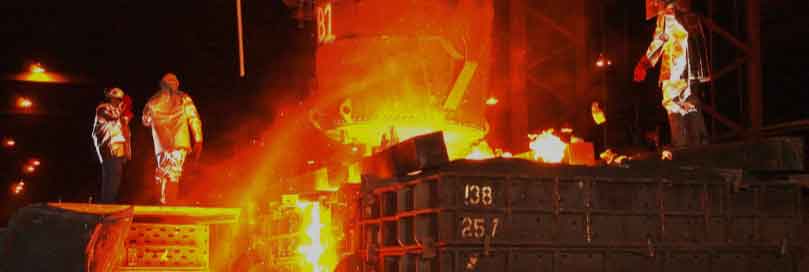
Foundry technology has been a cornerstone of manufacturing for centuries, playing a crucial role in the production of metal components and products. In recent years, advancements in foundry technology have revolutionized the manufacturing industry, enabling faster, more efficient, and cost-effective production processes. Here are some key advancements that have contributed to this revolution:
Digitalization and Automation:
The integration of digital technologies and automation has transformed foundry operations. Computer-aided design (CAD) and computer-aided manufacturing (CAM) systems allow for precise and complex designs to be created and translated into manufacturing instructions. Automation systems, such as robotic arms and automated material handling, have streamlined production, reducing human error and improving efficiency.
Additive Manufacturing (3D Printing):
Additive manufacturing, often referred to as 3D printing, has emerged as a disruptive technology in the foundry industry. It enables the production of intricate and complex metal parts with reduced material waste and faster turnaround times. 3D printing also allows for design optimization, customization, and the production of small-batch components economically.
Advanced Simulation and Modeling:
Foundries are increasingly using advanced simulation and modeling tools to optimize their processes. Computational fluid dynamics (CFD) simulations help analyze and improve the flow of molten metal, reducing defects and improving casting quality. Finite element analysis (FEA) is used to simulate structural performance, allowing for design optimization and weight reduction without sacrificing strength.
Improved Materials and Alloys:
Foundries are continuously exploring new materials and alloys to enhance the properties of cast components. Advanced alloys with improved strength, durability, and heat resistance are being developed, expanding the range of applications for cast metal products. The use of lighter alloys also contributes to weight reduction and fuel efficiency in industries such as automotive and aerospace.
Energy Efficiency and Sustainability:
Foundries are adopting greener practices to minimize environmental impact. Energy-efficient technologies, such as induction melting furnaces and regenerative burners, help reduce energy consumption and greenhouse gas emissions. Recycling and reusing materials, as well as implementing waste management systems, contribute to sustainable foundry operations.
Real-time Monitoring and Predictive Maintenance:
The advent of the Internet of Things (IoT) has enabled real-time monitoring of foundry equipment and processes. Sensor-equipped machines gather data on temperature, pressure, and other relevant parameters, allowing for proactive maintenance and the early detection of potential issues. Predictive analytics help optimize maintenance schedules, reducing downtime and improving productivity.
Augmented Reality (AR) and Virtual Reality (VR):
AR and VR technologies have found applications in training, quality control, and process optimization within the foundry industry. Virtual simulations enable operators to practice complex tasks before execution, reducing errors and enhancing safety. AR-based quality control systems overlay digital information onto real-world objects, aiding in inspection and defect detection.
These advancements in foundry technology have transformed manufacturing processes, enabling greater flexibility, accuracy, and sustainability. The industry continues to evolve, with ongoing research and development focused on further enhancing efficiency, reducing costs, and expanding the range of materials and applications in the foundry sector.