① The main function of the sprue is to guide molten iron into the runner or runner. According to the different cross-sectional area ratio of components, molten iron flows in two states: full flow and non full flow. When pouring into the cylinder, it is expected that the iron hydraulic head will reach 2500 mm. At the initial stage of pouring, the flow velocity and pressure head of molten iron will be very large after entering the sprue cup. A large pressure difference will be formed between the flow strand of molten iron and the surface layer of sand mold, and the gas and slag will be sucked away, and more seriously, it will be directly flushed into the molten iron in the mold.
② The function of cross runner is to distribute molten iron to the ingate, and at the same time, it also plays a role in preventing the primary oxide slag in the molten iron. According to the empirical equilibrium equation, the critical buoyancy velocity V0 is obtained
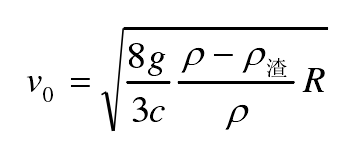
Where:
R-slag radius;
ρ – density of liquid metal;
ρ slag – slag mass density;
G-acceleration of gravity.
It can be seen from the formula that in order to ensure the floating of slag in molten iron, it is necessary to create favorable conditions for slag floating, that is, the slag radius r must be small enough, the velocity of molten iron in the runner is slow enough, the flow of molten iron is stable, and the vortex state is not formed.
③ The main function of ingate is to introduce molten iron into the casting mold, which can effectively control the filling speed and direction. In order to prevent slag inclusion on the surface of the casting, it is necessary to ensure that the process of molten iron flowing into the cavity is smooth and avoid serious oxidation of molten iron caused by splashing and eddy current. The research of other conventional products shows that if the inner runner is used as the blocking section, the molten iron will be seriously ejected during the pouring process, so it must be avoided in the design of the gating system of the inlet cylinder.