Choosing the right material for your project depends on several factors, including the specific application, required properties, and budget constraints. Here’s a comparison of gray iron castings with other common materials to help you make an informed decision:
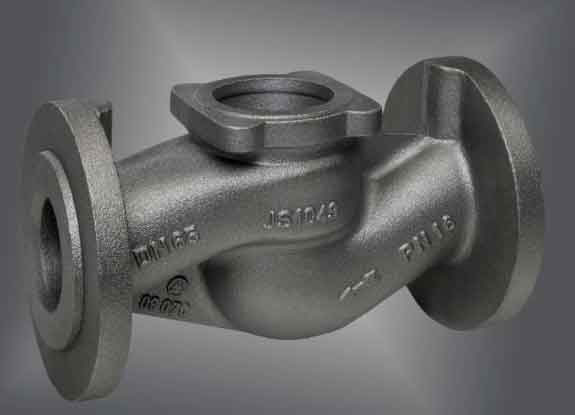
- Gray Iron vs. Ductile Iron: Both gray iron and ductile iron are cast iron alloys, but they have different microstructures and mechanical properties. Gray iron has graphite flakes in its microstructure, providing good machinability and damping capacity but lower tensile strength and ductility. On the other hand, ductile iron has nodular graphite, resulting in higher tensile strength, ductility, and impact resistance. Ductile iron is often chosen when higher mechanical properties are required, while gray iron is preferred for applications where good machinability and damping properties are essential.
- Gray Iron vs. Steel: Steel is a ferrous alloy with higher carbon content than cast iron. Compared to gray iron, steel generally has higher tensile strength, hardness, and impact resistance. However, gray iron has better damping capacity, which makes it suitable for applications where vibration damping is critical. Steel may be a better choice for applications requiring high strength and toughness, while gray iron is favored for applications where vibration and noise reduction are important.
- Gray Iron vs. Aluminum Alloys: Aluminum alloys are non-ferrous materials that offer lower density, good corrosion resistance, and excellent thermal conductivity compared to gray iron. Aluminum castings are often preferred for lightweight applications, such as aerospace and automotive components. Gray iron, on the other hand, provides better wear resistance, making it suitable for heavy-duty applications.
- Gray Iron vs. Bronze: Bronze is a copper-based alloy known for its excellent corrosion resistance and low friction properties. It is often chosen for applications where lubrication may be challenging. Gray iron is typically preferred when higher strength, wear resistance, and cost-effectiveness are required.
- Gray Iron vs. Cast Steel: Cast steel shares similarities with both gray iron and steel. It provides better tensile strength and ductility compared to gray iron but may not have the same damping properties. Cast steel is often chosen for applications requiring a balance between strength and toughness.
The choice between gray iron castings and other materials depends on the specific requirements of your project. Gray iron is a versatile material with excellent machinability, damping capacity, and wear resistance, making it suitable for various industrial applications. However, for projects demanding higher tensile strength, ductility, or other specific properties, other materials like ductile iron, steel, aluminum alloys, bronze, or cast steel may be more appropriate. It’s essential to consider the unique characteristics of each material and how they align with your project’s needs to make the right choice.