The steel castings manufacturing process is a complex and precise method of transforming molten metal into intricate and durable components. It involves several stages, each carefully executed to ensure the production of high-quality steel castings. Here is a step-by-step look inside the steel castings manufacturing process:
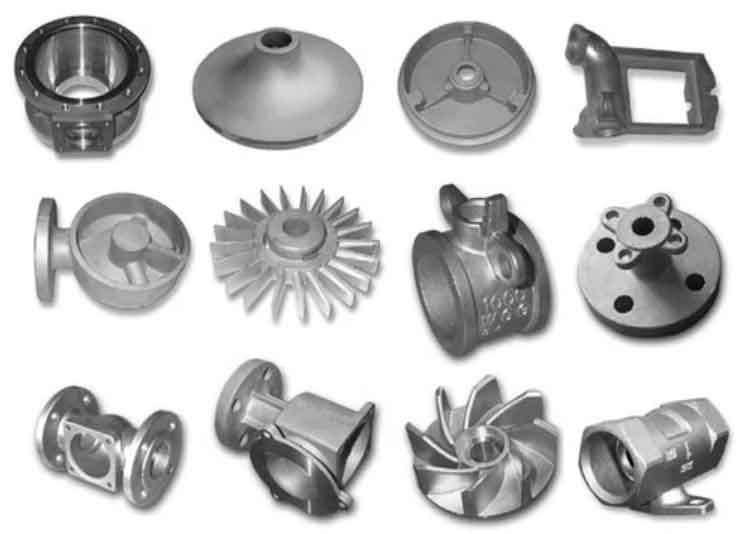
- Pattern Making: The process begins with the creation of a pattern, which is a replica of the final casting in the desired shape and size. Patterns can be made from wood, metal, or plastic and are used to create the mold.
- Mold Making: The pattern is used to create a mold, which is made of a refractory material like sand. The mold is formed by packing the sand mixture around the pattern to create a negative impression.
- Pattern Removal: Once the mold is formed, the pattern is removed, leaving a cavity in the sand that matches the shape of the desired casting.
- Melting: The next step is melting the steel. Electric arc furnaces or induction furnaces are commonly used to heat the steel to its melting point.
- Pouring: Once the steel is melted, it is poured into the mold cavity. The pouring process must be carefully controlled to prevent defects like porosity and ensure that the molten metal fills the entire mold.
- Cooling and Solidification: After pouring, the molten metal cools and solidifies within the mold, taking the shape of the cavity.
- Shakeout: Once the casting has solidified, the mold is broken open, and the newly formed casting is removed. Any excess sand is removed during this step.
- Cutting and Cleaning: The casting is then cleaned to remove any remaining sand or impurities. It may also undergo cutting or trimming to remove any unwanted material.
- Heat Treatment: Some steel castings may undergo heat treatment to enhance their mechanical properties and improve their performance.
- Inspection: The final step involves inspecting the casting to ensure it meets the required specifications and quality standards. Non-destructive testing methods such as ultrasonic testing or X-ray inspection may be used to detect any internal defects.
- Finishing and Machining: Depending on the application, the casting may undergo additional finishing and machining processes to achieve the desired final shape and surface finish.
- Surface Treatment: The steel castings may receive surface treatments such as painting, coating, or galvanizing to enhance corrosion resistance and appearance.
The steel castings manufacturing process requires expertise, precision, and attention to detail to produce high-quality components used in various industries, including automotive, aerospace, construction, and more. It is a critical part of modern manufacturing that enables the creation of complex and durable parts that form the backbone of many industrial applications.