Quality control is a vital aspect of the heat treatment process to ensure that the final components meet the desired specifications and performance requirements. Here are some key methods and techniques for detecting and eliminating defects during heat treatment quality control:
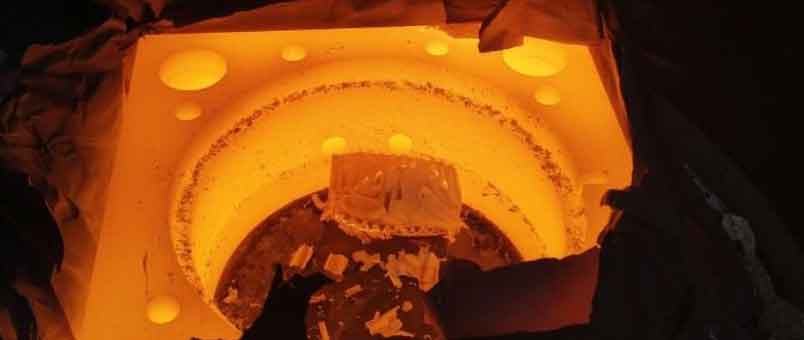
Visual Inspection:
Visual inspection is an essential first step in quality control. Trained personnel visually examine the components for any surface defects, such as cracks, warping, discoloration, or other abnormalities. This inspection can help identify obvious defects that require further investigation.
Non-Destructive Testing (NDT):
NDT methods are used to detect internal and surface defects without causing damage to the components. Common NDT techniques used in heat treatment quality control include:
- Ultrasonic Testing (UT): Utilizes high-frequency sound waves to detect internal defects, such as cracks, inclusions, or voids.Magnetic Particle Inspection (MPI): Uses magnetic fields and magnetic particles to detect surface and near-surface defects, particularly cracks.Liquid Penetrant Testing (LPT): Involves applying a liquid dye or fluorescent penetrant to the surface, which seeps into surface defects and is then detected using UV light or visual inspection.Radiographic Testing (RT): Uses X-rays or gamma rays to create images of internal defects, such as cracks, inclusions, or voids.
Hardness Testing:
Hardness testing measures the hardness of the heat-treated components using techniques like Rockwell, Brinell, or Vickers hardness testing. It ensures that the components have achieved the desired hardness level specified in the heat treatment requirements. Deviations from the target hardness can indicate issues such as incomplete heat treatment, improper quenching, or material inconsistencies.
Microstructural Analysis:
Metallographic examination involves preparing a cross-section of the heat-treated component, polishing it, and etching it to reveal the microstructure. Microscopic analysis is then performed to assess the presence of desirable phases, uniformity, grain size, and the absence of detrimental microstructural features. This analysis helps evaluate the success of the heat treatment process and identify any abnormalities or deviations.
Dimensional Inspection:
Dimensional inspection ensures that the heat-treated components meet the specified dimensional requirements. Precise measurements are taken using tools such as calipers, micrometers, or coordinate measuring machines (CMM) to verify critical dimensions, tolerances, and geometric features.
Statistical Process Control (SPC):
SPC techniques involve collecting and analyzing data during the heat treatment process to monitor and control process variables. Statistical methods such as control charts and process capability analysis help identify trends, variations, and deviations from the desired process parameters. SPC aids in early detection of process issues, allowing for timely corrective actions.
Quality Management System:
Implementing a robust quality management system, such as ISO 9001, ensures that standardized procedures, documentation, and quality control practices are followed throughout the heat treatment process. This includes proper documentation of process parameters, inspection results, traceability, and customer requirements.
Continuous Improvement:
Foster a culture of continuous improvement by regularly reviewing and analyzing quality control data, feedback from customers, and internal observations. Identify recurring defects or issues and implement corrective actions to eliminate root causes and prevent their recurrence in future heat treatment processes.
By incorporating these quality control measures into the heat treatment process, manufacturers can enhance the reliability, consistency, and performance of the heat-treated components. Collaboration with experienced heat treatment professionals, metallurgists, and quality control experts is crucial for developing effective quality control procedures and ensuring compliance with industry standards and customer requirements.