The main defect of the inlet cylinder casting in the NDT of VT, MT and Pt is that there are excessive magnetic marks in Mt. Wet fluorescent magnetic powder was used for MT inspection of all areas required by the drawing. The test results showed that there were several surface defects with dense spots and lines exceeding the standard on the air inlet side surface of the intake side of the intake cylinder casting.
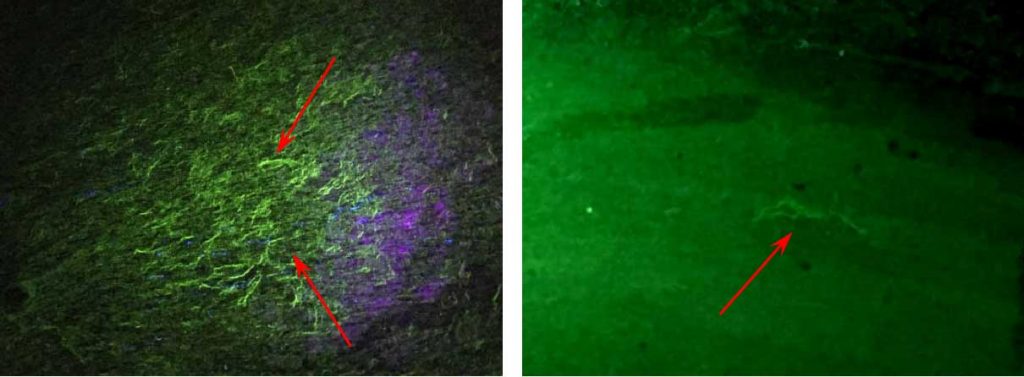
Local polishing and visual inspection were carried out for the defects in the indication of magnetic trace exceeding the standard detected by Mt. Some position defects can be eliminated by slight polishing and then MT again It is found that the defects are mainly fine silica sand particles, coating, refractories and other inclusions. These small impurities are involved in the molten iron during pouring and filling, and then float up to the upper surface of the casting to form surface inclusions. It is a case problem caused by improper control of molding and molding operation process. The process control is strengthened Can be avoided. In addition, the part with more than 80% defect area has local grinding depth of more than 10 mm. During MT re inspection, there are still different degrees of dense cloud spots gathering point defects and linear defects. The formation mechanism of these defects is relatively complex, which needs to be analyzed and studied by relevant detection methods. Its formation mechanism and prevention and control measures are important research objects in this part.