Comparing gray cast iron with other materials used in engineering provides insight into their respective strengths and weaknesses for different applications. Here’s a comparative analysis of gray cast iron against commonly used engineering materials:
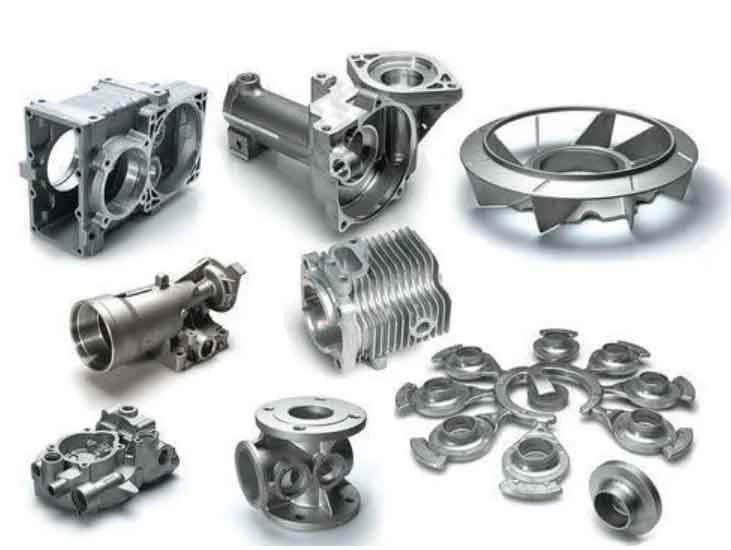
- Gray Cast Iron vs. Ductile Iron: Gray cast iron and ductile iron are both iron-carbon alloys, but the difference lies in their microstructure. Gray cast iron has graphite flakes, while ductile iron has spheroidal graphite nodules, which give it improved ductility and toughness. Ductile iron offers higher tensile strength and impact resistance than gray cast iron, making it suitable for applications requiring higher mechanical properties and better resistance to shock loading.
- Gray Cast Iron vs. Steel: Steel is an alloy of iron and carbon with other alloying elements, such as manganese, chromium, and nickel. Compared to gray cast iron, steel generally has higher tensile strength, toughness, and fatigue resistance. Steel is favored when high strength, ductility, and impact resistance are essential, such as in structural components and machinery subjected to dynamic loads.
- Gray Cast Iron vs. Aluminum Alloys: Aluminum alloys are known for their lightweight and excellent corrosion resistance. In contrast, gray cast iron is much denser and less corrosion-resistant. Aluminum alloys find use in applications requiring a combination of strength, lightness, and resistance to environmental exposure, while gray cast iron is chosen for its cost-effectiveness and wear resistance.
- Gray Cast Iron vs. Nodular Cast Iron (Nodular Iron): Nodular cast iron, also known as nodular iron or ductile iron, is a type of cast iron with spheroidal graphite nodules. Nodular iron combines the castability of gray iron with improved mechanical properties and ductility. Compared to gray cast iron, nodular iron offers higher tensile strength, toughness, and elongation, making it suitable for applications where greater resilience and higher mechanical performance are required.
- Gray Cast Iron vs. Stainless Steel: Stainless steel, an alloy of iron with chromium and sometimes other elements, offers excellent corrosion resistance and high strength. Stainless steel is often chosen for applications where resistance to rust and corrosion is crucial, such as marine equipment, food processing machinery, and medical devices. Gray cast iron is less resistant to corrosion and is more commonly used in applications where wear resistance and low cost are prioritized.
- Gray Cast Iron vs. Titanium Alloys: Titanium alloys are known for their excellent strength-to-weight ratio, high corrosion resistance, and biocompatibility. These alloys find applications in aerospace, medical implants, and other high-performance industries. Gray cast iron’s strength lies in its wear resistance and low cost, making it suitable for applications where weight considerations are less critical.
The choice between gray cast iron and other materials depends on the specific engineering requirements, including mechanical properties, corrosion resistance, weight considerations, cost, and manufacturing feasibility. Each material offers unique advantages, and engineers carefully evaluate these factors to select the most suitable material for a given application.