As shown in Figure 1, due to the symmetrical arrangement of rollers, the weight of the mold is shared equally by four rollers, and the force acting on each roller is borne by a pair of rolling bearings. According to the force analysis, it is easy to get the normal force F between the mold and each roller and the force fr acting on each rolling bearing.
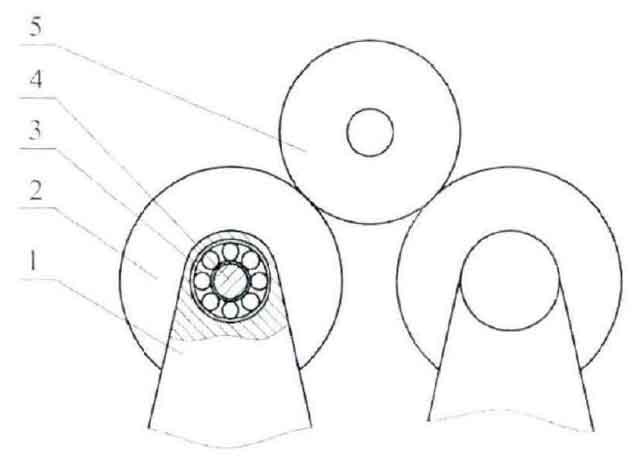
As shown in Figure 2, the stiffness of each roller support of horizontal centrifugal casting machine can be regarded as the series connection of bearing support stiffness K1, roller shaft stiffness scale K2 and contact stiffness K3 between roller and mold. At the same time, each roller bearing has damping C1,. Then the stiffness and damping of single roller support can be obtained as follows:
Since the rolling bearings used in the roller supported furnace tube centrifugal casting machine are mostly self-aligning ball bearings, the stiffness and damping of self-aligning ball bearings are studied.
The stiffness of rolling bearing is composed of Hertz contact stiffness and oil film stiffness between roller and raceway. According to Hertz’s point contact deformation formula, the elastic approach of ball and single raceway in contact normal direction is obtained

Where, q is the normal contact load, K, F and E are ellipticity, complete elliptic integral of the first kind and complete elliptic integral of the second kind respectively
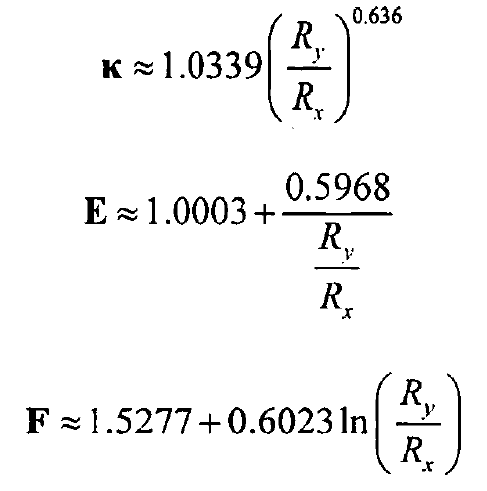
For self-aligning ball bearings, the expressions of Rx and ry are as follows:
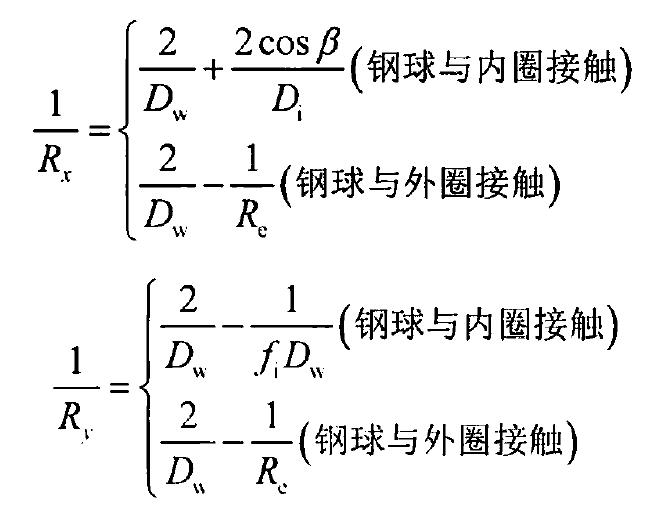
Where, β is the contact angle, DW is the diameter of the steel ball, re is the spherical radius of the outer raceway, Di is the diameter of the contact point between the rolling element and the inner raceway, as shown in Figure 3, FI is the groove curvature radius coefficient of the inner raceway.