Analysis of part structure
The lifting box is mainly used in petroleum drilling and production equipment. It is made of ZG25CrNiMo, with dimensions of 1040mm×776mm×933mm and a net weight of 1058kg. It is a vulnerable part. The three-dimensional diagram of the lifting box is shown in the figure. The main shape feature is a rotating body. Most of the box wall thickness is 45mm, with the thickest part of 165mm and the thinnest part of 30mm. The structural wall thickness of this part is uneven, and there are large hot spots in some local areas. When the steel liquid solidifies, shrinkage cavity and porosity defects are bound to occur. Therefore, when designing the casting process, risers must be set up at these thick and large hot spot areas for shrinkage compensation.
Process plan
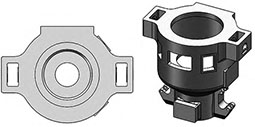
The model is divided into two halves, as shown in the figure. The model making is relatively simple, and it is also convenient for modeling and core placement. After horizontal modeling and core placement, the mold is erected for pouring. As previously analyzed, the structure of this piece is unevenly thick, and there are large hot spots in the thick parts. It is necessary to provide shrinkage by setting up risers. In order to ensure the compactness of the casting structure, the risers must be placed at the left or right end of the casting for shrinkage, and the corresponding other end is poured, as shown in the figure. When using this method for modeling, no matter where the risers and runners are placed, it is particularly difficult to place the risers, and it is also difficult to achieve precise positioning, which is not convenient for workers to operate. Therefore, it is not appropriate to use this method.
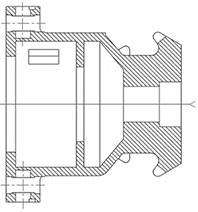
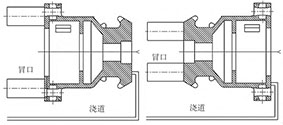
To ensure the effective shrinkage of the riser to the overall casting, especially in the thick and large hot spot area, the preliminary size of the riser is determined to beø300 mm×500 mm, with a total of 4 pieces, evenly distributed on the upper end surface, as shown in Figure 5. The HZCAE11.0 software developed by Huazhong University of Science and Technology is used for numerical simulation of the casting process. The solidification simulation is performed by instant filling of the molten steel and considering the pure temperature field without flow, and the results are shown in Figure.
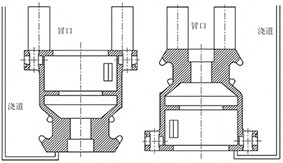
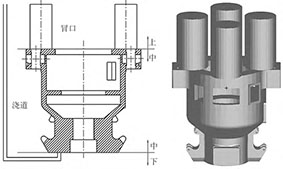
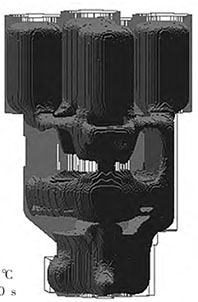
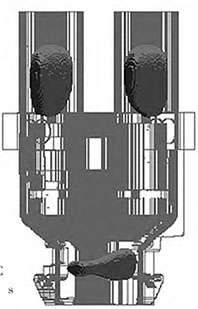
The simulation results showed that when the molten steel solidified to 572 s, there were two obvious isolated areas in the lower part of the lifting box casting, and the risers did not play a significant role in filling these areas. When solidification reached 3552.41 s, the upper part of the lifting box had completely solidified, and the molten steel in the risers was still abundant, but significant centralized shrinkage cavities formed at the lower hot spots, which inevitably affected the fatigue strength and service life of the lifting box. Therefore, this scheme should not be adopted.
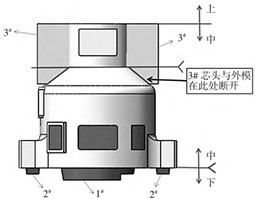
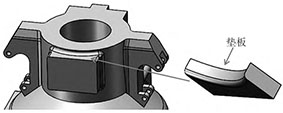
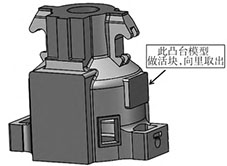
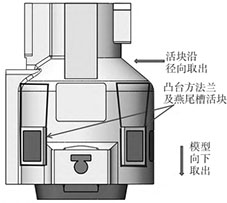
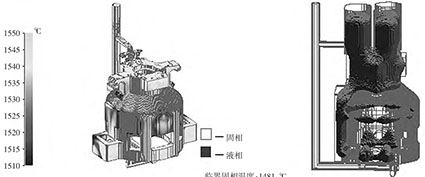
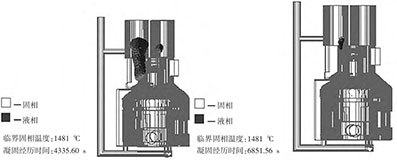
riser design
The correct position of the riser directly affects the feeding efficiency of the riser and the quality of the casting. According to the characteristics of the casting structure, several parts that need to be fed should be divided, and then the size and quantity of the risers for each part should be determined. The riser should be placed in the highest or last solidified part of the casting, and if necessary, chilling measures such as changing the position of the ingate, adding subsidies, using chills or special sand should be taken to form sequential solidification towards the riser. The methods for determining the size of the riser include modular method, cubic equation method, shrinkage liquid method, proportional method, shape factor method, hot spot circle method and tube shrinkage method. Due to the complex structure of this piece, it is difficult to determine the size of the riser using one method. This scheme uses a combination of modular method and computational solidification simulation to determine it.
The final shrinkage cavity is formed at the top of the casting and at the root of the riser, but there is still porosity at the junction of the two walls in the middle of the casting, as well as at the junction of the bottom lifting ring shaft hole and the inner wall. However, it cannot be eliminated by increasing the size of the riser. During molding production, an external chilling iron is placed at the junction of the lifting ring shaft hole and the inner wall, and the molding sand is made of special sand with a higher thermal storage coefficient than silica sand. The sequential solidification of the casting is controlled by chilling, and the feeding distance of the riser is increased, forming a dense structure on the surface of the casting.
conclusion
(1) Select the vertical casting process plan with the large surface where the lifting bail shaft hole is located facing downwards and the lifting lug and thick side wall small end facing upwards.
The lower three-part box shape is designed to accommodate the risers, the main body of the model, the core head, and the sprue. The wooden model includes one outer mold (with the middle section broken off), three core boxes, one movable block base plate, one movable block, and two dovetail groove movable blocks.
(2) The risers were designed using the modular method, and solidification simulations were conducted under pure temperature field and mold filling and heat transfer coupling conditions using the HZCAE11.0 software to determine the shrinkage of a waist-shaped open riser and two cylindrical open risers on the thick wall end surface. The specifications of the two risers were “240 mm×360 mm×400 mm” and “ø240mm×400 mm”. After multiple simulation results showed that the shrinkage cavity in the thick hot spot area was basically eliminated, there were still looseness at the junction of the two walls in the middle of the casting, the junction of the bottom lifting ring shaft hole and the inner wall, but it could not be eliminated by riser shrinkage. In order to eliminate the above defects, an external chilling iron was set at the bottom to achieve better sequential solidification and shrinkage.