The cooling rate during the solidification process of a casting has a significant impact on both the shrinkage behavior and microstructure of the final product. Understanding the relationship between cooling rate, casting shrinkage, and microstructure is crucial for optimizing casting processes and achieving desired material properties. In this article, we explore the influence of cooling rate on casting shrinkage and microstructure and its implications for casting production.
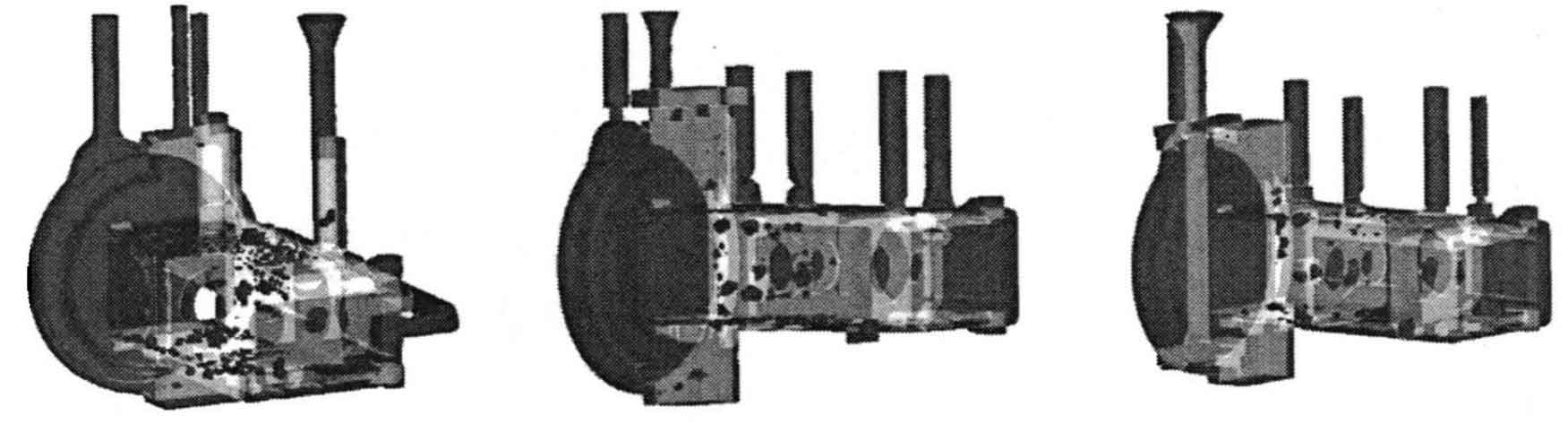
- Solidification Behavior: The cooling rate directly affects the solidification behavior of the molten metal. Rapid cooling rates promote faster solidification, resulting in finer and more uniform microstructures. Slower cooling rates allow for more extended solidification times, leading to larger grain sizes and potentially coarser microstructures. The choice of cooling rate can be tailored based on the desired material properties and casting requirements.
- Shrinkage Behavior: Cooling rate influences the shrinkage behavior of the casting. Faster cooling rates can lead to increased shrinkage due to the reduced time available for the molten metal to feed and compensate for volume contraction. Slower cooling rates, on the other hand, can allow for more efficient feeding and reduced shrinkage. By optimizing the cooling rate, foundries can control and minimize shrinkage defects such as porosity and voids.
- Microstructural Features: Cooling rate affects the formation and distribution of microstructural features within the casting. A higher cooling rate promotes the formation of finer and more dispersed phases, resulting in enhanced mechanical properties such as strength and hardness. Slower cooling rates can encourage the growth of larger grains, which may impact the material’s mechanical properties differently. Proper control of cooling rate can help achieve the desired microstructure for the casting.
- Solidification Time: Cooling rate directly affects the solidification time of the casting. Faster cooling rates reduce the time available for the molten metal to solidify, potentially leading to incomplete solidification or non-uniform cooling. Slower cooling rates allow for longer solidification times, enabling more controlled and uniform cooling. Finding the optimal balance between cooling rate and solidification time is crucial to ensure complete solidification and minimize defects.
- Process Control and Parameters: Achieving the desired cooling rate requires effective process control and the optimization of various parameters. Factors such as mold material, mold design, mold coating, cooling system design, and the use of chills or insulation can influence the cooling rate and subsequent shrinkage and microstructural behavior. Proper selection and optimization of these parameters based on the specific casting requirements are essential for achieving the desired cooling rate and resulting properties.
Evaluating the influence of cooling rate on casting shrinkage and microstructure is vital for optimizing casting processes and achieving the desired material properties. By carefully controlling the cooling rate through appropriate process parameters and design considerations, foundries can tailor the microstructural characteristics and minimize shrinkage defects. This knowledge allows for the production of high-quality castings with improved mechanical properties and dimensional accuracy.