The nominal composition of the experimental alloy is shown in Table 1. The raw materials are: al-24.45% Si master alloy, pure Al (99.8%), pure Fe (99.9%), pure Ni (99.99%), pure Cu (99.99%) and pure Mg (99.9%).
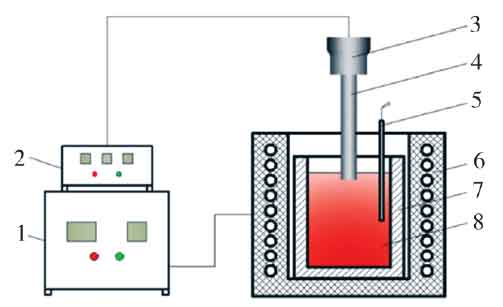
The alloy was melted at 800 ℃ and degassed in argon atmosphere for 10 min. After standing for a period of time, adjust the temperature to 750 ℃ for standby. The ultrasonic treatment is carried out in an ultrasonic vibration device as shown in Fig. 1. Ladle a certain amount of alloy liquid into the preheated metal sample cup and place it in the holding furnace. Put down the ultrasonic vibration head and immerse it in the melt for 15-20 mm. When the melt temperature drops to the starting temperature, start the ultrasonic vibration immediately. The vibration temperature range of A1 and A2 alloy is 650-625 ℃ and 665-640 ℃, respectively, and the vibration time is 90 s. After ultrasonic treatment, the melt was poured into the die cavity of the extruder which had been preheated to about 200 ℃. The upper and lower directions were pressurized at the same time. After holding for 60s, the casting was ejected. The size of the parts was 30mm × 80mm, and the pressure used was 0, 100, 200 and 300mpa. In order to study the effect of ultrasonic treatment on alloy solidification, the aluminum alloy melt without ultrasonic treatment (with the same melting process and melt quality) was directly poured into the extrusion die cavity at 700 ℃ for comparative analysis.
A section of sample with a length of 10 mm was taken from the upper end of rheo extrusion sample. After inlaying, grinding and polishing, the alloy was corroded with 5% NaOH solution. The microstructure and phase composition of the alloy were analyzed by Quanta 200 scanning electron microscope (SEM) with energy dispersive spectrometer (EDX). Using the metallographic analysis software developed by our research group to calculate the grain size of iron rich phase, each group of samples under the same magnification in different areas take 10 photos, analyze the phase size in the photos and calculate the average size. The other half of the rheo extrusion samples were treated by T6 heat treatment (solution solution at 510 ℃ for 7h and artificial aging at 190 ℃ for 10h) and processed into room temperature tensile samples as shown in Fig. 2. Tensile tests at room temperature were carried out on ag-ic100kn Shimadzu universal material testing machine, and the tensile rate was 1 mm / min. Three groups of samples were tested under the same condition, and the average value was obtained.