1. Core making process of cylinder water jacket
The triethylamine cold core making method is adopted, and the process parameters are shown in the table. Main components of core sand: SiO2 ≥ 92%, silt content ≤ 0.35%, moisture ≤ 0.2%. The number of core sand mesh is 40/100 mesh, in which the concentration of the third sieve is ≥ 75%, the concentration of the fourth sieve is ≥ 85%, AFS=45~52, and the acid consumption value is ≤ 5 mL/50 g.
2. Defect analysis
The profile size of the shot water jacket sand core and the relative position of the middle beam structure were tested, and the results showed that they were qualified. Further cutting inspection was carried out on the castings (number of samples: 10 cylinder blocks of A and B moulds), and it was found that the total length of the water jacket had a fluctuation of 0.5~1.5mm (there was a tendency to become longer), and the deviation of the three water passage gaps between cylinder holes from the theoretical position was 0.3~1.2mm, but the fluctuation direction did not show obvious regularity. On the other hand, the wall thickness of the lower type water jacket is larger on the whole.
Project | Type of core sand | Number of mesh/mesh | Resin dosage (%) | Sand shooting time/s | Curing time/s | Sand shooting pressure/10 ^ 5Pa |
Parameters | Scrubbing sand | 48-55 | 1.5 (two-component 1:1) | 2-3 | Approximately 40 | 2-4 |
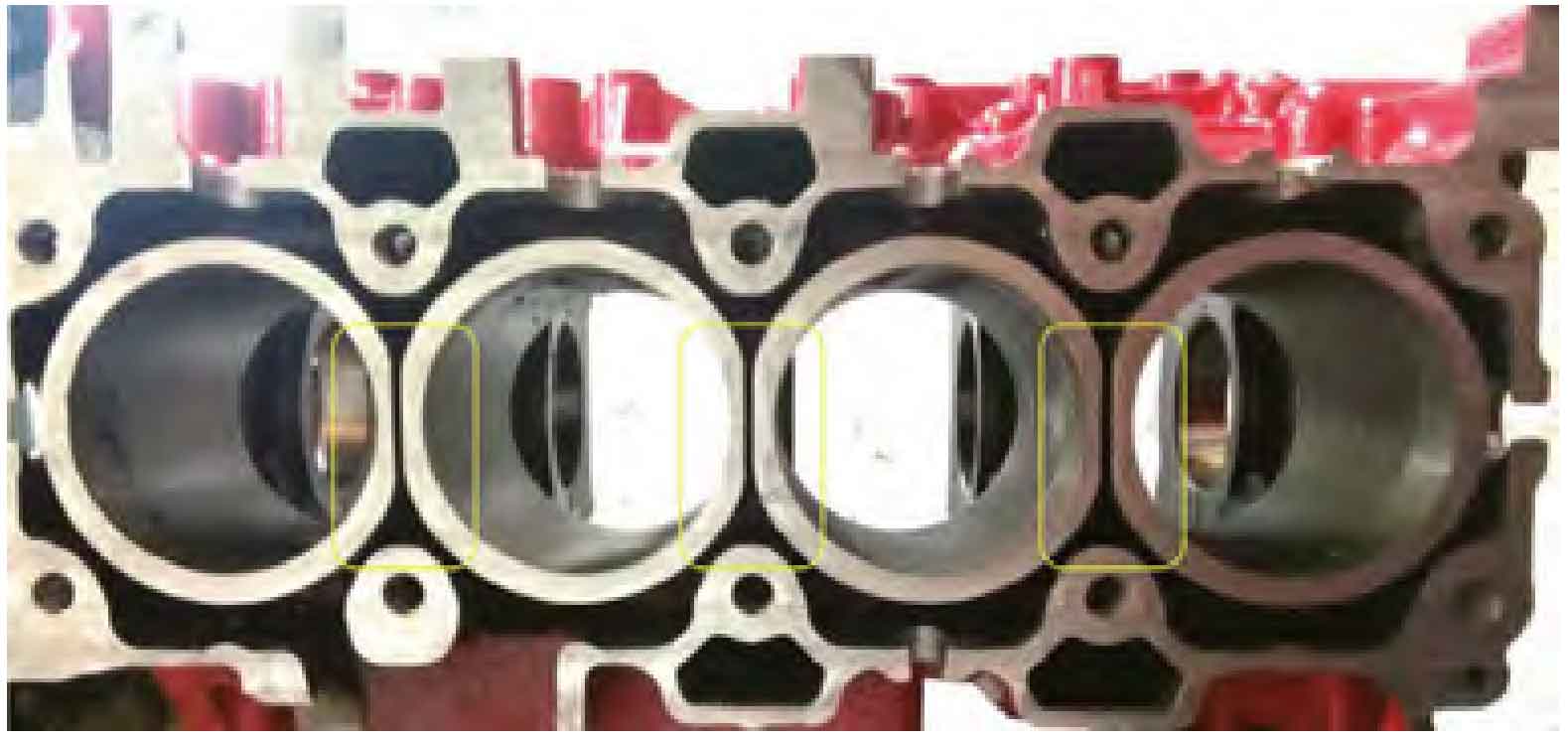
It is concluded that in the process of high temperature pouring, the core of water jacket sand drift obviously under the effect of molten iron buoyancy, resulting in the deformation of the casting. Such defects are concentrated at the middle thin-walled beam as shown in Figure 1. Because the upper surface of the water jacket core is supported by the sand hole and the metal core support, the wall thickness of the upper water jacket is normal; However, the thickness of the middle cross beam is only 3 mm, and its strength is low, so it cannot provide enough support for the lower profile of the water jacket. It bends under the effect of buoyancy, resulting in uneven wall thickness of the cylinder hole. In severe cases, core breaking occurs, as shown in Figure 2.
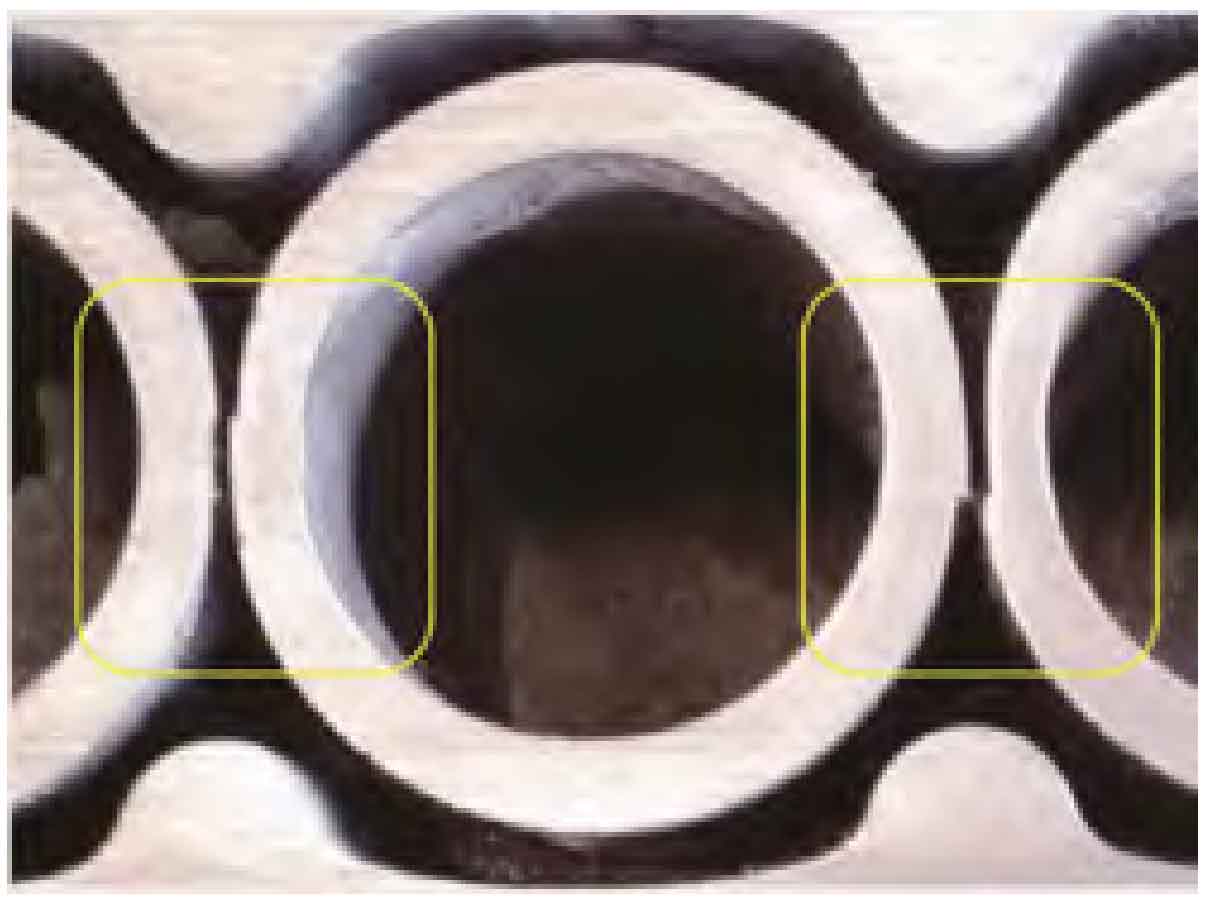
According to the above analysis of sand adhesion mechanism, it can be further confirmed that the defect is mainly mechanical sand adhesion. Mechanical sand sticking is a mechanical mixture of sand and metal adhered to part or the whole surface of a casting. It is formed by metal penetrating into the micropores on the surface of the mold. If the penetration depth is less than the sand grain radius, the casting will not have sand sticking and only make its surface rough. If the penetration radius is greater than the sand grain diameter, mechanical sand sticking will occur. If the penetration depth exceeds 2-3 times the sand grain diameter, it is very difficult to clean.