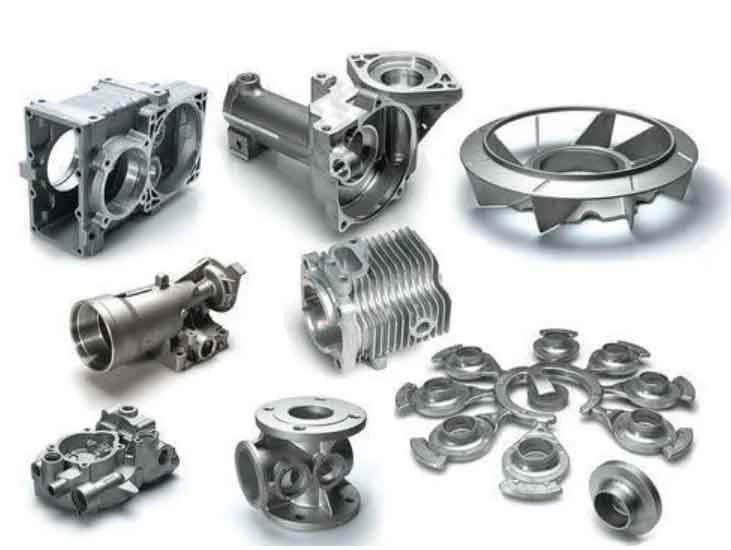
Ensuring quality in grey cast iron foundries is crucial to producing components that meet industry standards and customer expectations. Quality control and process optimization play a significant role in achieving consistent and reliable results. Here are some key steps and strategies that grey cast iron foundries employ to ensure quality in their production processes:
- Quality Management Systems (QMS):
- Implementing a robust quality management system is essential to establish standard operating procedures and quality control protocols. QMS frameworks such as ISO 9001 provide a systematic approach to quality assurance.
- Process Control and Monitoring:
- Regular monitoring and control of the casting process parameters, such as pouring temperature, mold temperature, and cooling rates, help maintain consistency and minimize defects.
- Raw Material Inspection:
- Thoroughly inspecting incoming raw materials, including iron alloys, additives, and inoculants, ensures that only high-quality materials are used in the casting process.
- Mold Design and Preparation:
- Well-designed molds with proper gating and risering systems help ensure uniform filling and solidification, reducing the risk of defects.
- In-Process Inspection and Testing:
- Performing in-process inspections, such as visual inspections, dimensional checks, and ultrasonic testing, helps identify any issues early in the production process.
- Non-Destructive Testing (NDT):
- Implementing NDT techniques, such as ultrasonic testing, radiography, or magnetic particle testing, allows for the detection of internal defects without damaging the components.
- Metallurgical Analysis:
- Conducting metallurgical analysis, including microstructure examination and chemical composition testing, provides insights into the material’s properties and helps identify any deviations from specifications.
- Heat Treatment and Finishing:
- Applying proper heat treatment and finishing processes helps achieve the desired mechanical properties and surface characteristics.
- Employee Training and Skill Development:
- Investing in employee training and skill development ensures that the workforce is equipped with the necessary knowledge and expertise to maintain quality standards.
- Continuous Improvement and Lean Manufacturing:
- Adopting continuous improvement practices and lean manufacturing principles helps streamline processes and minimize waste, enhancing overall efficiency and quality.
- Traceability and Documentation:
- Maintaining accurate and detailed records of each casting’s production history enables traceability and facilitates root cause analysis in case of any quality issues.
- Customer Feedback and Satisfaction:
- Regularly seeking customer feedback and ensuring customer satisfaction are essential for understanding the performance of the castings in real-world applications.
By incorporating these strategies and best practices, grey cast iron foundries can establish a culture of quality and reliability, resulting in consistently high-quality castings that meet the stringent requirements of various industries.