1. Alloy melting
The alloy was melted in 500 kg medium frequency induction furnace in air atmosphere. The raw materials used in the experiment are alloy, including 20CrMnTi scrap, high carbon ferrochromium, high carbon ferromanganese, ferromolybdenum and carburizing agent. In the smelting process, the temperature is controlled at 1480 ~ 1500 ℃, and the final temperature is rapidly raised to control the deoxidation at 1480 ℃ (0.5 wt.% ferromanganese is added in the furnace for pre deoxidation, 0.25 wt.% ferrosilicon is added in the furnace for initial deoxidation, and 0.05 wt.% aluminum is added in the ladle for final deoxidation).
2. Alloy casting
Before casting, the ladle, runner and mould are preheated in advance by special preheater, the mould is preheated to about 200 ℃, and the ladle and runner are preheated to about 1000 ℃. The patented liquid forging coating is used to spray the mold cavity and parting surface. During spraying, the parting surface and cavity should be free of impurities, bulges or depressions. The coating needs to be re sprayed with a thickness of 0.3 mm for each pouring furnace, and the coating needs to be fully dried before pouring.
The melted alloy was transferred to the preheated ladle for pouring by stages, and the weight and temperature before pouring were measured at the same time. Because the liquidus of chromium white cast iron is 1300 ℃, the pouring temperature is 1250 ~ 1300 ℃, the tapping temperature is 1500 ℃, and the air cooling rate is about 200 ~ 400 ℃ / min. therefore, it is necessary to ensure the pouring within 10 s at 1300 ± 20 ℃ (monitored by infrared thermometer). In addition, when tapping, the predetermined amount should be measured, and the tapping amount should be 5 ~ 10% greater than the required pouring amount.
According to the different composition of the alloy, different pressure parameters set, hypoeutectic composition alloy 1 # 1 furnace, three times pouring, a total of three mold; The alloy with near eutectic composition was cast in 5 times in 2 # 1 heats.
3. Pressure casting
The preparation of plate hammer samples was carried out on y32-1600t four column vertical liquid forging machine. The main experimental parameters were the specific pressure value, and the other main parameters were pouring temperature, mold preheating temperature and holding time. The pouring temperature is measured by infrared thermometer (measuring temperature range: 1000 ~ 3200 ℃) before alloy pouring, and the preheating temperature of die is measured by hand-held infrared thermometer (measuring temperature range: 50 ~ 1600 ℃) inside the die before pouring. The holding time can be deduced according to the square root law. The solidification time of plate hammer is about 194 s, so the holding time is set to 200 s.
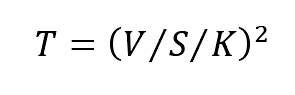
Where:
T — solidification time (min);
V — volume of specimen (mm3);
S — surface area of test piece (mm2);
K – solidification coefficient (cm / Min1 / 2), 2.0 cm / Min1 / 2 for cast iron metal mold casting
The relevant parameters of liquid die forging machine are set as experimental values, and different pressure parameters are modified in the process of different pouring times in the same furnace. After the hydraulic forging machine has completed a series of operations, such as pouring, mold closing, pressure maintaining and ejection, the formed specimen is taken out.
4. Specimen cooling
The purpose of this experiment is to find out the effect of pressure on solidification structure including phase composition of chromium white cast iron. However, the heat treatment of the sample will have an effect on the solidification structure, and the secondary phase transformation will appear, which makes the research process more complicated. Therefore, all the specimens in this study were characterized in as cast condition without heat treatment. However, the test piece after molding needs to be cooled slowly in the air under the package of thermal insulation material. This is because the size of the plate hammer test piece is large, and it is easy to crack if the cooling speed is too fast in the process of air cooling.
5. Sampling scheme
After the plate hammer specimen is cooled naturally, the cutting dimension is 225mm at the position under the indenter near the working face of the plate hammer × 225mm × The metallographic specimen, impact toughness specimen and impact wear specimen are obtained by using 110mm test block. The top, center and bottom parts of the test block near the edge of the die are used as microstructure contrast samples at different positions. The specific sampling positions are shown in the figure. Under different pressure test conditions, the same position of the sample is obtained, and the sample contains: three 10mm × 10mm × In the process of cutting, the sections with different orientations should be marked and the orientation of the contrast samples should be the same, which can be used for SEM and XRD analysis; Three 10mm × 10mm × 30mm specimen for hardness test and impact wear test; Three 10mm × 10mm × 55mm.
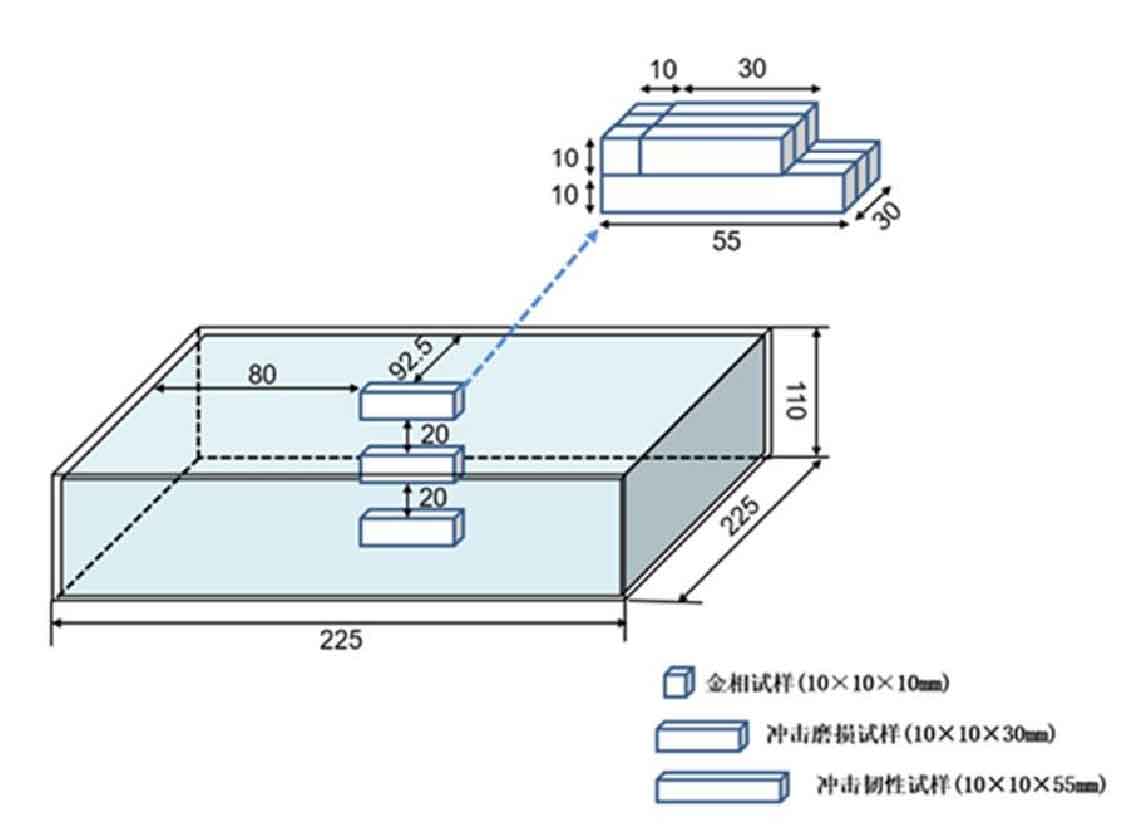
The numbering rules of samples are: alloy composition + pouring times (different pressure) + sampling position. The samples are divided into alloy 1 and alloy 2 according to different alloy compositions; The number of pouring times under different pressure is 1 ~ 5; The marks of the upper, middle and lower positions are top, middle and bottom. For example, alloy 1 with low chromium white cast iron composition is No. 1-1-m in the middle of the specimen under normal pressure (the first pouring).