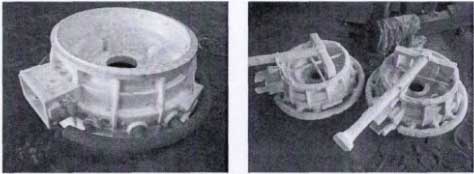
(1) Prevent sand sticking of castings. After the coating penetrates into the surface of the sand mold (core), fill the gap between the sand particles on the surface to prevent the metal liquid from penetrating into the surface to form mechanical sand sticking; Prevent chemical reaction between molten metal and mold, form low melting point substance and cause chemical sand sticking;
(2) Strengthen the surface strength of sand mold (core), reduce and prevent sand inclusion, sand washing, sand holes and other defects of castings.
(3) Reduce the surface roughness of castings. Because the refractory aggregate particles in the casting coating are very fine, the surface of the casting mold coated with the coating is smooth, which reduces the surface roughness of the casting and improves the surface finish of the casting.
(4) Control the cooling rate of castings to prevent shrinkage cavity, crack and other defects.
(5) Improve surface properties of castings. Alloying elements are added to the coating, and casting infiltration technology is used to make the surface of the casting alloy or refine the structure, so as to improve or change the surface composition, structure and properties of the casting.
(6) It can absorb and shield sulfur, carbon and other gases from furan resin sand mold to prevent local ball milling and compilation of ductile iron castings, casting inclusions (slag), sulfur penetration cracks of special steel, carburization defects of stainless steel, etc.
(7) The thermal decomposition of the coating has less gas and low nitrogen content, which can prevent pore defects.