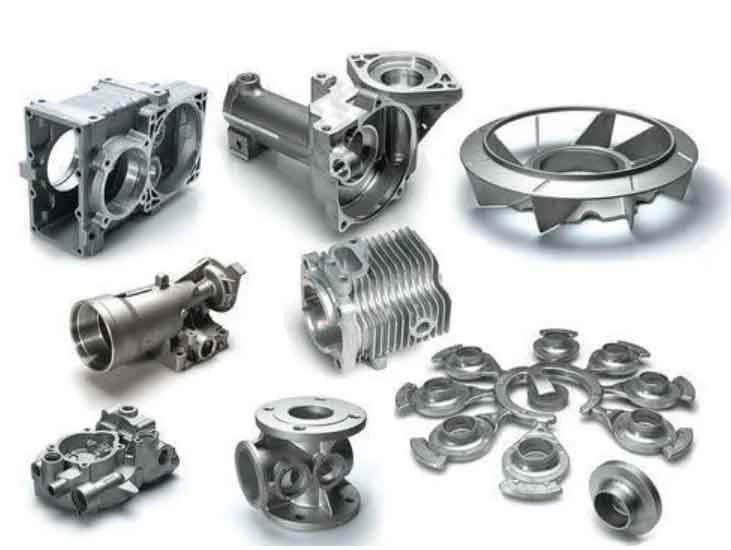
Grey cast iron is a fascinating material that has been used for centuries in various industries, thanks to its unique properties and versatile applications. Unraveling the secrets of grey cast iron involves understanding its metallurgical characteristics and the machining techniques used to produce intricate components. Let’s take a closer look at these aspects:
1. Metallurgy of Grey Cast Iron:
Grey cast iron is primarily composed of iron (Fe), carbon (C), and silicon (Si). Its microstructure consists of graphite flakes embedded in a matrix of ferrite and pearlite. The presence of silicon promotes the formation of graphite, which gives the material its gray appearance when fractured.
Graphite Formation:
During solidification, silicon favors the formation of graphite over cementite (iron carbide). The graphite flakes act as lubricants, providing excellent wear resistance and damping properties. The size, shape, and distribution of the graphite flakes influence the material’s properties.
Matrix Composition:
The matrix in grey cast iron contains ferrite and pearlite. Ferrite is a soft, ductile phase, while pearlite is harder and more brittle. The proportion of ferrite and pearlite affects the mechanical properties, such as hardness, strength, and ductility.
Alloying Elements:
Alloying elements like manganese, nickel, chromium, and copper can be added to modify the properties of grey cast iron. They influence the microstructure and enhance strength, wear resistance, corrosion resistance, and other desirable characteristics.
2. Machining Techniques:
Machining grey cast iron requires specific techniques due to its microstructure and hardness. Here are some key aspects of machining grey cast iron:
Tool Selection:
Due to the abrasive nature of graphite flakes, special tool materials like carbide or ceramics are preferred for machining grey cast iron.
Cutting Parameters:
Proper cutting speeds and feeds must be used to prevent excessive tool wear and maintain dimensional accuracy.
Coolant Usage:
Coolant is often employed during machining to dissipate heat and prevent damage to the cutting tool.
Avoiding Chatter:
The damping capacity of grey cast iron makes it prone to chatter during machining. Careful tool selection and setup can help minimize this issue.
Surface Finish:
Achieving a smooth surface finish may require appropriate tooling and finishing processes, as the graphite flakes can influence the surface texture.
Grinding:
Grey cast iron is often ground to achieve precise dimensions and surface characteristics, taking advantage of its hardness and wear resistance.
3. Heat Treatment and Stress Relief:
In some cases, heat treatment and stress relief processes are employed to modify the microstructure and reduce internal stresses. Annealing, normalizing, or stress relieving can improve machinability and enhance specific mechanical properties.
Understanding the metallurgical composition and machining techniques for grey cast iron is essential for producing high-quality components in various industries. Its unique microstructure, enhanced by alloying elements and controlled heat treatment, contributes to the material’s versatility and performance. Through effective machining practices, manufacturers can harness the potential of grey cast iron for a wide range of applications.