Connecting rod is an important part of diesel engine. The surface quality, such as quenching cracks, directly causes the scrapping of parts. However, the internal quality, such as structure, performance and micro cracks, is not easy to be found in production, but may cause serious consequences. The connecting rod has complex shape and uneven thickness, so it is easy to crack during quenching and tempering.
Connecting rod forging is carried out at 1150 ± 50 ℃, which results in coarse austenite grains in forgings. After cooling to room temperature, coarse pearlite structure is formed. Because the structure is hereditary, the forged connecting rod is directly quenched to obtain coarse lamellar martensite. However, the formation of cracks is largely determined by the size of martensite sheets. Large martensite sheets promote the formation of cracks, while small martensite sheets reduce the formation of cracks. This is because the crack is formed by mutual collision of martensite during its growth. The martensite formation speed is very fast. When it collides with each other or with austenite grain boundary, considerable stress field is caused by impact. Because martensite is very brittle, it can not eliminate stress through slip or twin deformation, so it is easy to form impact microcracks. Under the action of thermal stress and structural stress, microcracks expand into macro cracks. At the same time, the existence of microcracks will significantly reduce the fatigue life of parts, especially the plasticity and toughness become very poor. When the connecting rod is forged at high temperature, not only coarse pearlite structure is formed when it is cooled after forging, but also the pre eutectoid ferrite may precipitate in a network along the austenite grain boundary to form network ferrite. The widmanstatten structure can be formed only at a certain cooling rate. After forging, air cooling is beneficial to the diffusion of Fe atoms due to the high heating temperature of the workpiece. The formation of network ferrite increases the concentration of carbon atoms in austenite, and then forms the widmanstatten structure when further cooling. The reticular ferrite and widmanstatten structure can not be eliminated due to low temperature during quenching, and play the role of cutting the machine body. At the same time, the specific volume of martensite is large. When martensite transformation occurs, the volume expands rapidly, while the reticular ferrite and widmanstatten structure hinder martensite expansion and form a large stress, which is easy to cause the expansion of quenching microcracks and form quenching macroscopic cracks.
During the inspection of the heat-treated connecting rod, cracks were found at the root of its small end, as shown in the figure. Take samples at crack a and B for microscopic inspection. There is oxide in crack a, decarburization on both sides, and the crack is distributed in an arc; There is no oxide and decarburization in the crack at B. A crack conforms to the characteristics of forging crease, which belongs to forging crease; The crack at B was formed by the crack at a after quenching. If there are defects on the metal surface or inside, when the material is transformed from austenite structure to martensite structure during quenching, due to the effect of structural stress and thermal stress, the defect will become the stress concentration point, which will produce cracking or crack propagation, which is a form of quenching crack. Not only the crease will cause crack propagation during quenching, but other defects on the surface or inside of the connecting rod will also cause crack propagation or crack generation.
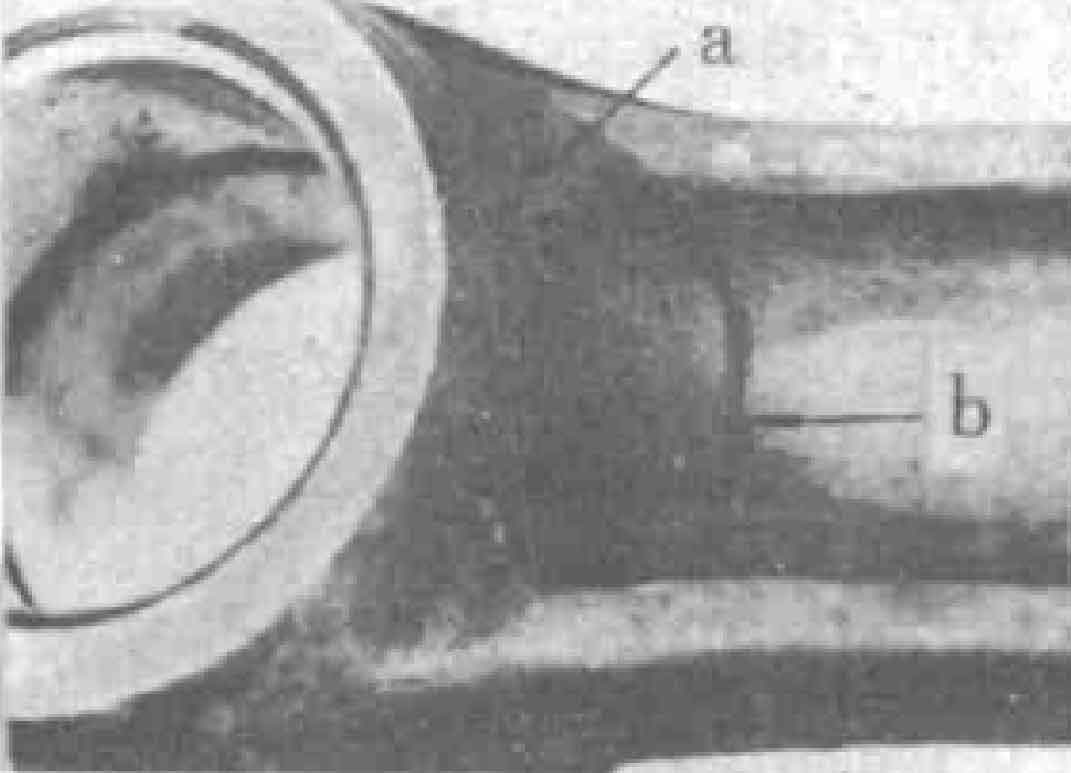
Due to the complex shape of the connecting rod, quenching cracks will also occur directly due to the influence of heating temperature, medium quality, raw material composition segregation and other factors during quenching, tempering and quenching. Quenching crack is characterized by cracking along grain boundary, no decarburization on both sides and oxide inside.
Therefore, the comprehensive effect of the structural stress and thermal stress generated during quenching is an important factor for the formation of quenching cracks. In addition, the micro cracks formed in the surface layer of the material during the forging process have opened the door for the formation of quenching cracks. In the third stage of quenching treatment, the core is cooled to MS point, forming martensite, trying to expand, so that the surface layer is under tensile stress. The surface layer is already hard and brittle martensite at room temperature. Under the action of tensile stress, It is difficult to deform. At this time, it is easy to take the surface microcrack as the stress concentration source to form cracking. The coarser the martensite needle, the easier it is to crack. If the heating temperature is too high, the structure of the steel will be coarse, and cracks may occur during quenching; Improper cooling is also easy to cause cracking. If the quenching is not tempered in time or the tempering is improper, the residual internal stress is still very large, which can also produce cracks, and even burst automatically in serious cases.
Therefore, quenching cracking is the most important form of heat treatment defects. Generally speaking, the superposition of structural stress and thermal stress of materials is the basic internal cause of cracking, and the unreasonable shape or structure of parts is the basic external cause of quenching cracking. Sharp changes in section, asymmetric shape, sharp corners, etc. will cause serious stress concentration in local areas of the material, which will worsen the stress state and increase the stress value. The product will bear the effect of abnormal tensile stress. If the stress value in the stress concentration area exceeds the fracture limit of the material, micro cracks will be formed and rapidly expand, and finally macro cracks will be formed.