Lost wax casting is a versatile and ancient manufacturing process used to create precise and intricate metal components. This method involves creating a wax model, which is then coated with a refractory material to form a mold. The wax is melted away, leaving a cavity that is filled with molten metal to produce the final component. While lost wax casting offers excellent dimensional accuracy and surface finish, the mechanical properties of the cast components can be further enhanced through various heat treatment and surface finishing techniques. This article explores the most effective heat treatment and surface finishing methods for lost wax cast components, ensuring improved durability, strength, and performance.
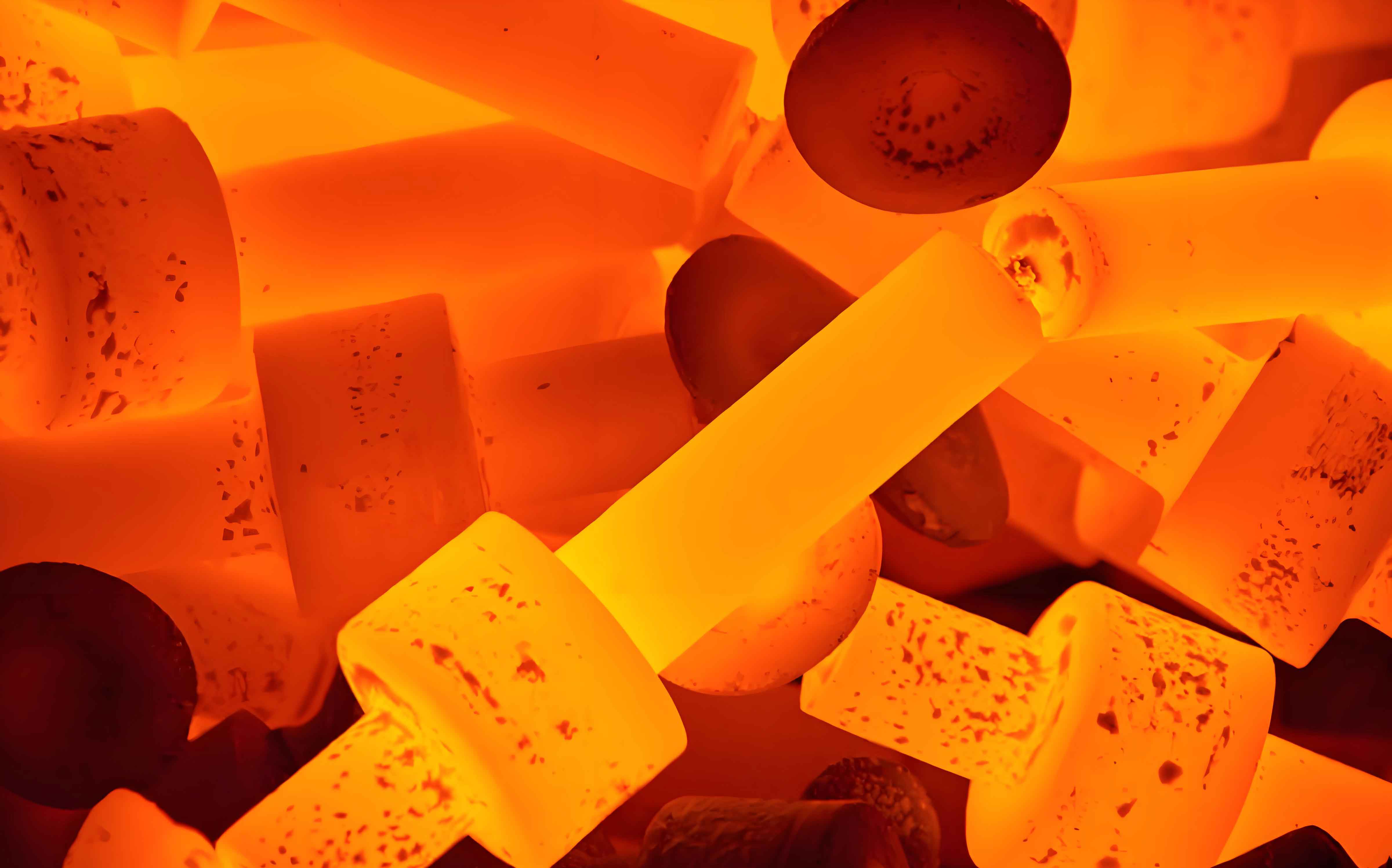
Heat Treatment Techniques for Lost Wax Cast Components
Heat treatment is a crucial step in enhancing the mechanical properties of lost wax cast components. It involves heating and cooling the metal in a controlled environment to alter its microstructure and properties. The following are some common heat treatment techniques used for lost wax cast components:
1. Annealing
Annealing involves heating the cast component to a specific temperature and then slowly cooling it. This process aims to relieve internal stresses, increase ductility, and improve machinability.
- Procedure:
- Heat the component to a temperature between 600°C and 900°C.
- Hold the component at this temperature for a predetermined period.
- Allow the component to cool slowly in the furnace.
Benefits of Annealing |
---|
Reduces internal stresses |
Enhances ductility |
Improves machinability |
2. Normalizing
Normalizing involves heating the cast component to a temperature above its recrystallization point and then air cooling it. This process refines the grain structure, enhances strength, and improves toughness.
- Procedure:
- Heat the component to a temperature between 800°C and 950°C.
- Hold the component at this temperature to ensure uniform heating.
- Allow the component to cool in still air.
Benefits of Normalizing |
---|
Refines grain structure |
Enhances strength |
Improves toughness |
3. Quenching and Tempering
Quenching and tempering is a two-step process that involves rapid cooling (quenching) followed by reheating (tempering). This technique enhances hardness and strength while maintaining sufficient toughness.
- Procedure:
- Heat the component to a temperature between 850°C and 950°C.
- Quench the component in water, oil, or air.
- Reheat the component to a temperature between 150°C and 700°C.
- Hold the component at the tempering temperature, then allow it to cool.
Benefits of Quenching and Tempering |
---|
Increases hardness |
Enhances strength |
Maintains toughness |
4. Solution Heat Treatment
Solution heat treatment involves heating the component to a temperature where alloying elements dissolve to form a single-phase solution. This process is followed by rapid cooling to retain the solution structure.
- Procedure:
- Heat the component to a temperature between 480°C and 540°C.
- Hold the component at this temperature to achieve a homogeneous solution.
- Quench the component rapidly to retain the solution structure.
Benefits of Solution Heat Treatment |
---|
Enhances strength |
Improves corrosion resistance |
Increases ductility |
Surface Finishing Techniques for Lost Wax Cast Components
Surface finishing techniques are essential for improving the aesthetic appearance, corrosion resistance, and wear resistance of lost wax cast components. The following are some common surface finishing techniques used for these components:
1. Sand Blasting
Sand blasting involves propelling abrasive particles against the component’s surface to remove imperfections and create a uniform finish. This technique is widely used for cleaning and surface preparation.
- Procedure:
- Use compressed air to propel abrasive particles (such as sand or grit) against the component’s surface.
- Adjust the pressure and particle size to achieve the desired finish.
Benefits of Sand Blasting |
---|
Removes surface imperfections |
Creates a uniform finish |
Prepares surface for coating |
2. Polishing
Polishing involves using abrasive materials to smooth and shine the component’s surface. This technique is used to achieve a mirror-like finish and enhance the component’s aesthetic appeal.
- Procedure:
- Use progressively finer abrasive materials (such as sandpaper or polishing compounds) to smooth the surface.
- Apply a polishing compound and use a polishing wheel to achieve a high-gloss finish.
Benefits of Polishing |
---|
Achieves a mirror-like finish |
Enhances aesthetic appeal |
Improves corrosion resistance |
3. Electroplating
Electroplating involves depositing a thin layer of metal onto the component’s surface using an electric current. This technique is used to enhance corrosion resistance, wear resistance, and appearance.
- Procedure:
- Prepare the component’s surface by cleaning and removing contaminants.
- Immerse the component in an electrolyte solution containing metal ions.
- Apply an electric current to deposit the metal layer onto the component.
Benefits of Electroplating |
---|
Enhances corrosion resistance |
Improves wear resistance |
Provides a decorative finish |
4. Anodizing
Anodizing is an electrochemical process that forms a protective oxide layer on the component’s surface. This technique is commonly used for aluminum components to enhance corrosion resistance and wear resistance.
- Procedure:
- Clean the component’s surface to remove impurities.
- Immerse the component in an electrolytic solution.
- Apply an electric current to form the oxide layer on the surface.
Benefits of Anodizing |
---|
Enhances corrosion resistance |
Improves wear resistance |
Provides a decorative finish |
5. Powder Coating
Powder coating involves applying a dry powder to the component’s surface and then curing it under heat to form a protective layer. This technique is used to enhance durability, corrosion resistance, and appearance.
- Procedure:
- Clean and prepare the component’s surface.
- Apply the powder using an electrostatic spray gun.
- Cure the component in an oven to melt and bond the powder.
Benefits of Powder Coating |
---|
Enhances durability |
Improves corrosion resistance |
Provides a decorative finish |
Conclusion
Heat treatment and surface finishing techniques are essential for optimizing the properties and performance of lost wax cast components. By carefully selecting and applying these methods, manufacturers can produce components with superior mechanical properties, enhanced durability, and improved aesthetic appeal. Understanding the specific requirements of each application and the capabilities of different techniques allows for the production of high-quality components that meet the demanding standards of various industries.