Identifying and resolving heat treatment defects requires a systematic approach and a thorough understanding of the heat treatment process. Here is a guide to help you identify and address common heat treatment defects:
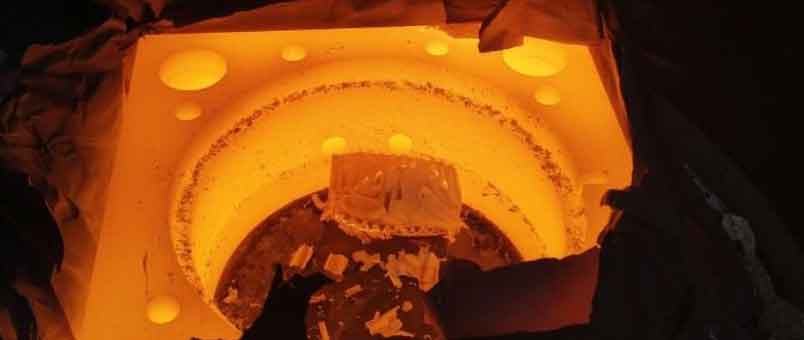
1.Visual Inspection:
Perform a visual inspection of the treated components to identify any visible defects such as cracks, warping, surface irregularities, discoloration, or excessive scaling. Visual inspection can provide initial clues about the presence of defects.
2.Non-Destructive Testing (NDT):
Utilize non-destructive testing methods such as magnetic particle inspection, liquid penetrant testing, ultrasonic testing, or radiographic testing to detect subsurface defects that may not be visible. NDT techniques can help identify internal cracks, inclusions, or other structural defects.
3.Microstructural Analysis:
Conduct microstructural analysis using techniques like optical microscopy or electron microscopy to examine the material’s microstructure. This analysis can reveal defects such as improper grain size, non-uniform phase distribution, or excessive phase transformations.
4.Hardness Testing:
Perform hardness testing across the treated component to identify variations in hardness that may indicate soft spots or inadequate hardness. Hardness tests can pinpoint regions with inconsistent heat treatment results.
5.Chemical Analysis:
Conduct chemical analysis of the material to check for deviations in composition, which can impact the heat treatment response and result in defects. Analyzing the chemical composition can help identify issues related to decarburization or improper alloying.
6.Residual Stress Measurement:
Determine the presence and magnitude of residual stresses using techniques like X-ray diffraction or strain gauging. Residual stresses can contribute to distortion or cracking, and their measurement can guide subsequent defect resolution.
7.Defect Resolution Strategies:
Once defects are identified, implement appropriate strategies to address them:
- Cracking: Determine the cause of cracking (e.g., quench cracks, thermal stress cracks) and adjust the quenching process, use different quenching media, or introduce stress-relieving techniques like tempering.
- Distortion: Assess the root cause of distortion (e.g., non-uniform heating or cooling) and adjust the process parameters, use fixtures or jigs to control component movement, or incorporate stress-relief steps in the heat treatment process.
- Soft Spots: Investigate the cause of soft spots (e.g., non-uniform heating, inadequate carbon diffusion) and optimize the heating and quenching process, ensure proper carbon availability, or adjust the carbon potential of the atmosphere.
- Surface Defects (Decarburization, Scaling): Implement proper atmosphere control, use protective coatings or inert gas environments, or adjust process parameters to prevent surface-related defects.
- Microstructural Issues: Analyze the microstructural deviations and adjust the heat treatment parameters (e.g., time, temperature) or incorporate additional treatments (e.g., annealing, homogenization) to rectify microstructural defects.
- Residual Stresses: Apply stress-relieving techniques like post-heat treatment tempering or stress relief annealing to reduce or eliminate residual stresses.
8.Process Optimization and Quality Control:
Continuously monitor and optimize the heat treatment process to prevent future defects. Implement process controls, monitor critical parameters, establish quality assurance protocols, and conduct regular inspections and tests to ensure consistent and defect-free heat treatment results.
Remember, addressing heat treatment defects often requires a combination of experience, expertise, and a thorough analysis of the specific conditions and materials involved. Collaboration between heat treatment experts, metallurgists, and quality control personnel can greatly aid in identifying and resolving heat treatment defects effectively.