Cast iron is the most widely used basic material in metal materials and plays an important role in casting alloys. According to statistics, in 2012, China’s casting output reached 41.5 million tons. In the application of casting equipment manufacturing industry, automobiles accounted for 24.8% and agricultural machinery accounted for 4%. At present, gray cast iron is still the main material for the engine block of large trucks and tractors. However, with the intensification of market competition, gray cast iron, as a traditional “large quantity and wide range” metal structure material, is facing serious challenges in material quality, performance and price. Due to the relatively low strength of gray cast iron, it has been strongly competitive by stamping parts, weldments, nodular (vermicular) cast iron, non-ferrous metals and plastics for some time, and the demand shows a downward trend. With the development of light weight and high power of automobile, it is urgent to reduce the requirements of self weight of structural parts and further improve the comprehensive properties of gray cast iron.
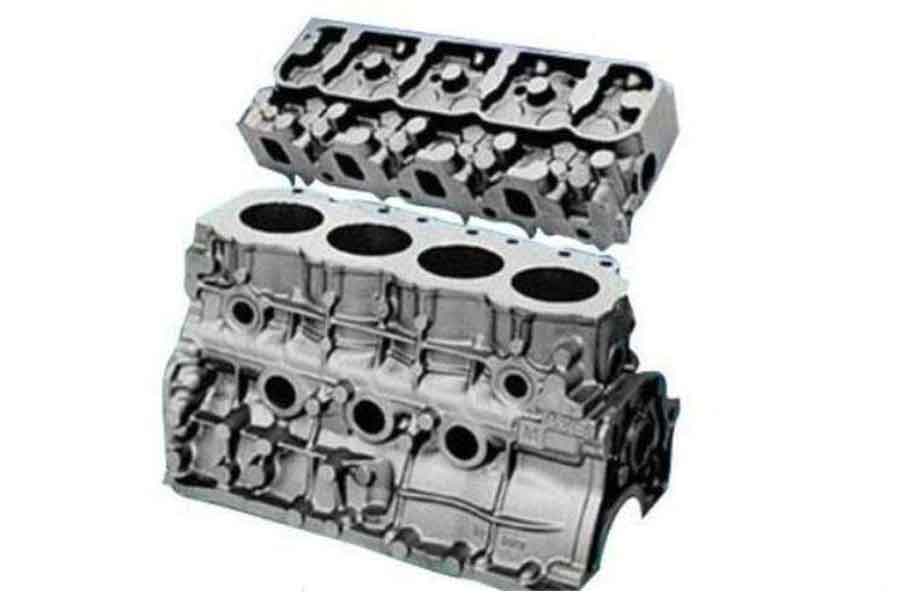
For a long time, in order to improve the strength of gray cast iron, the majority of foreign scientific researchers have carried out a large number of and systematic studies on the solidification process, inoculation and modification treatment of high-strength gray cast iron and the influence of alloy elements on the microstructure and properties of gray cast iron. As early as 1997, AFS established a special thin-walled cast iron group to improve the technology of high-strength castings and thin-walled parts; Japan’s technology of high-strength thin-walled gray cast iron for the 21st century has been supported by the government of 30 million yen. In recent years, China has achieved fruitful results in casting production and technology, but generally speaking, compared with industrial developed countries, there is still a large gap in production cost, casting quality and environmental protection. The engine block castings produced by the casting company subordinate to China YITUO Group Co., Ltd. have exposed many problems in the process of integrating with international standards, such as high production cost, low product quality, and urgent improvement of the core production technology of castings. The increase of engine pressure puts forward higher requirements for material strength and fatigue performance. How to further improve the strength of gray cast iron has become the concern of foundry workers.
At present, the production of high-power diesel engine cylinder block and other high-strength gray cast iron castings at home and abroad is mainly to improve the properties of gray cast iron by adding a certain amount of Cu, Cr, Mo and Ni alloy elements. At present, the cylinder block, cylinder head and some shell castings produced by China Yituo casting company are mostly alloyed with Cu and Cr to meet the strength requirements. The compound addition of Cu and Cr to gray cast iron can give better play to their alloying ability. After adding Cu to gray cast iron containing Cr, it can improve the quality index, improve the graphite morphology, stabilize the pearlescent volume, reduce the chilling tendency and improve the casting properties. Among these alloy elements, the price of Cu is relatively low and the most commonly used. In recent years, the price of Cu has increased significantly, from about 20000 yuan / ton to about 60000 yuan / ton. With the soaring price of copper, the pressure of increasing costs has become a problem for manufacturers