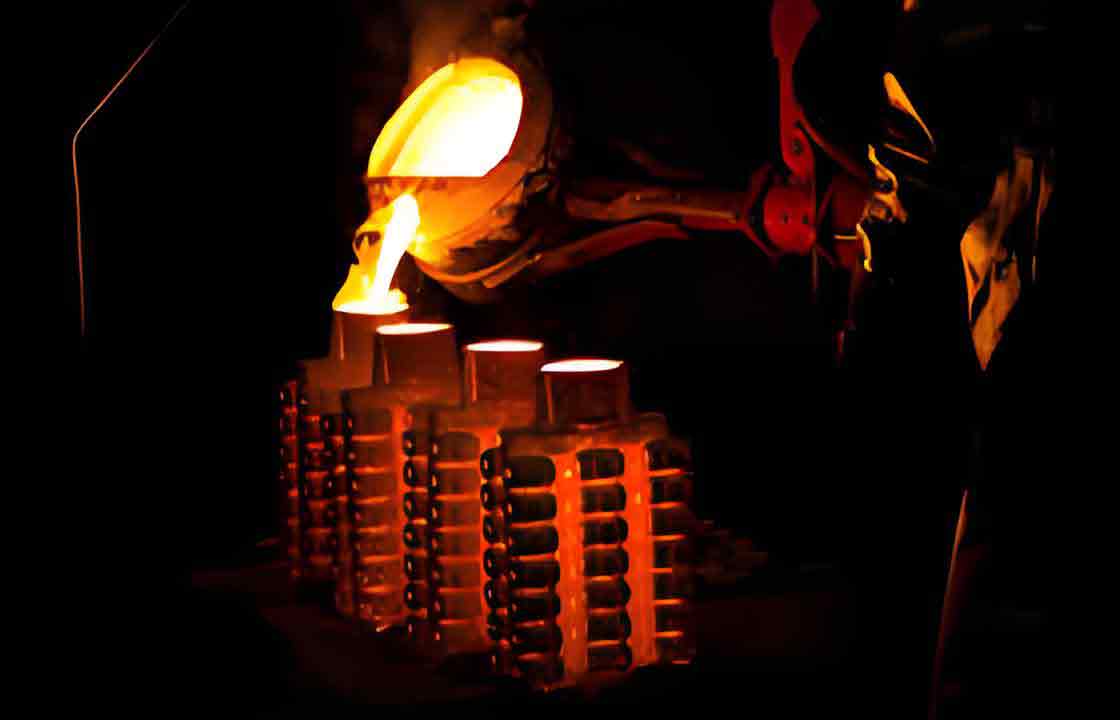
Lost wax casting is versatile and precise manufacturing process used to produce complex metal components. For a lost wax casting manufacturer, achieving energy efficiency and process optimization is essential for improving productivity, reducing costs, and minimizing environmental impact. This article explores various strategies and technologies that can be employed to enhance energy efficiency and optimize processes in lost wax casting manufacturing.
Introduction to Lost Wax Casting
Lost wax casting involves creating a wax model of the desired part, which is then coated with a ceramic shell. The wax is melted out, leaving a cavity that is filled with molten metal. Once the metal solidifies, the ceramic shell is removed to reveal the metal casting. This process is particularly advantageous for producing components with complex geometries and fine details.
Key Steps in Lost Wax Casting
- Pattern Creation: A wax model of the desired part is created using injection molding or hand carving.
- Assembly: Multiple wax models can be assembled onto a wax tree to create multiple parts in a single batch.
- Shell Building: The wax assembly is repeatedly dipped into a ceramic slurry and coated with fine sand to build a ceramic shell.
- Dewaxing: The ceramic shell is heated to remove the wax, leaving a hollow cavity.
- Metal Pouring: Molten metal is poured into the ceramic mold.
- Shell Removal: Once the metal has solidified, the ceramic shell is broken away to reveal the casting.
- Finishing: The casting is cleaned, and any excess material is removed to achieve the final product.
Importance of Energy Efficiency in Lost Wax Casting
Energy efficiency is crucial in lost wax casting as it directly impacts operational costs and environmental sustainability. By reducing energy consumption, casting manufacturers can lower production costs, decrease greenhouse gas emissions, and comply with regulatory standards.
Key Areas for Energy Efficiency
- Pattern Creation: Energy-efficient wax injection and carving techniques.
- Shell Building: Optimized drying and curing processes for ceramic shells.
- Dewaxing: Efficient heating methods for wax removal.
- Metal Pouring: Controlled melting and pouring temperatures.
- Cooling and Solidification: Effective cooling systems to minimize energy use.
- Finishing: Energy-efficient cleaning and finishing techniques.
Strategies for Energy Efficiency in Lost Wax Casting
1. Optimizing Wax Pattern Production
Wax pattern production can be energy-intensive. Implementing energy-efficient wax injection and carving techniques can significantly reduce energy consumption.
- High-Efficiency Wax Injection Machines: Use machines with advanced heating and injection controls to minimize energy use.
- Recycling Wax: Implement a wax recycling system to reuse waste wax and reduce material costs.
2. Improving Ceramic Shell Building
The shell building process involves multiple cycles of dipping and drying, which can consume a considerable amount of energy.
- Optimized Drying Systems: Use energy-efficient drying ovens and ensure proper airflow to reduce drying times.
- Advanced Slurry Formulations: Develop ceramic slurries that require fewer coats and shorter drying times.
3. Efficient Dewaxing Techniques
Dewaxing involves heating the ceramic shell to remove the wax, which can be energy-intensive.
- Microwave Dewaxing: Utilize microwave heating technology for faster and more energy-efficient dewaxing.
- Autoclave Dewaxing: Implement autoclave systems that use steam pressure to remove wax efficiently.
4. Controlled Metal Melting and Pouring
Melting and pouring metal require significant energy. Controlling these processes can lead to substantial energy savings.
- Induction Melting Furnaces: Use induction furnaces, which are more energy-efficient and provide precise temperature control.
- Preheated Molds: Preheat molds to reduce the energy required for metal pouring and improve casting quality.
5. Effective Cooling and Solidification
Cooling and solidification can be optimized to reduce energy consumption and improve casting quality.
- Optimized Cooling Systems: Use energy-efficient cooling systems that maintain consistent temperatures and reduce cycle times.
- Directional Solidification: Implement techniques that control the direction of solidification to minimize defects and energy use.
6. Energy-Efficient Finishing Techniques
Finishing processes, such as cleaning and machining, can also be optimized for energy efficiency.
- Automated Finishing Equipment: Use automated equipment that reduces manual labor and energy consumption.
- Advanced Abrasive Technologies: Employ high-efficiency abrasives and polishing techniques to minimize energy use.
Case Studies: Energy Efficiency in Lost Wax Casting Manufacturing
Case Study 1: Automotive Components
An automotive casting manufacturer implemented high-efficiency wax injection machines and optimized ceramic shell drying systems. These changes resulted in a 20% reduction in energy consumption and improved production rates.
Case Study 2: Aerospace Parts
A leading aerospace casting manufacturer adopted induction melting furnaces and preheated molds for their production process. This led to a 15% decrease in energy use and enhanced the quality of their cast components.
Case Study 3: Medical Devices
A medical device manufacturer introduced microwave dewaxing and advanced slurry formulations in their lost wax casting process. These improvements reduced energy consumption by 25% and shortened production cycles.
Process Optimization in Lost Wax Casting
Process optimization is essential for enhancing productivity, reducing defects, and minimizing costs in lost wax casting. By continuously improving each step of the casting process, manufacturers can achieve higher efficiency and better-quality castings.
Key Areas for Process Optimization
- Pattern Creation: Enhancing the precision and repeatability of wax patterns.
- Shell Building: Streamlining the shell building process for consistency and quality.
- Metal Pouring: Controlling metal pouring parameters for uniformity and reduced defects.
- Cooling and Solidification: Optimizing cooling rates to minimize internal stresses and defects.
- Finishing: Improving finishing techniques for faster and more accurate results.
Strategies for Process Optimization in Lost Wax Casting
1. Enhancing Pattern Creation
- Automated Wax Injection: Implement automated wax injection systems for consistent pattern quality.
- Precision Tooling: Use high-precision tooling for wax pattern production to ensure dimensional accuracy.
2. Streamlining Shell Building
- Automated Dipping Systems: Use automated dipping systems to ensure uniform slurry application and build consistent ceramic shells.
- Real-Time Monitoring: Implement real-time monitoring of shell building parameters to detect and correct any deviations immediately.
3. Controlling Metal Pouring Parameters
- Automated Pouring Systems: Use automated metal pouring systems to control pouring speed and temperature accurately.
- Simulation Software: Implement casting simulation software to predict and optimize metal flow and solidification patterns.
4. Optimizing Cooling and Solidification
- Controlled Cooling Rates: Use controlled cooling systems to manage cooling rates and minimize internal stresses.
- Directional Solidification: Implement directional solidification techniques to improve mechanical properties and reduce defects.
5. Improving Finishing Techniques
- Automated Finishing: Use automated finishing equipment to reduce manual labor and improve consistency.
- Advanced Abrasives: Employ advanced abrasive technologies for faster and more efficient finishing.
Case Studies: Process Optimization in Lost Wax Casting Manufacturing
Case Study 1: Industrial Machinery
An industrial machinery casting manufacturer optimized their pattern creation process by implementing automated wax injection and precision tooling. These changes resulted in improved pattern quality and reduced cycle times.
Case Study 2: High-Performance Engines
A manufacturer of high-performance engine components used casting simulation software to optimize their metal pouring parameters. This led to a significant reduction in casting defects and improved overall component performance.
Case Study 3: Medical Implants
A medical implant manufacturer optimized their cooling and solidification processes by implementing controlled cooling systems and directional solidification techniques. These improvements enhanced the mechanical properties and reliability of their cast implants.
Conclusion
Achieving energy efficiency and process optimization in lost wax casting manufacturing is essential for improving productivity, reducing costs, and minimizing environmental impact. By implementing advanced technologies and optimizing each step of the casting process, manufacturers can produce high-quality castings with greater efficiency. Continuous improvements in energy efficiency and process optimization ensure that lost wax casting remains a vital and versatile manufacturing process for a wide range of applications.