In general, as long as the process and tooling are set reasonably, the extrusion casting can be solution treated, but in the actual production, especially in the indirect extrusion casting, there are often “blistering” defects in the solution treatment, which makes the heat treatment impossible. In the late 1990s, the production of aluminum wheel for motorcycle by squeeze casting declined sharply in China. One of the important reasons was that the heat treatment technology had not passed the standard at that time. Many researches have been done at home and abroad, and the author has done some related work.
In order to control the “bubbling” defect of heat treatment, that is, to minimize the involvement of gas and slag in liquid metal, the main measures taken are as follows.
① The filling speed (sprue speed) of liquid metal should be strictly controlled, and it should be less than 0.8m/s. For direct squeeze casting, the filling speed is controlled by the speed of extrusion punch, generally between 0.1 and 0.4 m / s, while for indirect squeeze casting, it is measured by the speed of sprue or the narrowest part of casting, generally between 0.5 and 1.0 m / s.
② It is forbidden to use oil agent or wax based coating when using water agent coating. Before pouring, it is necessary to blow the water in the cylinder and mold cavity dry.
③ To solve the problem of slag collection and exhaust of the die, the matching clearance, exhaust groove, slag collection bag and ejector pin of the die are used to exhaust the die. For the castings with complex shape and strict requirements, some methods such as exhaust block, exhaust valve and even vacuum are also used to exhaust the die.
④ In the design of the feeding system and the inner runner of the mold, the vertical extrusion filling (feeding) system from the bottom to the top shall be adopted as far as possible to reduce the front impact of the liquid metal flow on the core and the cavity wall, so that the dross of the liquid metal and the solidified hard shell can be blocked in the cylinder as far as possible to form a cake or enter the slag bag, and the gas in the cavity can be discharged smoothly.
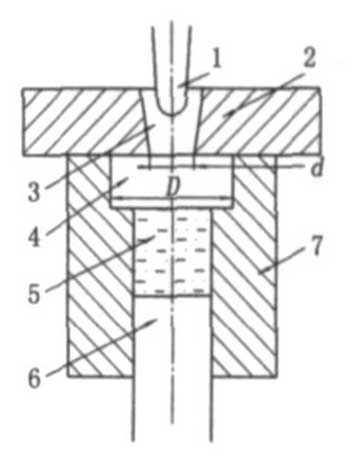
The figure is a typical design drawing of extrusion cylinder and internal sprue. In most cases, the bottom-up central feeding is more conducive to exhaust and reduce the gas entrapment than the lateral feeding.