Valves, as a universal industrial component, are widely used, mainly in fields such as petroleum, chemical, petrochemical, water conservancy, metallurgy, power, urban construction, machinery, coal, food, nuclear industry, LNG, etc. There are many types of valves with different sizes, specifications, and structures, mainly including ball valves, butterfly valves, control valves, safety valves, gate valves, globe valves, check valves, pressure reducing valves, drain valves, diaphragm valves, etc. The quality ranges from tens of grams to tens of tons, and valve materials vary depending on the working environment, including cast iron, ordinary carbon steel, stainless steel, heat-resistant steel, wear-resistant steel, corrosion-resistant steel (duplex steel), copper alloy, and other materials.
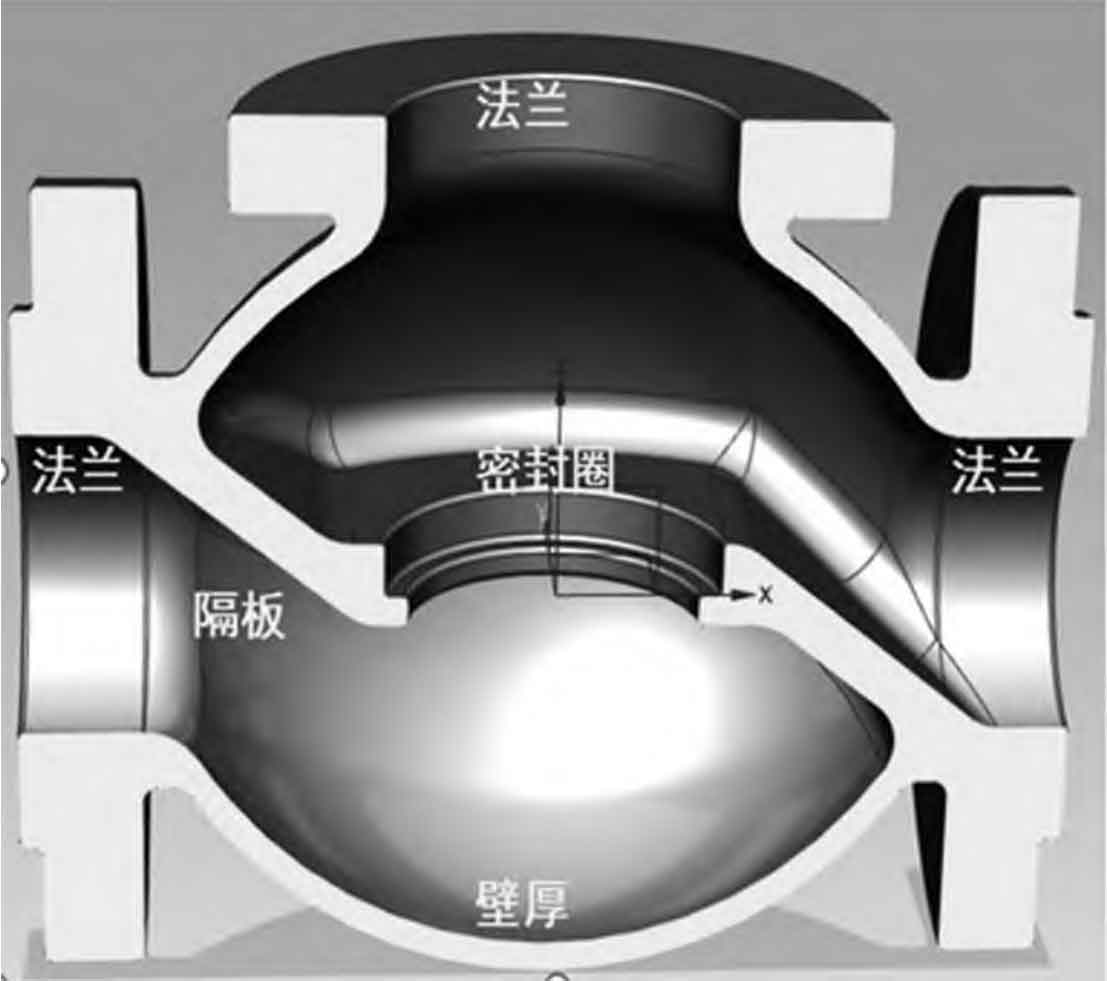
Flow control valve is one of the many valves in the field of industrial automation process control. It is the final control element that changes the process parameters of medium flow, pressure, temperature, liquid level, etc. by receiving control signals output by the regulating control unit and using power operation. The control valve belongs to a hollow structure and has different technical requirements according to different application conditions. The structure of the control valve is relatively complex, with high technical requirements and high casting difficulty. During production, casting defects such as cracks, shrinkage porosity, slag pores, etc. often occur. This article combines the actual situation and work experience of on-site production of flow control valve steel castings in alkaline phenolic resin sand production, mainly analyzes the causes and solutions of crack defects in flow control valves, providing technical reference for valve control in alkaline phenolic resin sand production and improving the quality of steel castings.
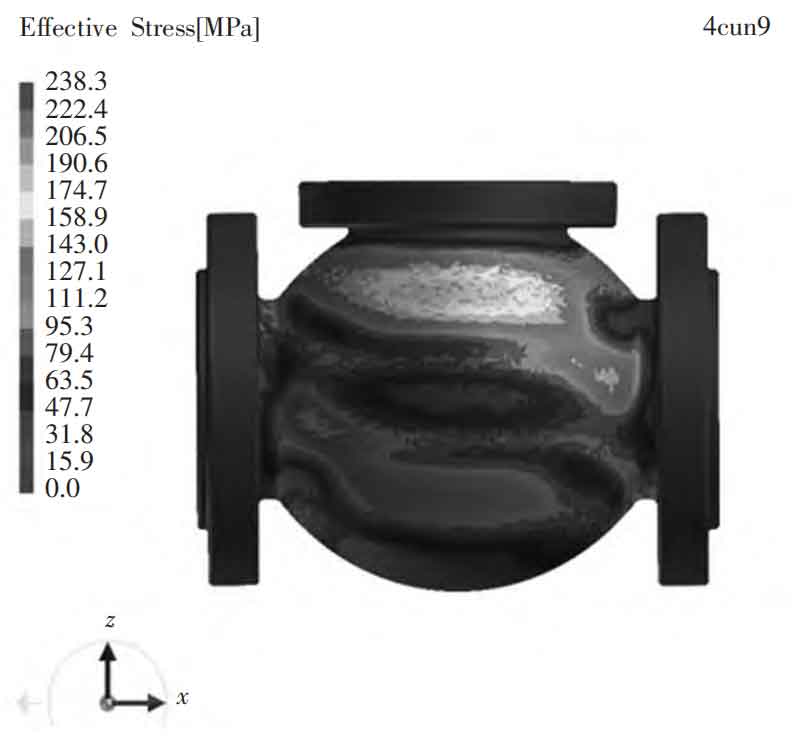
Cracks in valve steel castings can be divided into two types based on the temperature range they form: hot cracks and cold cracks. According to the location of the cracks in the steel castings, they can be further divided into external cracks, subcutaneous cracks, and internal cracks.
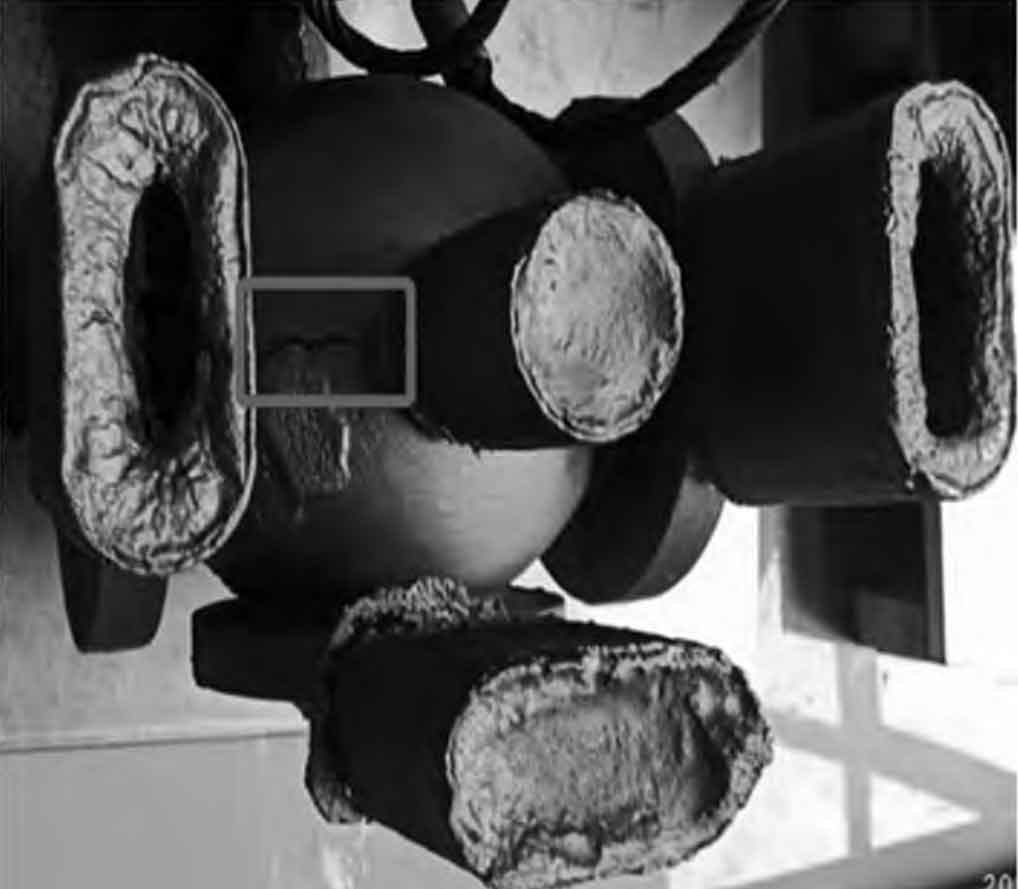
Through structural stress simulation analysis, the stress of the flow control valve is mainly concentrated at the junction of the middle sealing ring and partition (Figure 3) and the middle position of the adjacent two flanges (Figure 4). Actual production has also verified this, with cracks concentrated in these areas. The wall thickness at these locations is uneven, and during the solidification shrinkage process after pouring, uneven stress distribution leads to tensile cracking.
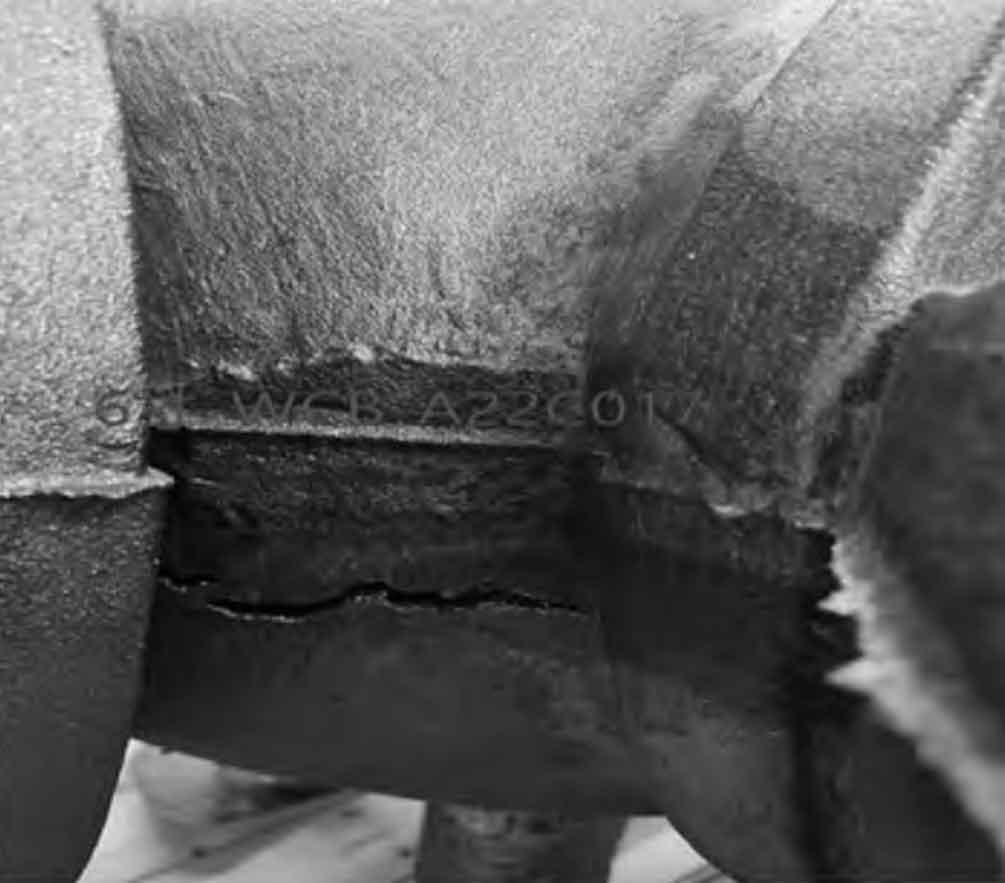
After analysis and multiple experimental verifications, the problem of crack defects in the cast steel parts of flow control valves has been mainly solved from the following aspects.
1. Optimize the structure of steel castings
1.1 Optimize the structure of steel castings themselves
After analyzing the pressure of the flow control valve and calculating the pressure of the partition, the wall thickness of the cast steel component or the thickness of the partition connected to the middle sealing ring can be adjusted appropriately under the pressure conditions to adjust the stress distribution of the cast steel component during solidification shrinkage. By reducing stress concentration, the crack tendency at this point can be reduced or eliminated.
1.2 Increase crack prevention reinforcement
Add anti crack rib plates in the middle of two adjacent flanges of the steel casting, with a thickness of approximately one-third of the wall thickness of the steel casting. During the solidification shrinkage of steel castings, the rib plate preferentially solidifies to form strength to offset the stress generated by adjacent flanges during shrinkage, thereby solving the problem of cracks between adjacent flanges.
2. Adjust styling materials and styling methods
2.1 Adjusting styling materials
During normal production, the sand core is generally shaped with new sand, which has good collapsibility, making it easier to clean the sand inside the mold cavity after pouring. The strength of alkaline phenolic resin sand will increase with the increase of temperature during pouring. Due to the fact that the new sand has not undergone high-temperature phase transformation, thermal expansion, and increased strength, the yield is relatively poor. This leads to the problem of cracks in steel castings due to the resistance of the sand core during solidification shrinkage.
Adjust the sand core molding sand. The sand core is made of calcined sand. After undergoing high-temperature phase transformation, the thermal expansion of the calcined sand in contact with high-temperature molten steel during casting will be reduced. At the same time, the yielding ability is relatively good, and the probability of cracking is relatively low.
Adjust the ratio of sand core resin curing agent by reducing the resin ratio of the sand core by 0.1%~0.2% compared to the resin ratio of the external mold. Adjust the curing agent according to the corresponding ratio, so that the strength of the sand core is lower than that of the external mold. When the steel casting undergoes solidification shrinkage after pouring, the resistance of the sand core will be lower than that of the external mold, thereby reducing the problem of cracks.
2.2 Adjusting the styling method
Adjust the production method of sand core. When making the sand core, the sand core shall be emptied on the premise of ensuring the strength of the sand core. When it is inconvenient to empty, sawdust or foam shall be added, mainly to increase the yield of the sand core and reduce the resistance of the steel casting during solidification shrinkage to reduce crack defects. At the same time, the collapsibility of the sand core with sawdust and foam shall be better, and it is convenient to clean the steel casting cavity.
Adjust the production method of the external mold. During the production of the external mold, the surface sand close to the surface of the steel casting is manually compacted to ensure the compactness of the sand mold. The back sand can be appropriately compacted on the compaction table.
3. Adjust pouring temperature and pouring speed
3.1 Adjusting the pouring temperature
Try to reduce the pouring temperature as much as possible while ensuring good filling of steel castings. For steel castings, especially carbon steel parts, if the pouring temperature is too high, the shrinkage during solidification will increase, and the thermal stress will increase, which will increase the tendency for hot cracking. When the stress exceeds the maximum stress that the steel castings can withstand, the steel castings will crack along the grain boundaries. At the same time, high pouring temperature makes it easy for steel castings to produce sand sticking, which increases the shrinkage resistance of steel castings and thus increases the risk of cracking.
3.2 Adjusting the pouring speed
Slow pouring speed can cause the mold cavity to be heated and baked for too long, resulting in an increase in temperature difference between different parts of the valve, which can easily cause the sand mold to lift and fall off, leading to defects such as cracks, cold shuts, and slag inclusions. By appropriately increasing the pouring speed, the metal liquid can quickly fill the mold cavity, prevent insufficient pouring, reduce metal liquid oxidation, reduce temperature differences in various parts of the steel casting, and thus avoid crack defects.
4. Optimize the smelting process
4.1 Control the content of S, P, and C elements
By controlling the quality of raw materials to reduce the content of harmful elements S and P, S has a prominent impact on the sensitivity of steel to hot cracking, causing steel to develop thermal brittleness and reducing its ductility and toughness; P increases the grain boundary brittleness of steel, increases its cold brittleness, and enhances its crack sensitivity.
Under the premise of meeting the mechanical properties, the C content should be appropriately controlled. The lower the C content, the better the ductility and toughness of the steel, and the lower the tendency of steel castings to produce cracks.
4.2 Control of Mn element composition content
Within the range of less than 1.0%, increasing the Mn content is beneficial for reducing the tendency of hot cracking in steel castings, while above 1.0%, it is prone to sulfur recovery, which is actually unfavorable.
4.3 Adding Elements to Refine Grains
Adding a small amount of elements such as titanium (Ti) and niobium (Nb) during smelting can refine the grain size and effectively improve the crack resistance of steel castings. Experimental results have shown that the effect is very good.
5. Optimize the gating and riser system
Poor design of the pouring system and riser can lead to stress in the steel casting and cracking during solidification shrinkage. The pouring system should be set away from the hot spot of the steel casting, avoiding the location where the thermal stress of the steel casting is relatively concentrated; The riser should also avoid stress concentration areas as much as possible while meeting the requirements of steel casting shrinkage. At the same time, the riser should be used in conjunction with cold iron to change the solidification sequence of the steel casting, reduce the impact of shrinkage stress on the steel casting, and thus reduce the occurrence of cracks in the steel casting.
6. Conclusion
ZHY Casting has solved all the crack problems in the cast steel parts of the flow control valve produced by alkaline phenolic resin sand through the above solutions and production verification in the past six months. In summary, to prevent and eliminate crack defects in the cast steel parts of flow control valves produced by the alkaline phenolic resin sand process, the following measures are mainly emphasized from a production perspective.
(1) Optimize the structure of steel castings and reduce stress concentration areas during solidification shrinkage.
(2) Change the molding materials and methods, use calcined sand as the sand core, empty the sand core, and improve the flexibility of the core.
(3) Adopting high-temperature steel tapping and low-temperature pouring to improve the pouring speed.
(4) Optimize the smelting process, strictly control harmful elements such as S and P, add elements that refine grain size, and improve the crack resistance of steel castings.