Chapter 1:Survey results from the American Foundry Association: Castings manufacturers are preparing to invest in 2024
According to the latest quarterly outlook survey of castings manufacturers conducted by the American Foundry Association, cautious optimism is the view of North American castings manufacturers on their business prospects.
More than 55% of respondents stated that they are very optimistic or to some extent optimistic about the business prospects of castings manufacturers in the next 12 months, while 21% of respondents hold a negative view. Respondents from castings manufacturers are particularly optimistic about the sales prospects of castings in the defense, oil and gas, and valve industries.
Most castings manufacturers are preparing for major investments, with 39% planning to allocate $1 million or more for capital projects in the next year, and another 25% expecting expenditures between $500000 and $1 million.
This survey identified key areas of investment, particularly grinding equipment at 41%, robots at 35%, machining machines at 35%, shaping equipment at 30%, lifting equipment at 28%, conveyors at 26%, environmental control at 26%, laboratory equipment at 26%, shot blasting technology at 22%, inspection/testing equipment at 22%, smelting equipment at 22%, core making machines at 20%, and air compressors at 19%.
Despite the optimistic outlook, castings manufacturers still face many challenges, with labor shortages being the first to hit, followed by regulatory difficulties and labor training issues. “The quarterly outlook survey of castings manufacturers emphasizes the crucial role of castings manufacturers in our manufacturing foundation and economy,” said Doug Kokull, CEO of the American Foundry Association. “These findings indicate that North American castings manufacturers are preparing to invest heavily in their equipment in 2024, promoting innovation and creating employment opportunities.”
The 2024 American Casting Manufacturing Conference is scheduled to be held from April 23rd to 25th in Milwaukee, Wisconsin, inviting suppliers from the metal casting industry and North American castings manufacturers to participate in the exhibition. This event provides a platform for thousands of castings manufacturers and industry professionals to showcase their products and services.
Chapter 2:Waupaca Castings Manufacturers in the United States Wins Sustainable Development Award
WAUPACA, Wisconsin – The WAUPACA castings manufacturers has once again won environmental awards from the National Trade Organization and customers. The castings manufacturers has been awarded the American Foundry Society (AFS) 2023 Green Casting Award for its sustained commitment to sustainable production processes and energy conservation. The Wopaca castings manufacturers was commended for preparing a sustainable development report for the enterprise. Wopaca Castings Manufacturers is the first independent American cast iron supplier to establish and communicate sustainable development goals and issue corporate sustainability reports to its stakeholders.
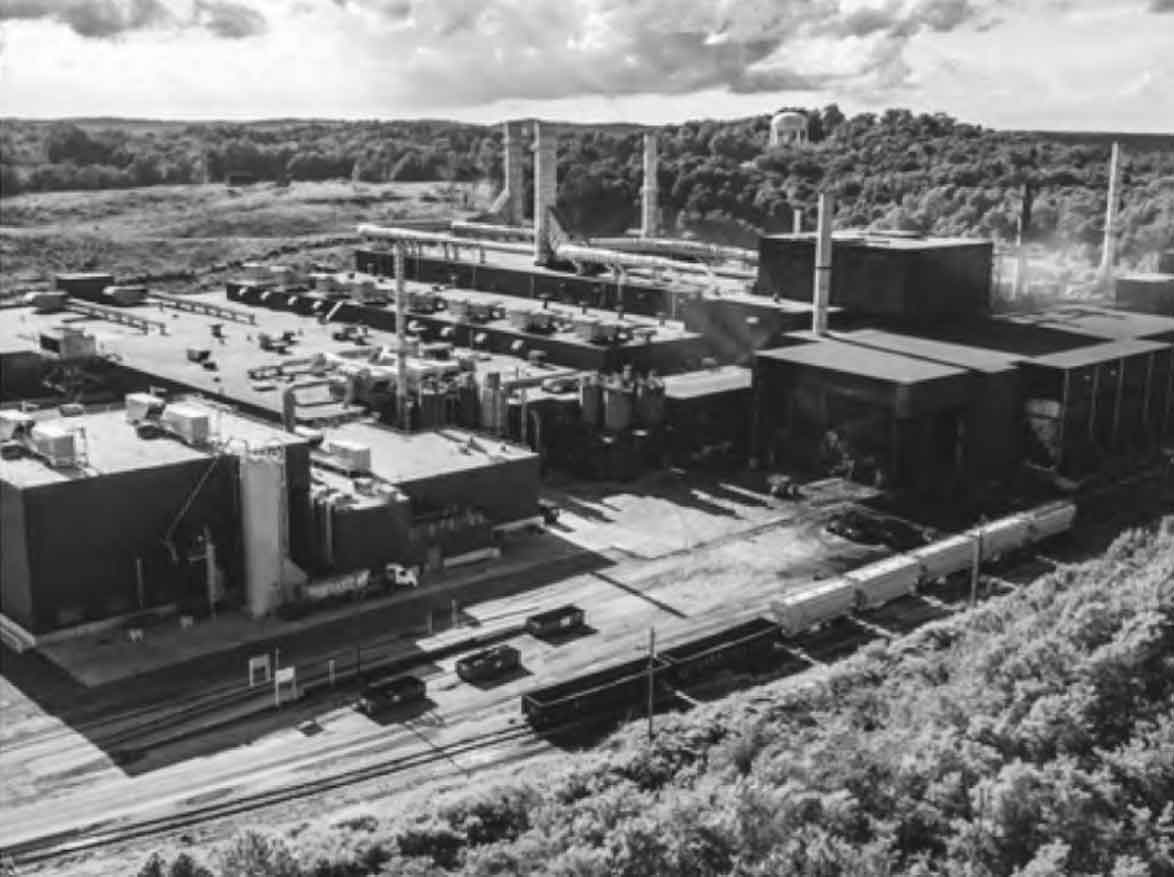
Since 2014, Waupaca castings manufacturers have been following the Global Reporting Initiative (GRI) standards to measure best practices for sustainable development and hold the company accountable for their set environmental goals. This is the second consecutive year that the Wopaca castings manufacturers has received the AFS Sustainable Development Award.
The Wopaca castings manufacturers has established a cross functional team to collect environmental, social, and governance reports to compile organizational goals and indicators, with the goal of becoming a future green castings manufacturers. This report conveys the company’s environmental goals, including reducing energy use, reducing emissions, and other sustainability activities beyond regulatory compliance.
“Now, more than ever before, our customers hope that their supply chain will help achieve organizational sustainability goals,” said Mike Nickley, President, Chief Operating Officer, and CEO of Wopaca Castings Manufacturers. “Our green initiatives help our clients achieve their personal goals, and partnerships like this provide support for all stakeholders’ decarbonization goals.”
85% of the iron produced by the Wopaca castings manufacturers is made from recycled materials, with an annual recovery of 450000 tons of casting by-products. Recycling and environmental commitments have been effective since the 1980s, but were extended to the entire enterprise’s sustainable development plan in 2014.
“We hope to set a benchmark for the most advanced technology in the casting industry,” said Brian Teresh, Sustainable Development Manager at Wopaca Castings Manufacturers. “These are all selective actions we take that go beyond environmental requirements, and energy efficiency is one of the biggest tools we use to influence overall process improvement.”
In order to achieve sustainable development goals, Wopaca castings manufacturers have taken many specific measures in the past 20 years, including:
In 2001, the Wopaca castings manufacturers met the ISO14001 standard and established a framework for establishing an effective environmental management system.
In 2009, Wopaca castings manufacturers joined the Ministry of Energy’s “Better Castings Manufacturers Project” and promised to reduce energy intensity by 25% within ten years.
In 2013, the company established a sustainable development benchmark.
In 2014, the Waupaca castings manufacturers established a greenhouse gas accounting (GHG) method to measure its greenhouse gas emissions and hired a full-time energy manager.
In 2014, the Wopaca castings manufacturers established a multidisciplinary sustainability team and a substantive evaluation testing method to better understand sustainability issues and prioritize them.
In 2014, the Wopaca castings manufacturers completed a strategic energy project and officially established sustainable development goals, resources, and Key Performance Indicators (KPIs).
In 2014, the Wopaca castings manufacturers released its first sustainability report.
In 2015, the Wopaca castings manufacturers submitted its first Carbon Disclosure Report (CDP), which disclosed the company’s impact on the environment and actions taken to reduce its carbon footprint.
In 2016, the Wopaca castings manufacturers obtained ISO 50001 certification at its No.1 factory, ensuring that the organization has an energy management system, reducing energy consumption, environmental impact, and improving profitability.
In 2016, Wopaca castings manufacturers joined the Department of Energy’s “Accelerating 2030 Energy Productivity” project, which aims to double the energy productivity in the United States from 2010 levels by 2030.
In 2021, the Wopaca castings manufacturers was honored by the Ministry of Energy’s “Better Castings Manufacturers” project for its project to eliminate air humidity around the factory’s cupola.
In 2021, the Wopaca castings manufacturers was recognized by the Ministry of Energy’s “Better Castings Manufacturers” project for improving the energy efficiency of air compressor systems.
In 2022, the Wopaca castings manufacturers joined the Department of Energy’s “Better Climate Challenge” to reduce greenhouse gas emissions by 25% by 2030.
In 2022, AFS awarded the Wopaca Castings Manufacturers the Green Casting Award in recognition of their installation of dehumidification systems at the Teal Castings Manufacturers in Indiana, which significantly reduced energy consumption.
The Wopaca castings manufacturers was commended by two suppliers (Bosch Rexroth and Kawasaki). The Wopaca castings manufacturers have once again won recognition from two suppliers (Bosch Rexroth and Kawasaki) for their sustainable development efforts. Bosch Rexroth has listed the Wopaca castings manufacturers as one of the three suppliers worldwide to receive the highest performance award, outstanding corporate social responsibility, and sustainable development award. Its sustainability disclosure and environmental performance have been rated as one of the most advanced global suppliers in the field of sustainability. The Wopaca castings manufacturers have also been awarded the Excellence Award for Technological Progress and Customer Cooperation. No other supplier has won all three awards.
The metal casting machine also received the 2022 Environmental Award from Kawasaki Automobile Manufacturing Company. This is the fifth time since 2011 that the Wopaca castings manufacturers have received this award. This award is based on the improvement of the air compressor system by the No.1 castings manufacturers, the dehumidification system savings by the No.5 castings manufacturers, and the installation of intelligent ventilation control devices by the No.2 and No.3 castings manufacturers, which have improved the operational energy efficiency of each castings manufacturers.
Chapter 3:UK castings manufacturers announce plans for a new £ 17 million casting production line
The British castings manufacturers have announced plans to build a new casting production line in Derbyshire to meet the rapidly growing demand. This new £ 17 million production line from William Lee, a castings manufacturers based in Dronfield, UK, will be funded by internal resources, with a total castings manufacturers capacity of 12000 tons. This new castings manufacturers are expected to be put into use in the next two years, hoping that this additional casting will enable the castings manufacturers to meet its demand for heavy-duty truck components, fully utilize new market areas such as truck electrification and wind energy, and seize further opportunities in the United States.
At present, William Lee’s existing castings manufacturers are unable to meet the current and expected needs and have to outsource some production to other castings manufacturers in the short term. William Lee was acquired by a castings manufacturers in 1991 and produces parts for almost all truck castings manufacturers, including Scania, Volvo, and Daimler. The company currently has 400 employees, producing over 25000 castings per day and selling them worldwide.
Chapter 4:Heidelberg Castings Manufacturers Lacewitz’s New Casting Line Starts Production
After 14 months of expansion, the casting line of Hydro Aluminum, the castings manufacturers based in Rackwitz, Germany, was put into operation on September 14, 2023. The new line can cast high-quality small diameter ingots, which can be directly forged into automotive parts using the HyFoyge process without the need for homogenization heat treatment and extrusion. The castings manufacturer’s casting line has a production capacity of 95 kt/a and employs 20 workers, resulting in a factory workforce of 90 people.
Chapter 5:Wisconsin aluminum castings manufacturers to expand factory
According to foreign media reports, the Wisconsin aluminum castings manufacturers plans to expand its manufacturing plant by approximately 4700 m ^ 2 and renovate approximately 1100 m ^ 2 of office space.
Cinnaire is a company that represents the US government in providing investments and loans to developers and non-profit organizations. The company is providing $11 million in new market tax credits for the project.
The Wisconsin aluminum castings manufacturers project will be conducted in two stages. The newly built industrial section will be completed in March 2024, while the office renovation will be completed in October 2024.
Chapter 6:Ford Metrology Box Castings Manufacturers to Build New Foundry
The Ford Meter Box Co. Inc., located in Wabash, Indiana, is a member of the American Foundry Association. The castings manufacturers will expand its casting business, undergo modernization reforms, and increase downstream production capacity.
This castings manufacturers with a 125 year history produces tap water components for both private and public infrastructure markets. This casting manufacturer’s production department includes casting, machining, assembly, warehousing, and supports professional trading companies around the world. Ford Metrology Company plans to build a state-of-the-art non-ferrous metal foundry (covering an area of 300000 square meters) on a 90 acre plot of land in the industrial park northeast of Wabash, and is currently awaiting local approval.
Steve Ford, President of Castings Manufacturers, stated that this expansion will be the largest in the history of the castings manufacturers. This new factory will complement the existing manufacturing factory of the castings manufacturers on Manchester Avenue. Some workshops of the castings manufacturers will continue to produce, and the use of these workshops will be readjusted to make better use of space. Construction is expected to start in late summer or early autumn. GK Systems, a member of the American Foundry Association, has been appointed as the main design company. GK Systems, as a design, construction, planning, and construction company, castings manufacturers will strive to ensure the highest standards while providing high-quality products.
This independent castings manufacturers is expected to promote a significant increase in brass product production while leaving room for future production lines. The increase in production capacity of the entire casting manufacturer’s equipment will require additional staff; However, the number of recruits will ultimately depend on the level of business. The castings manufacturers is currently recruiting engineering, maintenance, and sales talents to support its growing core business and the recent personnel demand for water treatment plants.
The years of modernization efforts by the castings manufacturers also mean that Wobash’s two factories are investing $250 million to $300 million in technology, capabilities, flexibility, safety, automation, and training. The project aims to enhance the company’s long-term flexibility while addressing the aging water infrastructure in the United States and the demand for tap water from single and multi household housing construction.
Chapter 7:SinterCast, a castings manufacturers, has set a new high in production of compacted graphite cast iron
SinterCast, a castings manufacturers, has seen its production of ductile iron increase for nine consecutive quarters, with an annual output of 205000 tons in June. According to the latest quarterly report of the castings manufacturers, the lightweight vermicular cast iron produced by the castings manufacturers using Hint Caster technology in June set a monthly record, equivalent to the castings manufacturer’s annual production of 4.1 million engines. Equivalent to the castings manufacturers producing 3.9 million engines in May and 3.1 million engines in April. The castings manufacturers achieved an annualized production of 3.7 million engines in the second quarter, setting a new quarterly record for the production of compacted graphite cast iron by Hint Caster castings manufacturers. The castings manufacturers achieved year-on-year growth in series production for nine consecutive quarters.
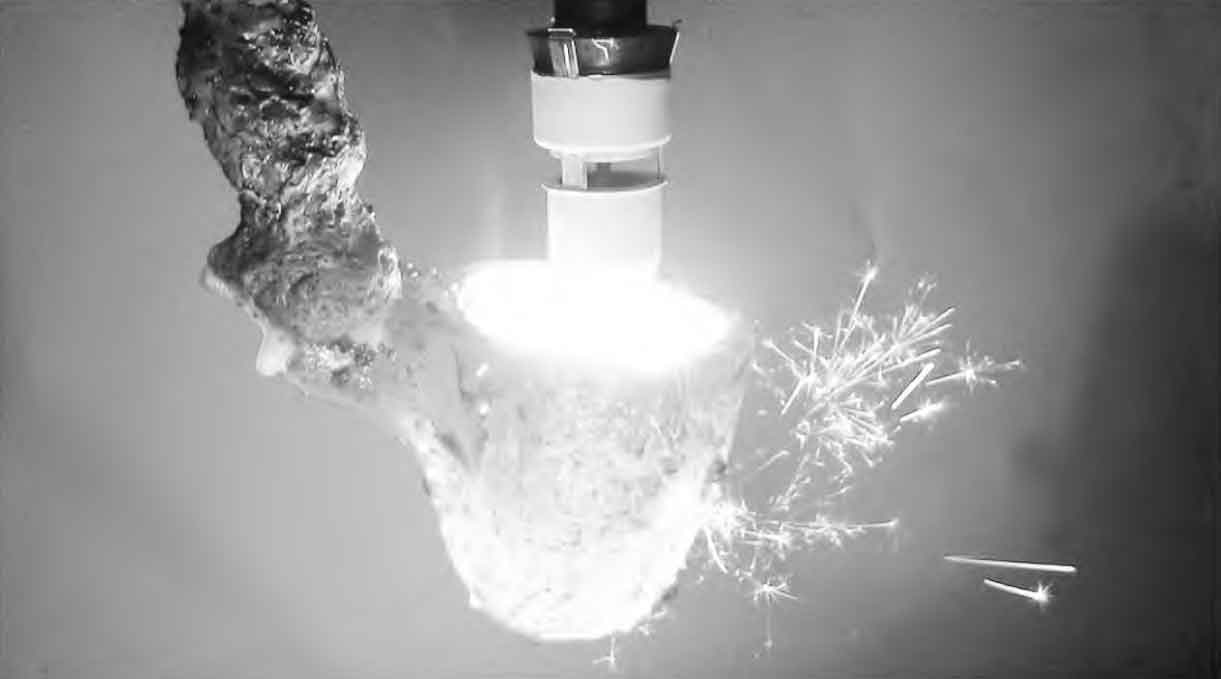
The headquarters of SinterCast Castings Manufacturers is located in Stockholm, and it is a castings manufacturers and patent licensor that uses the most widely used process control technology for vermicular cast iron production. The equivalent of each engine used to record production is equivalent to 50 kg of ductile iron – similar to the weight of a typical passenger car cylinder block. Therefore, the equivalent quantity of 4.1 million engines produced by castings manufacturers in June is equivalent to an annual production of 205000 tons; It is estimated that the actual production of vermicular graphite cast iron produced by the castings manufacturers using Hint Caster process control technology last month was 17083.3 tons.
Starting from the first series production in 1999, Hint Caster Casting Manufacturing took 16 years to reach the milestone of 2 million equivalent engines in 2015. Now, the production of Hint Caster castings has doubled in half the time, reaching 4 million equivalent engines. With the completion of 4 million units of equivalent, Hint Caster castings manufacturers is now turning its attention to 5 million units of equivalent.
SinterCast also provides its licensed castings manufacturers with specialized sampling cups used in the production process of vermicular graphite cast iron. According to the report, in the second quarter of 2023, the shipment volume of castings manufacturers sample cups increased to 49500, a 50% increase from the shipment volume in the first quarter (33100).
According to a report from the SinterCast castings manufacturers, the growth in sample cup shipments in the second quarter also indicates that with the normalization of the global supply chain, customers have basically lifted their restricted orders and are working hard to re-establish minimum inventory levels.
Vermicular cast iron is a lightweight iron-based material with higher tensile strength, stiffness, and fatigue strength than gray cast iron or aluminum alloy. The mass production of ductile iron by castings manufacturers mainly involves diesel and gas engine manufacturers, who seek to reduce weight, noise, and emissions for their engine designs.
Chapter 8:European casting manufacturer sentiment in June 2023
The sentiment index of European casting manufacturers is facing its fourth consecutive decline. The sentiment index of European casting manufacturers in June was 98.6 points, 2.1 points lower than May. Therefore, the sentiment index of European casting manufacturers has fallen below the initial value of 100.0 points in 2015.
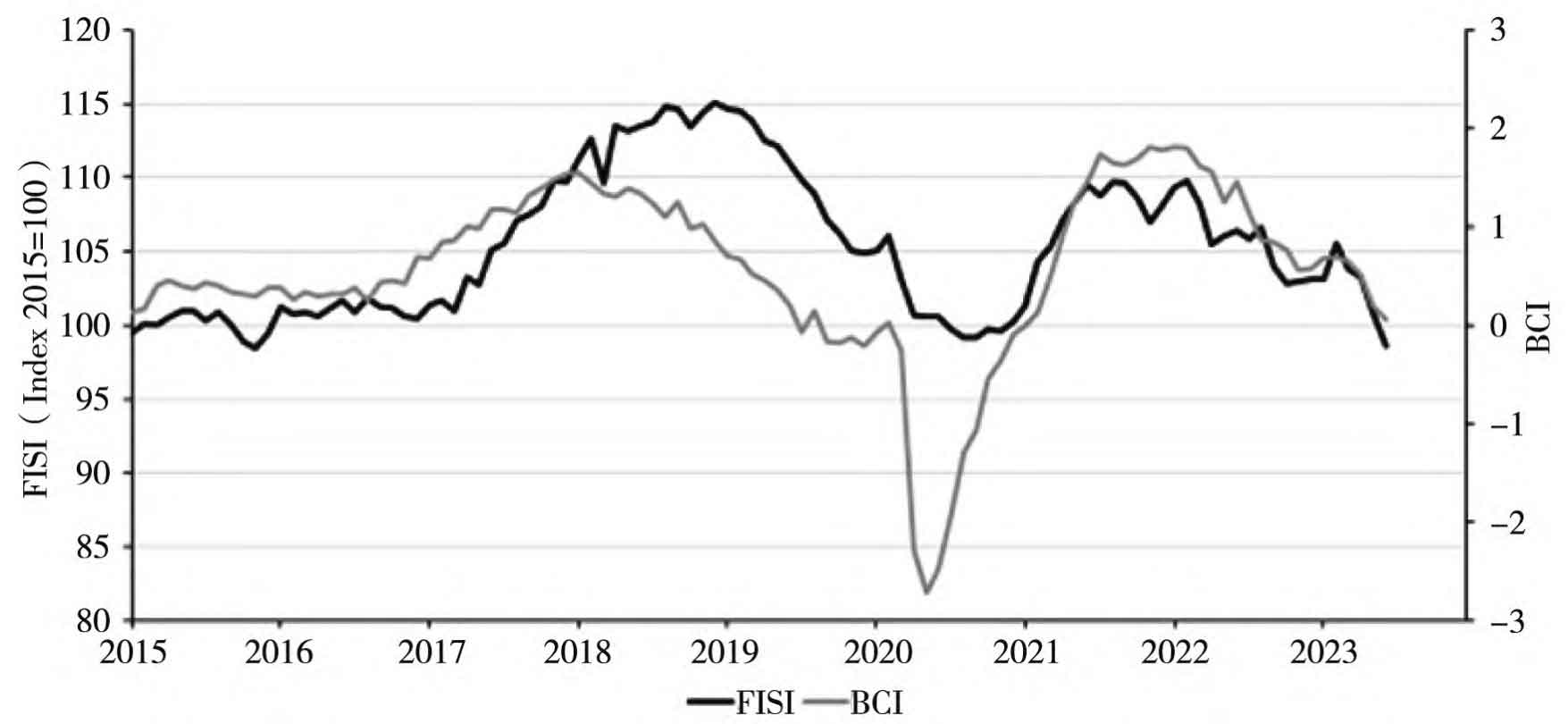
It is worrying that this negative trend is still intensifying. Although the backlog of orders is still high, it is being digested, and new orders from several industries of casting manufacturers seem to be collapsing across the board. Meanwhile, there are no signs of improvement, especially with pessimistic expectations for the next six months. Although in the past few months, due to statistical base effects, the development status of steel casting manufacturers and non-ferrous metal casting manufacturers has been opposite, currently, casting manufacturers of all material groups have had a negative evaluation of their business compared to the previous month. The Business Climate Index (BCI) decreased by 0.13 points in June to 0.06 points. Therefore, the sentiment index of European casting manufacturers has now almost returned to the level of the late 2020 pandemic, when the index became negative. Overall, the sales prices of component manufacturers in the next month are expected to decrease along with the current production and order levels.
The European Casting Manufacturers Sentiment Index is the earliest comprehensive index to provide information on the efficiency of the European casting industry. This report is published monthly by the European Foundry Association (CAEF) and is based on survey results from casting manufacturers. CAEF members need to evaluate the current business situation of the casting manufacturer industry and make expectations for the next six months.
The Business Climate Indicator (BCI) is an indicator released by the European Commission. The Business Prosperity Index evaluates the development status of casting manufacturers in the Eurozone on a monthly basis, and uses five industry surveys to weigh their production trends, order books, export order books, inventory, and production expectations.
Chapter 9:Wopaca Castings Manufacturers New Horizontal Molding Line
Waupaca castings manufacturers are expanding production capacity at Waupaca No.1 castings manufacturers in Wisconsin, adding horizontal molding lines to existing vertical molding capacity.
The castings manufacturers are recognized as a leader in the vertical molding field of green sand, and expanding production to horizontal molding will diversify its product portfolio. To commemorate this event, the castings manufacturers held the “First Pouring” event on April 18, 2023.
“We are making this investment as a direct response to customer needs,” said Mike Nikolai, President, Chief Operating Officer, and CEO of Wopaca Castings Manufacturers. “We have made strategic capital investments in key production areas, including the use of material processing automation, and now we are adapting to customers’ needs by providing horizontal and vertical styling.”
This production expansion directly solves customers’ concerns about the high tooling cost of small batch complex parts previously produced using vertical molding technology.
“Waupaca Castings Manufacturers are known for their mass production,” said James Newsome, Vice President of Sales and Marketing at Waupaca Castings Manufacturers.
By adding horizontal molding lines, our customers have a value-added service solution that can produce small batches of complex parts. Parts suitable for horizontal molding production include shells, covers, turbine bearing shells, spools, pulleys, and castings manufacturers with complex core designs.
The new styling line will begin installation in February 2023. The casting manufacturer is installing a Sinto horizontal molding machine, which will be the first of its kind to be put into use in the United States. Its functions include:
① High speed production, with a molding speed of 200 boxes/hour;
② Quickly replace the template within 18 seconds of the cycle time;
③ Excellent mold strength and dimensional accuracy;
④ Automatic core removal;
⑤ Laser guided automatic pouring;
⑥ This styling line is suitable for the existing footprint and space of the factory.
The Xindong horizontal molding machine is equipped with an ExOne S-Max Pro 3D sand core printer, which can produce complex sand core components as a single sand core and quickly produce prototype castings.
“From the beginning of the project, the teams of New East America and Wopaca have been closely collaborating to plan, design, and execute the project to seamlessly integrate it into Wopaca’s factory,” said Michael Halsband, CEO of New East America. “With Wopaca’s experienced casting manufacturer employees and Xindong’s intelligent casting technology, we believe that the system will set new performance standards for the speed of horizontal molding machines in North America.”
The new process enables Wopaca casting manufacturers to quickly replace double-sided template fixtures with existing sizes that are the same or smaller, in response to urgent customer deadlines.
Waupaca Cast Iron Plant is the largest casting manufacturer in North America, with its cast iron production, machining, and finishing factories located in Wisconsin, Michigan, and Indiana in the United States. Every day, 4000 team members melt 9500 tons of durable gray cast iron, ductile iron, and isothermal quenched ductile iron. Wopaca casting manufacturers produce iron castings for some more demanding applications, including construction, agriculture, oil and gas, industry, and the global railway market.
Chapter 10:RESAND’s casting sand treatment technology applied in castings manufacturers
RESAND (formerly known as Recycling Finland) has developed a casting sand treatment/recycling technology and developed a modular sand recycling plant using this technology. The recycling plant conducts heat and mechanical treatment on waste sand to improve the recovery rate of casting sand and reduce the consumption of raw sand.
Since 2020, the company has been processing waste sand from three Finnish castings manufacturers, Nuutaj ä rvi. Since the installation of a sand treatment workshop by TU Freiberg, a testing casting manufacturer in Germany, Finnish casting manufacturer Raahe Valimo Oy has been cooperating with the RESAND factory since early 2023.
Founded in 1919, Lakh Valimo Casting Manufacturer is still a sustainable castings manufacturers producing steel castings for well-known customers across Europe. Castings manufacturers produce approximately 1000 tons of steel castings of various sizes and weights ranging from 10 to 5000 kg per year. Castings manufacturers naturally set the highest standards for sustainability and carefully consider the flow of raw and auxiliary materials.
1000 tons of steel castings used to require approximately 2500 tons of silica sand, most of which were imported from Belgium by ship. The abandoned sand was once dumped in a landfill, but it is now strictly prohibited. This is the reason for setting up a sand treatment workshop directly at the castings manufacturer’s site.
Since the beginning of 2023, RESAND has been in operation, and Raahe castings manufacturers have made preliminary discoveries and data. The advantages are as follows:
① No landfill issues, no logistics issues;
② Approximately 2200 tons of new sand can be saved annually;
③ Better sand, smaller particles;
④ Less adhesive required;
⑤ Better casting quality and surface.
Castings manufacturers typically operate their own sand yards 24 hours a day, requiring minimal maintenance and ensuring stable operation. When using existing Neuhof castings manufacturers to crush and reuse sand molds, the sand can be directly sent to the sand recycling plant located directly in front of the casting manufacturer’s building. Finnish castings manufacturers have proven that the system is effective, especially in the field.
RESAND Oy is a Finnish technology company specializing in the sand recycling industry. RESAND provides castings manufacturers with more environmentally friendly and cost-effective sand usage solutions. After a long period of research, RESAND has obtained a patent for a recycling technology that can reuse casting sand, greatly reducing the extraction of new sand and almost depleted sand and gravel resources, reducing carbon dioxide emissions, and lowering treatment and transportation costs. This unique recycling technology also significantly reduces the amount of waste sand and reduces the demand for landfill sites from castings manufacturers.
Chapter 11: Situation of European Castings Manufacturers in June 2023: Digestion of Inventory
The European Castings Manufacturers Sentiment Index (FISI) has fallen for the second consecutive time. The rating of this index is 0.5 percentage points lower than in March and reached 103.3 percentage points in June. At first, it appeared to be clearly negative, but differences were found in the analysis of individual factors.
European Castings Manufacturers have recently assessed that their current business situation is better than the previous month; On the other hand, expectations for the next six months are even more pessimistic. This is in stark contrast to the development in the past few months, where the huge gap between pessimistic expectations and positive assessments of the situation has begun to narrow.
Compared to a month ago, handling backlog orders (reserve orders) inventory can provide a more positive assessment of the current business situation. However, in the long run, if the order stimulus is not significant, it is expected that the situation will deteriorate again in the coming months.
The Business Climate Index (BCI) decreased by 0.14 points in June, bringing the index to 0.54 points. Overall, compared to the previous month, the sales price expectations and production expectations for the next month are starting to decline from a higher level. The decrease in assessed order levels further indicates the negative stimulus of orders.
The European Castings Manufacturers Sentiment Index is the earliest comprehensive index to provide performance information on European foundries. This report is published monthly by the European Foundry Association (CAEF) and is based on survey results from European castings manufacturers. CAEF members are required to evaluate the current business situation of castings manufacturers and make expectations for the next six months.
The Business Climate Index is an indicator released by the European Commission. The Business Prosperity Index evaluates the development status of the manufacturing industry in the Eurozone on a monthly basis and balances five opinions from industry surveys: production trends, order books, export order books, inventory, and production expectations.
Background information on the European Foundry Association
The European Foundry Association is the general organization of casting associations in various European countries. This organization was established in 1953 and includes 22 EU member fruit associations dedicated to promoting the economic, technological, legal, and social interests of European castings manufacturers. At the same time, the European Foundry Association carries out activities aimed at developing castings manufacturers in various countries and coordinating their common international interests. The Secretariat has been located in Dusseldorf, Germany since 1997.
The European Foundry Association represents 4400 European castings manufacturers. Nearly 260000 employees generated a revenue of 39 billion euros. European castings manufacturers recruit 20000 workers and engineers annually. The main customer industries include automotive, general engineering and construction, as well as electrical engineering. There is no industrial sector that does not use castings.