The disc of ductile iron punch is an important part of high-speed punch. The main body of high-speed punch is composed of flywheel disc, and its peripheral surface is equipped with several square grooves, which mainly plays the role of weight reduction. The bottom of the disc is equipped with six process holes, and the connection with the rib plate is an arc segment. In order to ensure that the punching pressure of the punch is always uniform and prolong its service life, the disc cannot be deformed.
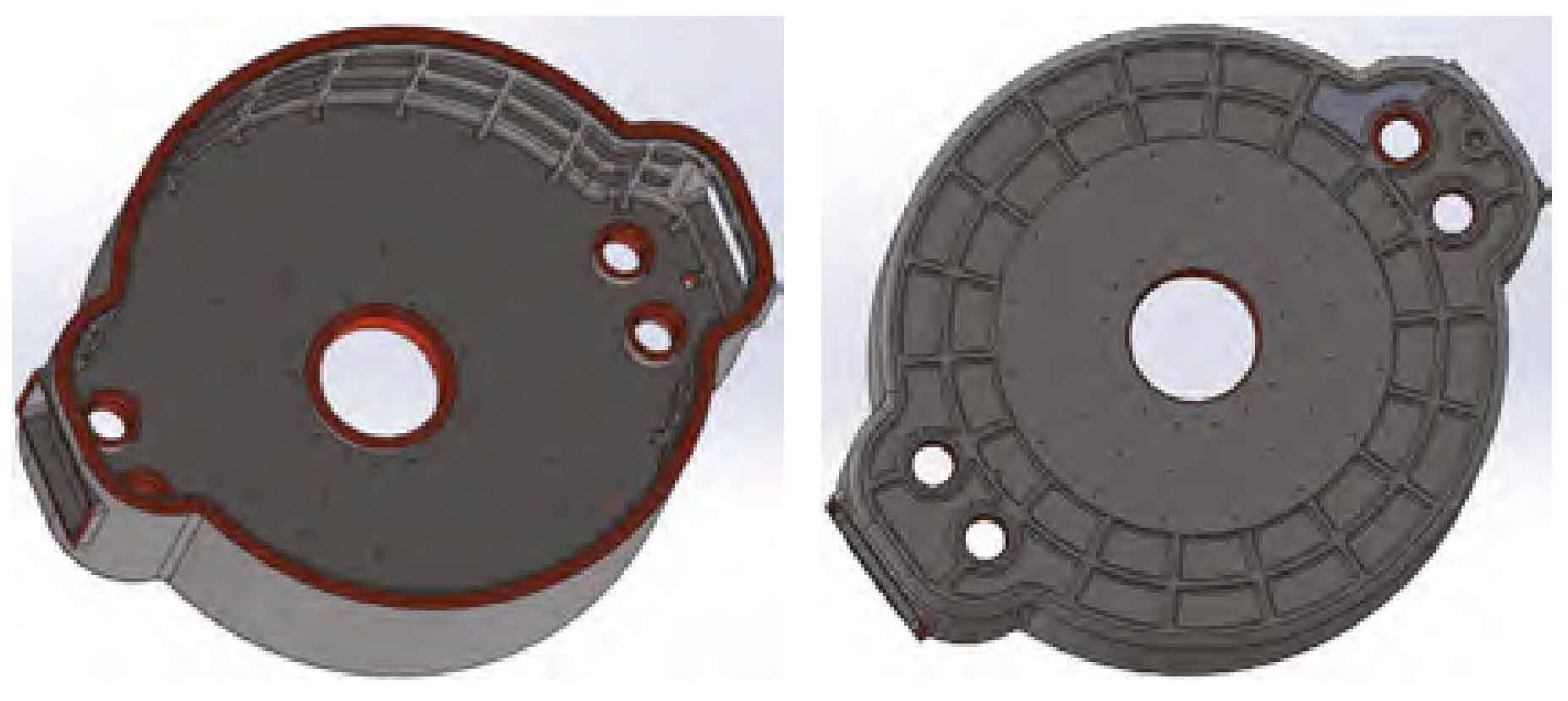
The rough disc of the ductile iron punch has a mass of 38000 kg. The three-dimensional structure is shown in the figure. The total height of the ductile iron is 1700mm, the outer diameter of the disc is 4800 mm, the maximum size is 5820 mm, the main wall thickness is 220 mm, and the wall thickness at the root of the bearing seat hole is the largest, belonging to the hot spot area.
The disc material of ductile iron punch is QT500-7. The mechanical properties of single cast test bar are required to be tensile strength greater than 420 MPa, yield strength greater than 320 MPa, and elongation after fracture greater than 5%.
(1) For the ductile iron disc castings of punch press, the appropriate chemical composition (mass fraction) is carbon equivalent 4.0%~4.2%, silicon 2.1%~2.3%, manganese ≤ 0.5%, residual magnesium content 0.035%~0.055%, rare earth elements 0.01%~0.02%.
(2) Using multiple inoculation, selecting yttrium based heavy rare earth spheroidizing agent, controlling the discharge temperature at 1430~1460 ℃, shortening the solidification time can improve the distribution and morphology of graphite balls.
(3) For large ductile iron castings, try to use bottom pouring with multiple ingates scattered to ensure stable mold filling of molten iron. Chill iron strengthens the cooling of key parts, eliminates or reduces shrinkage defects, and improves the structural density and mechanical properties of castings.
There is a circle of threaded holes on the lower surface of ductile iron, which is matched with the cover, and it is required that there are no loose defects in the holes. Due to the large cavity area of ductile iron, the casting process is difficult. Ductile iron has a great tendency to oxidize. In order to ensure the smooth filling of molten iron, prevent turbulence, reduce slag inclusions, pores and other casting defects, large castings generally adopt bottom injection and semi closed gating systems. In addition, the disc modulus of ductile iron punch is large. Theoretically, riser free casting can be achieved by ensuring the strength of resin sand mold and strengthening the inoculation of molten iron with flow.