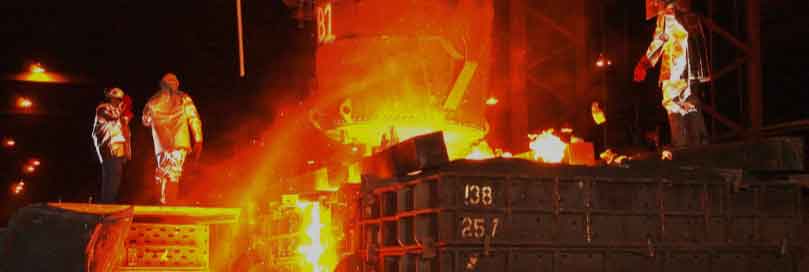
Grey iron castings and ductile iron castings are two different types of cast iron with distinct characteristics and applications. Here’s a comparative analysis of grey iron castings and ductile iron castings:
- Microstructure and Mechanical Properties:
- Grey Iron Castings: Grey iron has a flake graphite microstructure, which gives it its characteristic gray appearance. This microstructure provides good thermal conductivity and damping properties. However, it makes grey iron relatively brittle, resulting in lower tensile strength and impact resistance compared to ductile iron.
- Ductile Iron Castings: Ductile iron, also known as nodular cast iron, has a nodular graphite microstructure. The nodules of graphite in the matrix give ductile iron its improved mechanical properties. Ductile iron exhibits higher tensile strength, elongation, and impact resistance compared to grey iron, making it more ductile and tougher.
- Strength and Durability:
- Grey Iron Castings: Grey iron offers good compressive strength, making it suitable for applications where compressive loads are predominant. It has excellent wear resistance, making it ideal for components subjected to abrasive conditions.
- Ductile Iron Castings: Ductile iron provides higher tensile strength and yield strength compared to grey iron, making it suitable for applications that require higher mechanical performance. It offers better resistance to deformation and is less susceptible to cracking under load.
- Machinability:
- Grey Iron Castings: Grey iron is known for its excellent machinability. Its graphite flakes act as built-in lubricants, reducing friction and heat during machining operations. This results in improved tool life and enhanced productivity.
- Ductile Iron Castings: Ductile iron has lower machinability compared to grey iron due to its nodular graphite structure. The presence of the nodules can cause tool wear and vibration during machining, requiring appropriate cutting parameters and tooling for efficient machining.
- Application Range:
- Grey Iron Castings: Grey iron is commonly used in applications where good thermal conductivity, damping properties, and wear resistance are required. It finds extensive use in automotive components, such as engine blocks, brake drums, and cylinder heads, as well as in pipes, pump housings, and machine tool structures.
- Ductile Iron Castings: Ductile iron is preferred in applications that demand higher strength, toughness, and impact resistance. It is commonly used in heavy machinery, automotive components, agricultural equipment, and construction applications. Ductile iron is also suitable for components subjected to dynamic loads and high-pressure environments.
- Cost Considerations:
- Grey Iron Castings: Grey iron castings are generally less expensive compared to ductile iron castings. The production process for grey iron is simpler and requires fewer alloying elements, resulting in lower production costs.
- Ductile Iron Castings: Ductile iron castings involve additional steps and the use of alloying elements, making them relatively more expensive than grey iron castings.
Grey iron castings offer good wear resistance and machinability, while ductile iron castings provide superior strength, toughness, and impact resistance. The choice between the two depends on the specific requirements of the application, considering factors such as load conditions, mechanical properties, machinability, and cost considerations.