Enhancing efficiency in the investment casting process is crucial for improving productivity, reducing costs, and achieving shorter lead times. Here are some key strategies and techniques to enhance efficiency in investment casting:
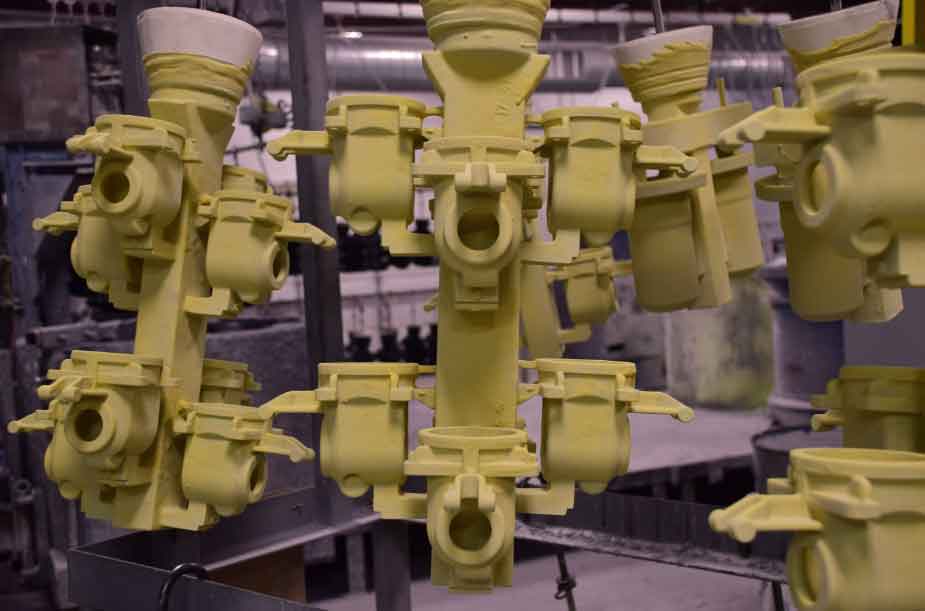
- Design Optimization: Design optimization plays a significant role in improving efficiency. By collaborating closely with designers and engineers, the design can be optimized for manufacturability. This includes reducing complexity, minimizing undercuts, and ensuring uniform wall thickness, which helps streamline the casting process and reduces the likelihood of defects.
- Rapid Prototyping and Digital Simulation: Utilizing rapid prototyping techniques, such as 3D printing, allows for faster production of wax patterns and enables iterative design improvements. Digital simulation tools can predict and optimize the casting process, identifying potential issues and suggesting improvements before the actual casting production begins. These technologies help minimize trial and error, reducing time and material waste.
- Efficient Wax Pattern Production: Improving efficiency in wax pattern production can significantly enhance the overall process. Employing advanced techniques like automated wax injection systems can increase production speed and consistency while reducing manual labor. Additionally, optimizing the gating and runner systems within the wax patterns ensures efficient filling of the molds and minimizes the use of excess material.
- Streamlined Shell Building: Shell building is a critical step in investment casting. Implementing automation and robotic systems for shell building processes can improve efficiency and consistency. Automated dipping systems and controlled shell drying techniques can accelerate the shell building process, reducing cycle times and enhancing productivity.
- Advanced Ceramic Shell Materials: Using advanced ceramic shell materials can contribute to efficiency improvements. High-quality ceramic shells with faster drying times and shorter burnout cycles can reduce overall production time. These materials also offer better thermal stability, which minimizes the risk of shell cracks or defects during the casting process.
- Optimized Casting Parameters: Carefully selecting and optimizing casting parameters, such as pouring temperature, mold preheating, and solidification time, can improve efficiency and casting quality. Precise control of these parameters helps achieve faster solidification, reduces the likelihood of defects, and optimizes the use of energy and resources.
- Automation and Robotics: Integrating automation and robotics into various stages of the investment casting process can enhance efficiency. Automated systems can be employed for tasks like wax pattern assembly, shell building, mold handling, and even casting finishing operations. Robotic arms can perform precise and repetitive tasks, increasing production speed, reducing errors, and improving overall efficiency.
- Supply Chain Management: Efficient supply chain management is crucial for minimizing delays and optimizing resource utilization. Ensuring timely availability of raw materials, consumables, and equipment parts can help avoid production bottlenecks and maximize efficiency. Collaborating closely with suppliers and implementing just-in-time inventory strategies can streamline the overall process.
- Continuous Improvement and Lean Manufacturing: Embracing lean manufacturing principles and implementing continuous improvement initiatives can drive efficiency gains in the investment casting process. Encouraging employee involvement, promoting a culture of innovation, and conducting regular process evaluations and optimizations can help identify and eliminate waste, reduce cycle times, and improve overall efficiency.
By implementing these strategies and techniques, manufacturers can enhance efficiency in the investment casting process, leading to improved productivity, reduced costs, shorter lead times, and increased competitiveness in the market.