Grey cast iron undergoes a transformation from molten metal in the foundry to functional parts in various industries. Let’s explore the process of producing grey cast iron components:
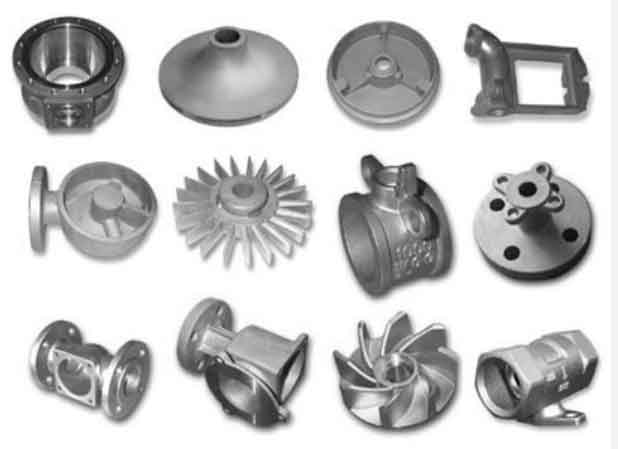
1. Melting and Preparation:
The production of grey cast iron begins with melting scrap iron, along with the addition of alloying elements such as carbon, silicon, and manganese, in a cupola furnace or an electric induction furnace. The mixture is heated to a molten state, allowing impurities to be removed through the use of fluxes or additives. The molten iron is then transferred to a ladle for further processing.
2. Casting:
Once the molten iron is prepared, the casting process begins. The molten iron is poured into a mold made from sand or other refractory materials. In the case of grey cast iron, the mold is typically made from green sand, a mixture of silica sand, clay, and water. The mold is carefully prepared by compacting the sand mixture around a pattern that defines the shape of the desired component.
3. Solidification and Cooling:
After pouring the molten iron into the mold, it starts to solidify and cool. During this phase, the graphite within the iron forms as flakes, giving grey cast iron its characteristic appearance. The solidification process is carefully controlled to ensure proper formation of the graphite structure and minimize the formation of other undesirable phases.
4. Shakeout and Cleaning:
Once the cast iron has sufficiently cooled and solidified, the mold is removed through a process known as shakeout. The casting is separated from the mold, and any excess sand is removed. The castings may undergo shot blasting or other cleaning processes to further remove any residual sand or other impurities.
5. Finishing and Machining:
After cleaning, the grey cast iron components undergo finishing operations to achieve the desired surface finish and dimensional accuracy. This may involve grinding, milling, turning, or other machining processes. The casting may also undergo heat treatment processes such as annealing or stress relieving to enhance its properties and remove any internal stresses.
6. Quality Control and Inspection:
Grey cast iron components undergo rigorous quality control measures to ensure they meet the specified standards and requirements. This may involve dimensional inspection, visual inspection, non-destructive testing (NDT), and other techniques to detect any defects or inconsistencies in the casting.
7. Application-Specific Treatment:
Depending on the intended application, grey cast iron components may undergo additional treatments or coatings to enhance their performance and durability. This could include surface treatments like painting or coating for corrosion resistance, or heat treatments to further improve the material’s properties.
8. Integration and Assembly:
Finally, the grey cast iron components are integrated into their respective applications. They may be assembled with other parts or integrated into larger systems or machinery. In automotive applications, for example, grey cast iron engine blocks are assembled with pistons, cylinder heads, and other components to form a complete engine.
The process of transforming grey cast iron from molten metal to functional parts involves a combination of foundry techniques, careful solidification, finishing operations, quality control, and application-specific treatments. This process ensures that the resulting grey cast iron components possess the desired strength, durability, and performance characteristics required for their intended applications.