The engine cylinder block serves as the core component determining lubrication efficiency and operational reliability. Among critical quality metrics, cylinder bore geometry directly influences oil consumption patterns. This paper analyzes deformation mechanisms in honing processes and proposes a countermeasure using simulated assembly conditions to minimize post-deformation oil loss.
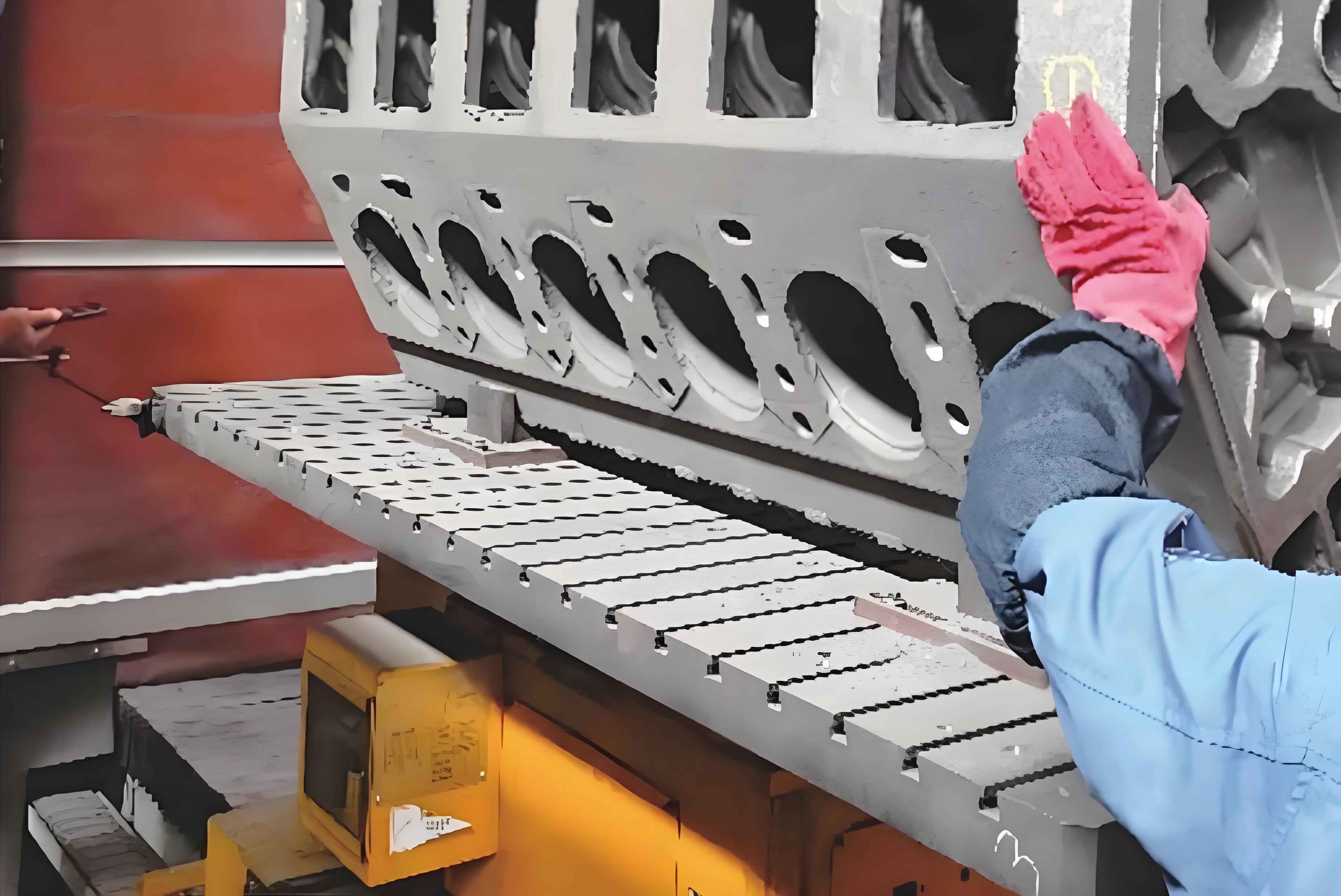
1. Oil Consumption Pathways
Primary oil consumption mechanisms in engine cylinder blocks include:
Pathway | Contribution | Key Influencers |
---|---|---|
Cylinder Wall Lubrication | 90% | Piston ring geometry, bore circularity |
Valve Guides | 5-7% | Oil seal integrity, thermal expansion |
Crankcase Ventilation | 3-5% | Blow-by gas pressure, oil mist formation |
The dominant factor remains cylinder bore geometry, where non-uniform oil film distribution caused by bore deformation creates localized oil accumulation zones. The instantaneous oil film thickness follows:
$$ h(\theta) = \frac{C(\theta) – r'(\theta)}{2} $$
Where $C(\theta)$ represents deformed bore radius and $r'(\theta)$ denotes piston ring profile after elastic deformation.
2. Cylinder Bore Deformation Analysis
Bore geometry deviations are quantified through:
$$ \text{Roundness} = \max(R_i) – \min(R_i) $$
$$ \text{Cylindricity} = \max(Z_{ij}) – \min(Z_{ij}) $$
Fourier decomposition reveals deformation harmonics:
Harmonic Order | Primary Cause | Typical Magnitude (μm) |
---|---|---|
0 (Concentricity) | Machining tolerance | ±2 |
1 (Eccentricity) | Fixture alignment | 3-5 |
2 (Ovality) | Thermal expansion | 8-12 |
4 (Quadroform) | Head bolt torque | 15-25 |
The fourth-order deformation (n=4) from head bolt tightening creates characteristic quadrilateral distortion:
$$ \Delta R_4(\theta) = A_4\cos(4\theta + \phi_4) $$
Where $A_4$ represents deformation amplitude and $\phi_4$ denotes phase angle.
3. Process-Integrated Honing Solution
Traditional honing processes produce near-ideal circularity but fail to account for assembly-induced deformations. Our modified approach incorporates:
Parameter | Standard Honing | Process-Compensated Honing |
---|---|---|
Tooling | Diamond abrasives | Adaptive CBN stones |
Clamping | Base-only fixture | Simulated head (80% assembly torque) |
Cycle Time | 4.5 min/cylinder | 5.2 min/cylinder |
The compensation process achieves 68% reduction in fourth-order deformation:
$$ \frac{A_{4,\text{comp}}}{A_{4,\text{std}}} = e^{-0.725(T/T_0)^{1.2}} $$
Where $T$ represents simulated torque percentage and $T_0$ denotes full assembly torque.
4. Verification Results
Comparative measurements demonstrate significant improvement:
Depth (mm) | Standard Process (μm) | Compensated Process (μm) |
---|---|---|
5 | 18.2 | 3.8 |
70 | 24.6 | 6.1 |
125 | 30.3 | 8.9 |
Engine oil consumption tests confirm 41% reduction in 10,000km endurance runs:
$$ \Delta \text{Oil Consumption} = 0.87 – 0.51\ \text{L/1000km} $$
This methodology establishes a production-viable solution for optimizing engine cylinder block performance through process-integrated deformation compensation.