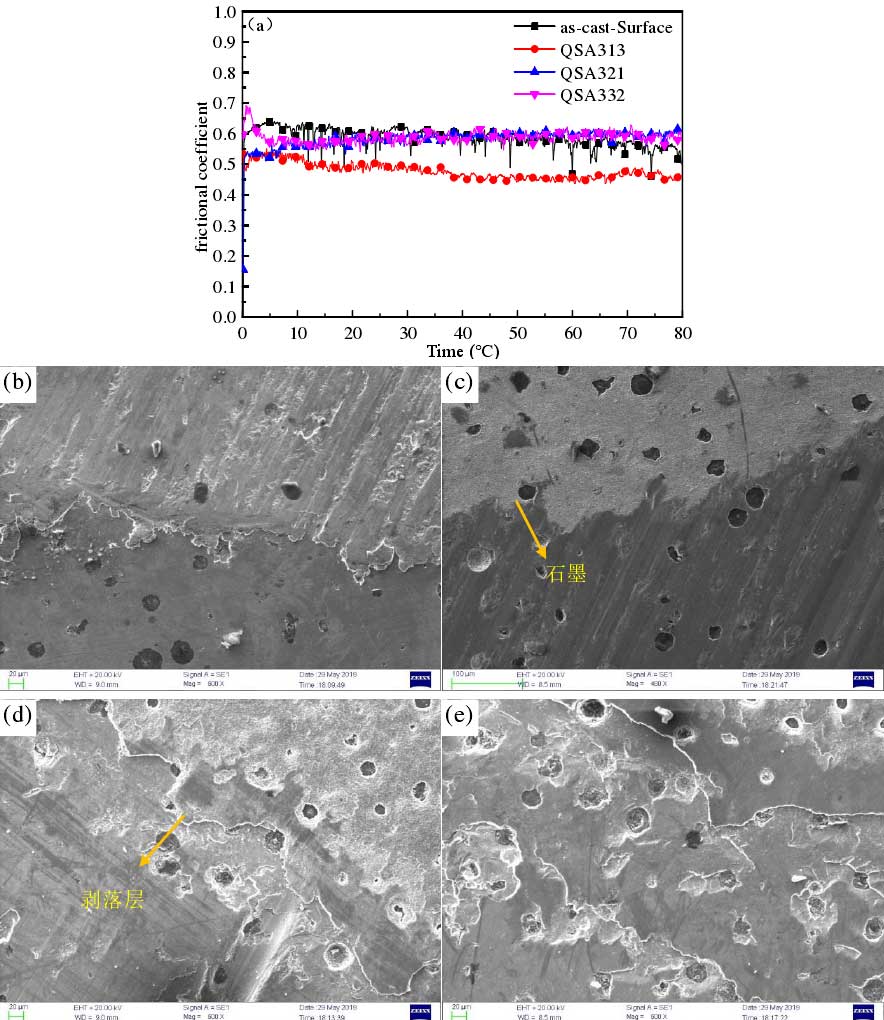
As cast and qsa313 The curve of the two samples first rises and then decreases, and fluctuates greatly. This is because in the test, the micro convex body of the sample rubs against the contact. With the increase of the friction time, when the contact area between the friction pairs increases, there will be adhesion points between the micro convex bodies. With the increase of the contact area, the adhesion points will increase. The friction pair must cut off these adhesion points When the shear resistance is overcome, the friction coefficient increases and the friction is cut off
The coefficient decreases. According to figure (a), the friction coefficients of as cast surface, qsa313, qsa321 and qsa332 are 0.565, 0.451, 0.583 and 0.576, respectively. The wear rates of the above four samples are 3.373, 1.242, 1.345 and 1.416, respectively. The smaller the friction coefficient and wear rate, the more wear-resistant the material is. It can be seen that the wear resistance of the samples after nitrocarburizing is significantly improved compared with that of the as cast samples. This is due to the fact that the surface of Nitrocarburized samples has γ′ – fe2-3n and ε – Fe4N hardening phases, so that the surface of the samples has higher hardness, and the wear resistance is improved.
Figure (b) shows the as cast sample without nitrocarburizing treatment, and figure (c) (d) (E) shows the sample treated at 580 ℃. It can be seen from the figure that there are furrow like scratches on the surface of the sample, and at the same time, there are many fine abrasive particles attached to the surface. This is because during the test, the load on the test sample will squeeze and shear the sample, and a small amount of material on the friction contact surface of the sample will fall off. These are called abrasive particles. At this time, the main wear mechanism is abrasive wear.
Figure (b) there are very obvious furrows on the surface of the sample, and the friction surface has a “scaly” appearance. This is due to adhesive wear on the surface of the sample, and there will be many deep and obvious wear marks on the surface. With the extension of test time, more wear particles fall off due to plastic deformation of the material. At this time, the mechanism changes from slight adhesive wear to severe adhesive wear, and the wear rate increases.
In figure (c), in addition to shallow furrow, there is no spalling pit in the sample. After nitrocarburizing, the surface hardness of the sample is high, and the ε phase is a layered close packed hexagonal structure, which is difficult to adhere to the metal, so it is important to reduce the friction coefficient and reduce the wear. Although the hardness of γ′ phase is relatively low, it is easy to produce cracks in the friction process. However, due to its face centered cubic structure, its anti-wear effect is excellent. At the same time, the existence of graphite also plays a certain role in lubrication. Therefore, the surface condition of the samples prepared by this process is good, and its friction coefficient and wear rate are the lowest.
In figure (d) (E), there are scale like surface layer and spalling pit on the surface of the sample, and the wear mark is also deep. At this time, the wear mechanism of the material is adhesive wear and abrasive wear. In this process, it is easier to produce wear debris. Therefore, the friction coefficient of the samples under the two processes is higher, so it is not wear-resistant.
Through the comprehensive balance method, the combination of the optimal factors and levels in this experiment was selected. First, the indicators were analyzed to find out the influencing factors and the optimal production scheme under each index. According to the actual situation, the analysis results of each index were comprehensively compared, and the optimal parameters under each level were obtained, taking into account the best conditions under each index.
The results of range analysis and variance analysis show that the primary and secondary relationship of the three factors on the thickness of the sample layer is t > s > t; the primary and secondary influence on the surface hardness of the sample is t > s > t T > t > s; the primary and secondary influence on microhardness (effective hardening depth) and wear resistance is t > s > t. Considering the actual working conditions, improving the material wear resistance and effective hardened layer depth is the main means to solve the deformation problem of piston pump cylinder block in the working process. Therefore, the influence of various factors on the primary and secondary relationship of the two indexes is given priority. The influence of infiltration temperature T is the largest, and the gas proportion s is the second. T is the main factor for the comprehensive score of friction and wear and the effective depth of hardened layer, but it is a secondary factor for the surface hardness, and has the least influence on the thickness of the carburized layer. The influence of the time t on the surface hardness and the thickness of the layer is the greatest. Due to the different importance of indicators, the relatively important factors should be considered first when selecting the optimal level under the factors, so the order of analysis is t > s > T. from the perspective of trend, economic analysis and primary and secondary factors, the optimal condition is 580 ℃ × 4 h, NH3: CO2 is 4:1.