Foundry technology plays a significant role in achieving a circular economy by enabling the recycling and reusing of materials. The circular economy aims to minimize waste generation, maximize resource efficiency, and create a closed-loop system where materials are continuously reused and recycled.
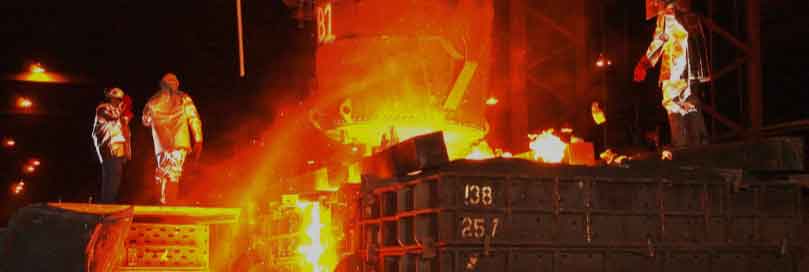
In the context of foundries, which are facilities that produce metal castings, there are several ways in which recycling and reusing materials can be implemented:
1.Scrap Metal Recycling:
Foundries generate a considerable amount of scrap metal during the casting process, which can be recycled. Scrap metal is collected, sorted, and processed to extract valuable metals like iron, steel, aluminum, copper, and others. This recycled metal can then be used as a feedstock for new casting production, reducing the need for virgin raw materials.
2.Mold and Core Material Recycling:
Foundries use molds and cores made of various materials such as sand, clay, and binders. After casting, these molds and cores become waste material. However, they can be recycled by breaking them down, separating contaminants, and reusing the recovered materials in new molds and cores. This approach reduces the consumption of fresh materials and minimizes waste generation.
3.Melting and Purification:
During the casting process, impurities and contaminants may be present in the molten metal. Foundries employ various techniques such as fluxing, refining, and filtration to purify the metal and remove these impurities. The purified metal can then be reused in subsequent casting processes, reducing the need for virgin metal production.
4.Energy Recovery:
Foundries require significant amounts of energy for melting metals and operating various equipment. Implementing energy recovery systems such as heat exchangers and waste heat boilers can capture and reuse the thermal energy generated during the casting process. This helps reduce energy consumption and reliance on fossil fuels, contributing to a more sustainable foundry operation.
5.Design for Recyclability:
Foundries can contribute to the circular economy by collaborating with product designers and engineers to create products that are easily recyclable. Designing products with separable components, avoiding the use of mixed materials, and ensuring proper labeling for material identification facilitates efficient recycling at the end of a product’s life cycle.
6.Life Cycle Assessment:
Foundries can conduct life cycle assessments (LCAs) to evaluate the environmental impact of their processes and identify areas for improvement. LCAs help optimize material selection, energy consumption, waste management, and transportation logistics, leading to more sustainable foundry practices.
It is important to note that implementing recycling and reusing practices in foundries requires collaboration among various stakeholders, including foundry operators, material suppliers, product designers, and consumers. Government regulations and incentives can also play a crucial role in promoting the adoption of circular economy principles in the foundry industry.