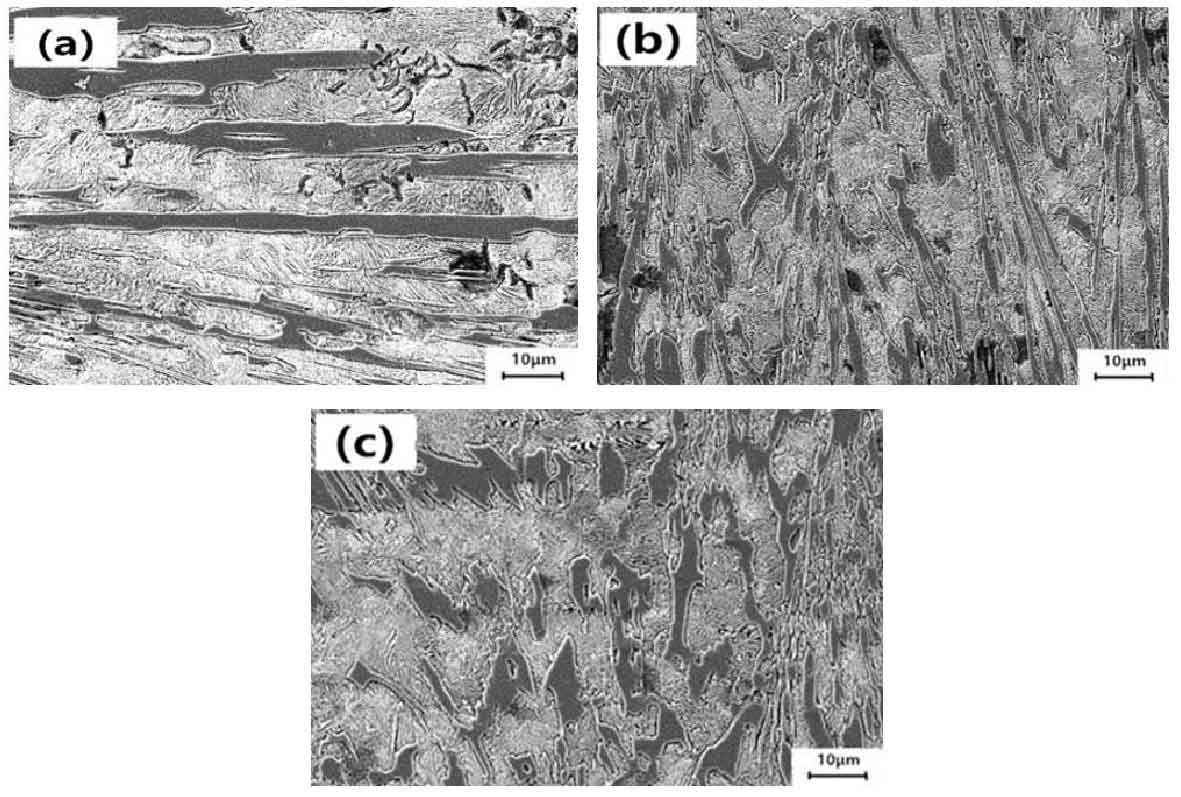
By comparing and analyzing the solidification structure of alloy 2 # under different pressures, it can be seen that the solidification structure of alloy 2 # under normal pressure is the same as that of alloy 1 # which is strip-shaped carbide, while the solidification structure under pressure appears dendritic carbide. In Fig. 2 (b), with the increase of pressure, the dendrites of dendrite carbides bend, and the dendrites overlap with each other, wrapping austenite between dendrites instead of growing forward. As shown in Fig. 2 (c), almost all lath or dendrite carbides are bent to different degrees. With the further increase of pressure, the wrapped smooth carbides gradually close, and the edges and corners become clear and polygon. When the pressure is increased to 160 MPa, almost all carbides are polygonal, and a few are curved laths, but the size is small. At the same time, the white matrix structure is reduced or even disappeared.
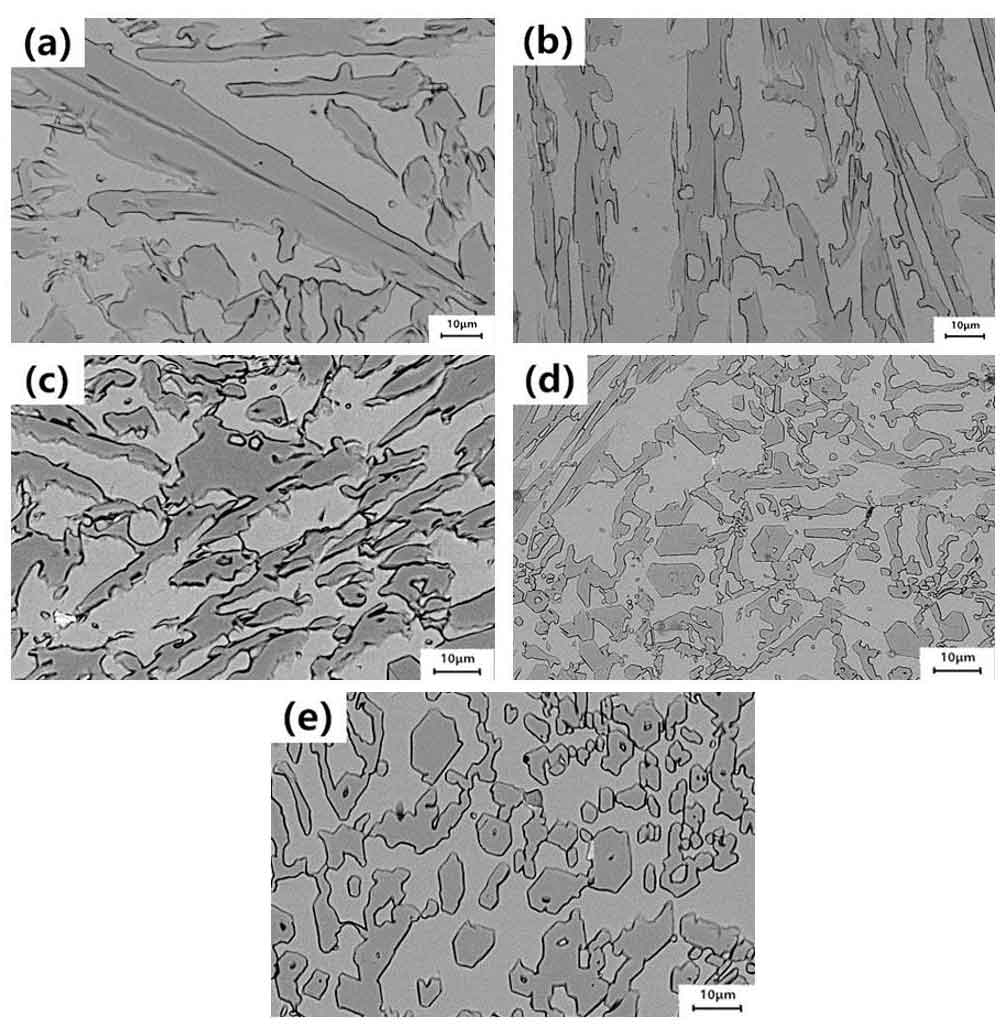
The size of eutectic carbide in alloy 1 in Fig. 3 (a) decreases with the increase of pressure. When the pressure is large enough, the decrease tends to be flat or even not obvious. At the same time, the size deviation also decreases with the increase of pressure, and the decrease range is larger when the pressure is not high. The size uniformity of eutectic carbides has changed significantly. Under normal pressure, the size difference between eutectic carbides is large, and the uniformity is not strong. When the pressure is high, the size distribution is relatively uniform. In Fig. 3 (b), the size of eutectic carbide in alloy 2 also decreases with the increase of pressure. Different from that in alloy 1, the size reduction of eutectic carbide is average. Although the size deviation does not decrease with the increase of pressure, it is within a relatively small deviation range compared with that in alloy 1. This shows that the size of eutectic carbide in alloy 2 decreases with the increase of pressure, but the effect of pressure on the size difference of eutectic carbide is not obvious, and the size uniformity of eutectic carbide is better than that of alloy 1.
The size of eutectic carbides can be reflected by discussing the size of eutectic carbides, but in order to further understand the influence of pressure on the morphology of eutectic carbides, it is necessary to introduce a characteristic quantity, i.e. aspect ratio, to describe its morphology. The ratio of the longest diameter inside the grain to the longest diameter perpendicular to the grain is obtained by Image Pro Plus 6.0
In Fig. 4 (a), the aspect ratio of eutectic carbide in alloy 1 decreases with the increase of pressure. When the pressure is 170Mpa, the aspect ratio of grain is the smallest. The morphology of eutectic carbides changed significantly, and the microstructure changed from long lath to short rod to nearly equiaxed. With the increase of pressure, the deviation of aspect ratio of alloy 1 # is smaller, which indicates that the pressure makes the lath and rod eutectic carbides with larger aspect ratio transform into equiaxed grains with smaller aspect ratio. In Fig. 4 (b), the aspect ratio of eutectic carbides in alloy 2 decreases with the increase of pressure. The aspect ratio of eutectic carbides in alloy 2 cast under normal pressure is still larger, which indicates that there are lath and long rod-shaped grains in it. When there is pressure in the solidification process, the aspect ratio of grains decreases sharply, and it is within a relatively small deviation range. Compared with alloy 1, the decrease of the aspect ratio of eutectic carbide in alloy 2 requires less pressure, while that in alloy 1 requires higher pressure to achieve the same effect.