Grey cast iron has indeed been a timeless classic in the world of materials due to its exceptional properties, cost-effectiveness, and wide range of applications. With the advent of advanced materials and technologies, grey cast iron continues to evolve and adapt to meet the demands of modern industries. Some of the ways in which grey cast iron is evolving with technology include:
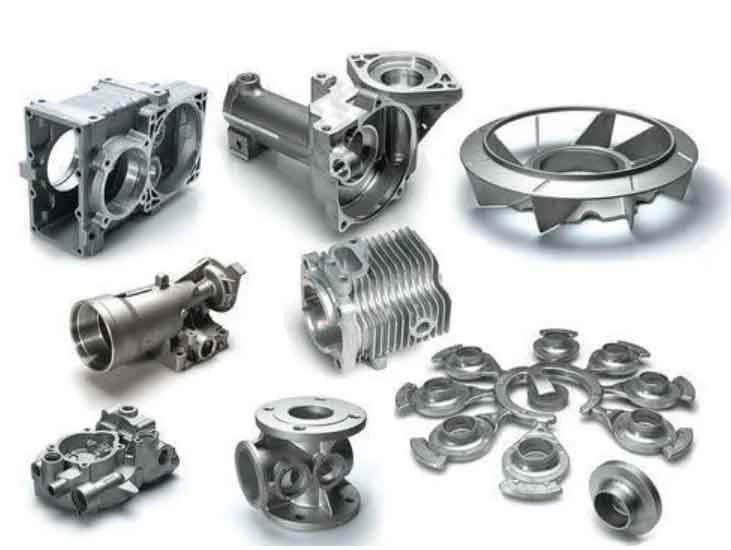
- Material Enhancements: Researchers are continuously exploring ways to enhance the properties of grey cast iron. Through the addition of alloying elements and precise control of the casting process, grey cast iron can achieve improved strength, wear resistance, and thermal conductivity while maintaining its favorable machinability.
- Simulation and Modeling: Advanced computer simulation and modeling techniques enable engineers to optimize casting designs and predict the behavior of grey cast iron components during the casting process. This allows for the creation of complex geometries and optimized structures, leading to better performance in specific applications.
- Additive Manufacturing Integration: Additive manufacturing (3D printing) is being combined with traditional casting techniques to create complex sand molds, patterns, and cores for grey cast iron components. This integration allows for more intricate designs and rapid prototyping, reducing lead times and material waste.
- Composite Materials: Hybrid materials, such as combining grey cast iron with other materials like ceramics or polymers, are being explored to create components with tailored properties for specific applications. These composite materials offer a unique combination of characteristics not achievable with individual materials.
- Lightweighting Solutions: With the increasing emphasis on lightweighting to improve energy efficiency and reduce emissions, grey cast iron is being used in innovative ways to provide lightweight solutions while maintaining its strength and durability.
- Digital Twins and IoT Integration: Digital twin technology allows manufacturers to create virtual representations of grey cast iron components and monitor their real-time performance during operation. This data-driven approach enables predictive maintenance, optimized performance, and better decision-making.
- Sustainable Practices: The casting industry is embracing sustainable practices, and grey cast iron foundries are adopting greener processes, such as energy-efficient furnaces, recycling of casting sand, and reducing emissions, to minimize the environmental impact.
- Quality Control and Inspection: Advanced non-destructive testing (NDT) methods, like X-ray imaging and ultrasonic testing, are employed to ensure the quality and integrity of grey cast iron components, identifying defects and flaws with precision.
- Automation and Robotics: Automation and robotics are being implemented in grey cast iron foundries to increase efficiency, reduce labor costs, and ensure consistent quality in the casting process.
- Industry 4.0 Integration: Grey cast iron foundries are adopting Industry 4.0 technologies to create smart and interconnected production environments. Real-time data analytics and connectivity allow for agile and flexible manufacturing processes.
As a result of these advancements, grey cast iron remains a versatile and essential material in various industries, including automotive, construction, machinery, and infrastructure. Its timeless appeal, combined with evolving technologies, ensures that grey cast iron will continue to play a significant role in modern engineering applications.