In the study, working conditions 1, 2, 3 and 4 represent four working conditions with applied pressure of 70, 46, 23 and 0mpa. The initial mold temperature of condition 1 is 230 ℃, the other three conditions are 250 ℃, and the pouring temperature of four conditions is 660 ℃. This means that the four working conditions are basically the same, but the applied pressure is changing.
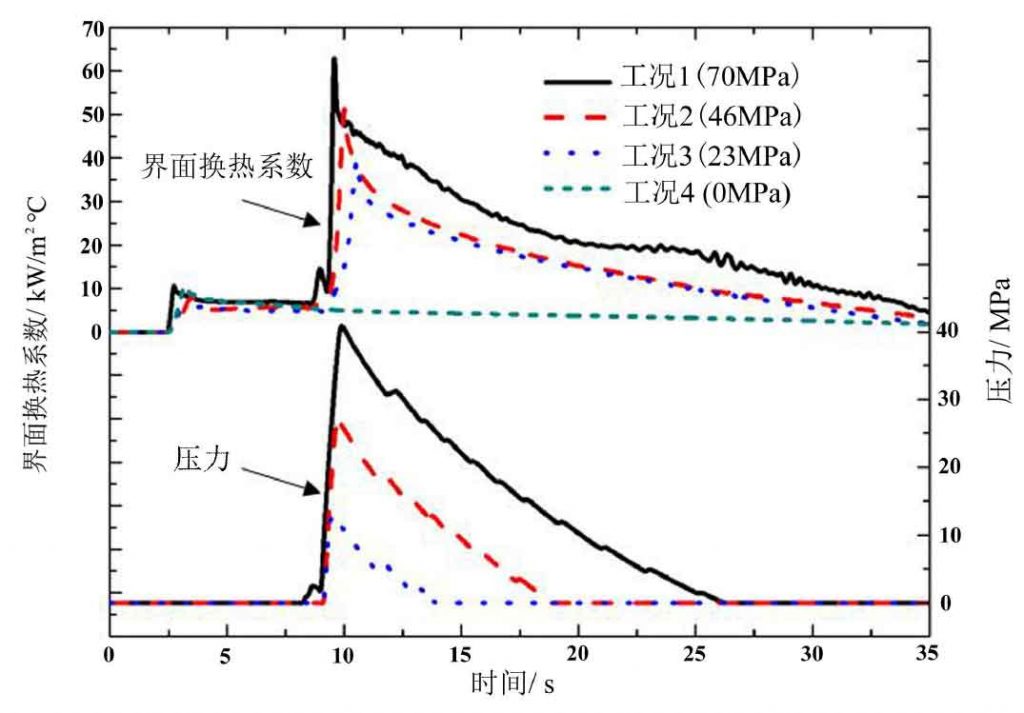
As shown in the figure, before the application of the external pressure, the variation law of the interface heat transfer coefficient is similar because the working conditions are basically the same. Because no external pressure is applied in case 4, the interfacial heat transfer coefficient decreases gradually with the solidification process, and no other change occurs. The average value of the interface heat transfer coefficient in case 4 is 3.92 kwm-2k-1. Compared with condition 4, the average values of the other three conditions are much higher. This shows that the external pressure greatly improves the contact state of the casting die surface and reduces the thermal resistance of the interface.
As shown in the figure, at the beginning of pressure application, both the heat transfer coefficient and the interface pressure of the casting die interface increase suddenly and reach the maximum. The larger the applied pressure is, the larger the maximum values of heat transfer coefficient, heat flux and pressure are. After the applied pressure, the interfacial heat transfer coefficient begins to decrease, sharply decreases at the beginning, and then remains a downward trend, but the decreasing rate gradually decreases. Among them, the decreasing trend and numerical value of the interface heat transfer coefficient of condition 2 and condition 3 are similar. The interface heat transfer coefficient of condition 1 is significantly higher than that of the other two conditions, which indicates that the effect of interface pressure on the interface heat transfer coefficient is more significant when the applied pressure is 70 MPa.