1 Preamble
ZG15Cr2Mo1 high-pressure steam chamber heat-resistant casting is an integral part of the steam turbine. A steam turbine, also known as a steam turbine engine, is a rotating steam power unit in which high-temperature and high-pressure steam passes through a fixed nozzle The accelerated air flow is then sprayed onto the blades, so that the rotor equipped with the blade row rotates and at the same time does work externally. The steam chamber is the chamber set up for balancing the steam flow after the steam passes through the main steam valve and enters the regulating steam valve. In this paper, Solidworks is used for modeling, and the finite element analysis software ProCAST is used as the simulation platform to simulate the data simulation of the filling and solidification process of the high-pressure steam chamber, and the possible casting defects are predicted. Based on the preliminary simulation results, the three-factor three-level orthogonal simulation test was designed with the pouring temperature, pouring speed and the number of inner runners as factors, and the optimal casting process parameters were obtained. The topic is the 2023 China College Student Mechanical Engineering Innovation and Creativity Competition: The 14th Casting Process Design Competition B, which comes from first-line production enterprises and is a casting process design problem that has yet to be solved by enterprises, so the research results have important practical application value.
2 Introduction to the characteristics and process of castings
The three-dimensional structure of the heat-resistant casting in the high-pressure steam chamber is shown in Figure 1. The casting profile size is 1648mm×620mm×1077mm, the weight is 1957.8kg, the maximum wall thickness is 153mm, the minimum wall thickness is 30mm, and the maximum hole diameter is 240mm. The chemical composition of the vapor chamber material ZG15Cr2Mo1 is shown in Table 1. It is made of alloy cast steel with a density of 7.8g/cm3, a solidus temperature of 1135 °C and a liquidus temperature of 1501 °C. Because cast steel has a high melting point, poor fluidity, easy oxidation and harvesting Therefore, in the actual casting process, there are often defects such as shrinkage porosity and shrinkage porosity due to insufficient shrinkage, and the wall thickness of the heat-resistant castings in the high-temperature steam chamber is large, and there are many uncertainties in cooling and solidification. According to the design rules of the steel casting gating system, the pouring scheme preliminarily designed in this paper adopts an open gating system, which is poured with a bottom injection package, and a riser is set at the thick part of the casting, and phenolic trees are selected for the sand core Grease from hard sand. The preliminary scheme of the high-temperature steam chamber heat-resistant casting casting system is shown in Figure 2.

Fig.1 Schematic diagram of the three-dimensional structure of the casting
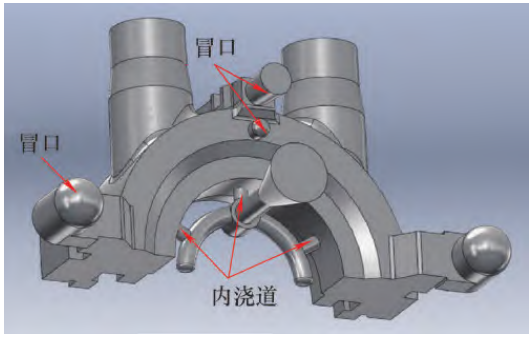
Fig.2. Preliminary scheme of heat-resistant casting system in high-temperature steam chamber
3 Numerical simulation pretreatment of casting process
3.1 Model Transformation and Meshing
Based on the high-pressure steam chamber steel casting part drawing, the 3D modeling was carried out by Solidworks, and then transferred to the IGS file grid import the solids into the Visual-Mesh module of the ProCAST software for finite element meshing. As the core of data analysis, meshing has a decisive impact on the time and accuracy of simulation analysis. Here, the size of the meshing element of the sand box and sand core part is set to 100mm, and the size of the meshing unit of the casting part and the gating system is 30mm, and finally 28,448 surface meshes and 407487 individuals are generated Grid.
3.2 Boundary conditions and operating parameter settings
The ProCAST software CAST module was used to numerically simulate the filling and solidification process. The main parameters of pouring are: pouring temperature, pouring speed, each part of the material and heat transfer coefficient. According to the material of cast steel Qualitative characteristics (the liquidus temperature of ZG15Cr2Mo1 is 1501 °C) and the casting process characteristics (sand gravity casting, the maximum wall thickness is 153mm, the minimum wall thickness is 30mm, and the maximum hole diameter is φ 240mm), 1600 °C is selected for simulation at the beginning of this paper, the pouring speed is selected as 120kg/s, the gravity is set to the positive direction of the Z-axis, and the natural air cooling. The interfacial heat transfer coefficient is selected as NCOINC type, and the interfacial heat transfer coefficient between the casting and the sand mold is taken ash=500W/(m2•K), and other general parameters remain the default.
4 Analysis of the simulation results of the preliminary scheme of the casting process
4.1 Analysis of the simulation results of the temperature field in the filling and solidification processThrough the Viewcast module, the distribution results of the temperature field of the casting are observed, and the simulation results of the gating system are shown in Figure 3. As can be seen from Figure 3, the molten metal filling is relatively stable, the cavity can be filled completely, there is no obvious splashing, the metal fluidity is good, the molten metal rises slowly in the cavity, and the gas in the cavity can be discharged smoothly during the filling process.
4.2 Solidity simulation results of solidification process The preliminary scheme of the casting process simulates the temperature field at the end of solidification, as shown in Figure 4. According to the principle of sequential solidification, by observing and analyzing the solidification sequence of the casting, it is possible to determine the area that is isolated and unretracted due to the final solidification of the molten metal, and this area has a high probability of defects. As can be seen from Figure 4, the top boss and the bottom thick place are finally solidified, which is the most likely position to produce defects.
4.3 Prediction of shrinkage porosity and shrinkage porosity defects of castings ProCAST casting simulation software can predict the areas where loose and shrinkage porosity are most likely to occur, and the location of defects is predicted as shown in Figure 5. As can be seen from Figure 5, its porosity is 2.834%. The shrinkage porosity is mainly distributed at the riser, and there are almost no shrinkage porosity in the part used in the casting, and the shrinkage porosity is concentrated in the thick part of the casting, and the scheme of transferring the shrinkage porosity to the riser by increasing the riser is feasible, but it is necessary to carry out further comparative tests on various parameters to obtain the best results.

Fig.3. Flow field of the filling process in the preliminary scheme of the casting process
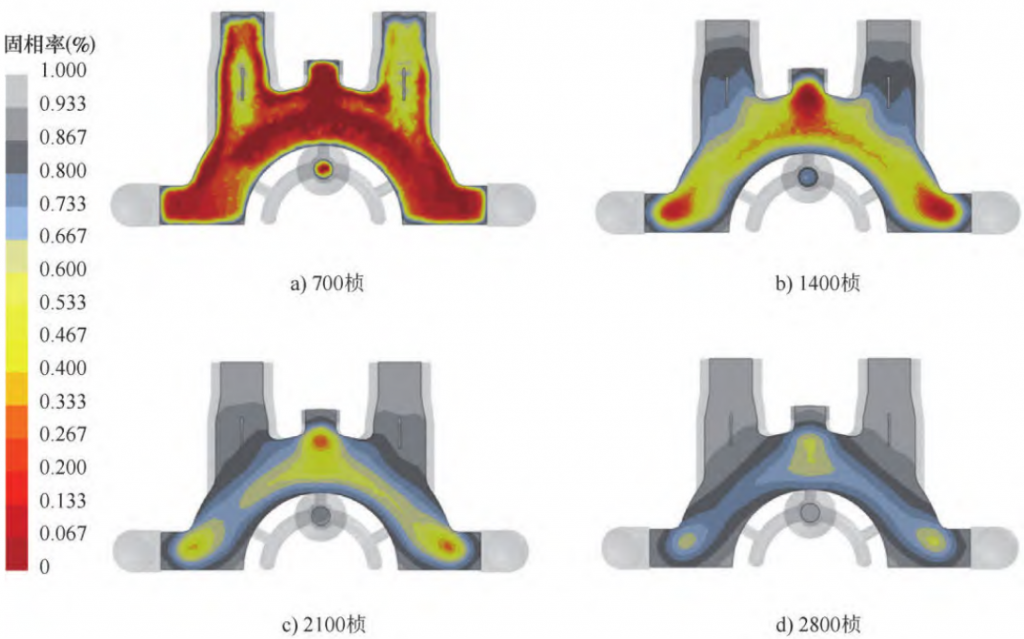
Fig.4. The preliminary scheme of the casting process simulates the temperature field at the end of solidification
5 Orthogonal test simulation and optimization of casting process parameters
5.1 Orthogonal experimental design
In order to reduce the defect rate of castings, the archgonal test simulation and optimization of three levels and three factors were carried out on the pouring time, pouring temperature and the number of inner runners, so as to obtain a better casting process scheme.
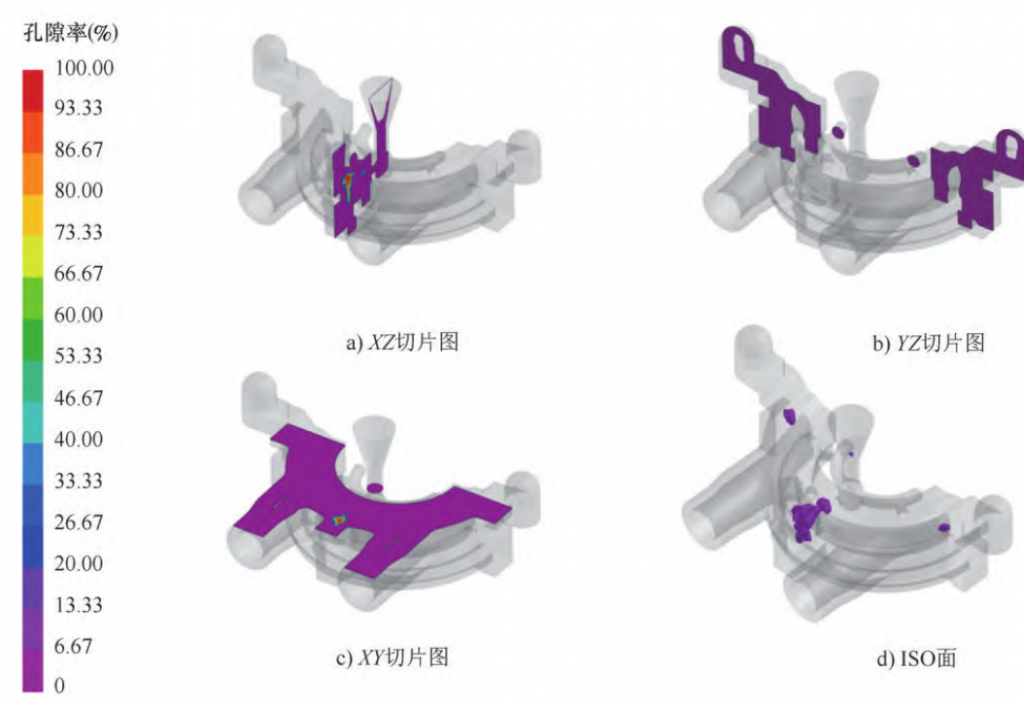
Fig.5. Prediction of shrinkage porosity and shrinkage position of the preliminary scheme of casting process
5.2 Analysis of orthogonal test simulation results
The casting simulation defects of the different test comparison groups are shown in Figure 6. As can be seen from Table 3 and Fig. 6, the influencing factors of the porosity of steel castings in the high-pressure steam chamber are the number of inner runners, pouring speed and pouring temperature, among which the small porosity is the goal, and the optimal casting process parameter combination is A2B3C2, that is, the pouring temperature is 1600°C, the pouring speed is 125kg/s and the number of inner runners is 3.
5.3 Simulation results of the optimization scheme
Based on the analysis of the orthogonal test simulation results, the optimization parameters of the casting process (pouring temperature 1600°C, pouring speed 125kg/s and the number of inner runners are 3), and the filling and solidification simulation studies were carried out by ProCAST software. Fig. 7~Fig. 9 show the filling process, solidification temperature field and pore defect simulation, respectively. From the simulation results, it can be seen that the porosity is reduced to 1.025% after the complete filling of the optimized process, and the porosity of the top boss and the bottom thickness is finally solidified, which is significantly lower than the porosity of 2.834% in the original scheme. At this time, the problem of shrinkage porosity and shrinkage porosity of the casting has been significantly improved, the shrinkage porosity is concentrated at the riser, the shrinkage porosity range is significantly reduced, and the casting effect is good. In the subsequent optimization process of the casting process, measures such as changing the size and number of risers and their positions, changing the size of the chilled iron, and adding thermal insulation risers can also be used to further eliminate shrinkage defects.
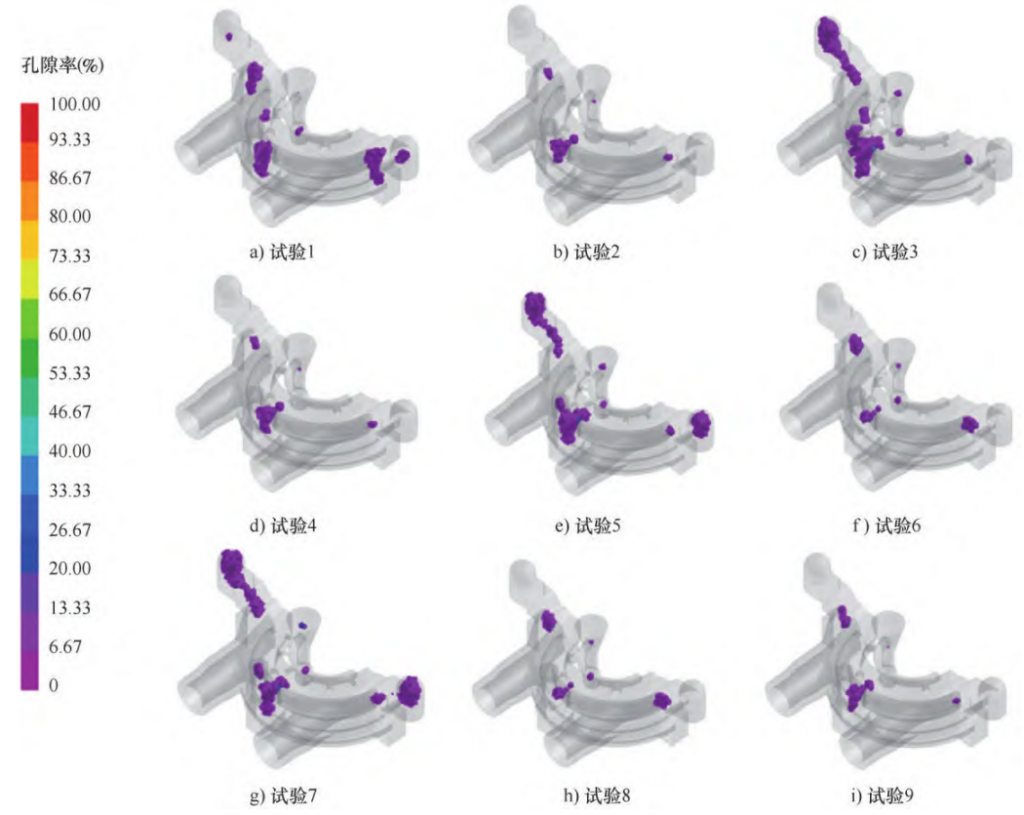
Fig.6. Casting simulation defects in different test comparison groups
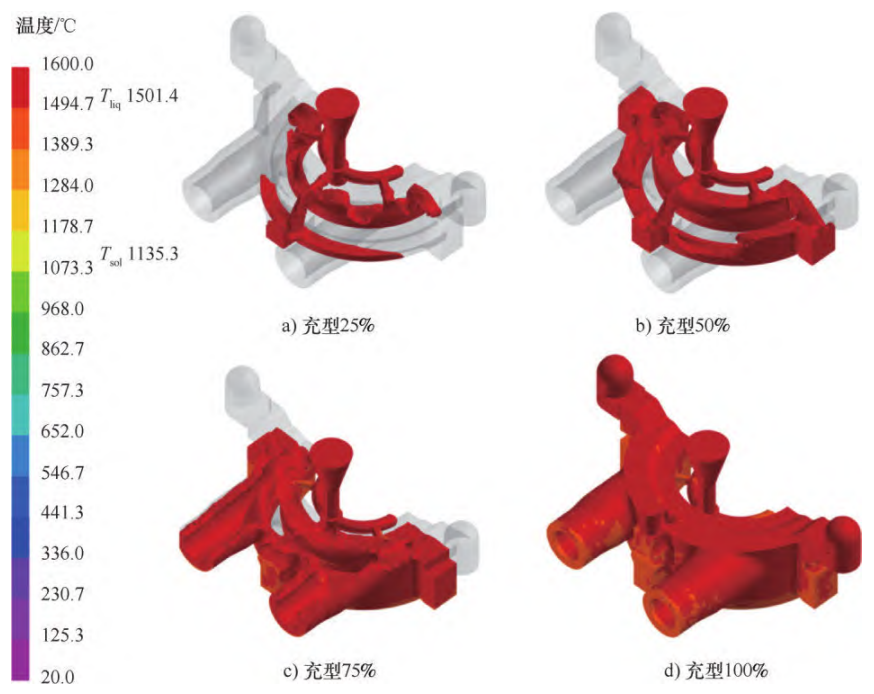
Fig.7. Flow field of casting filling process under optimized process
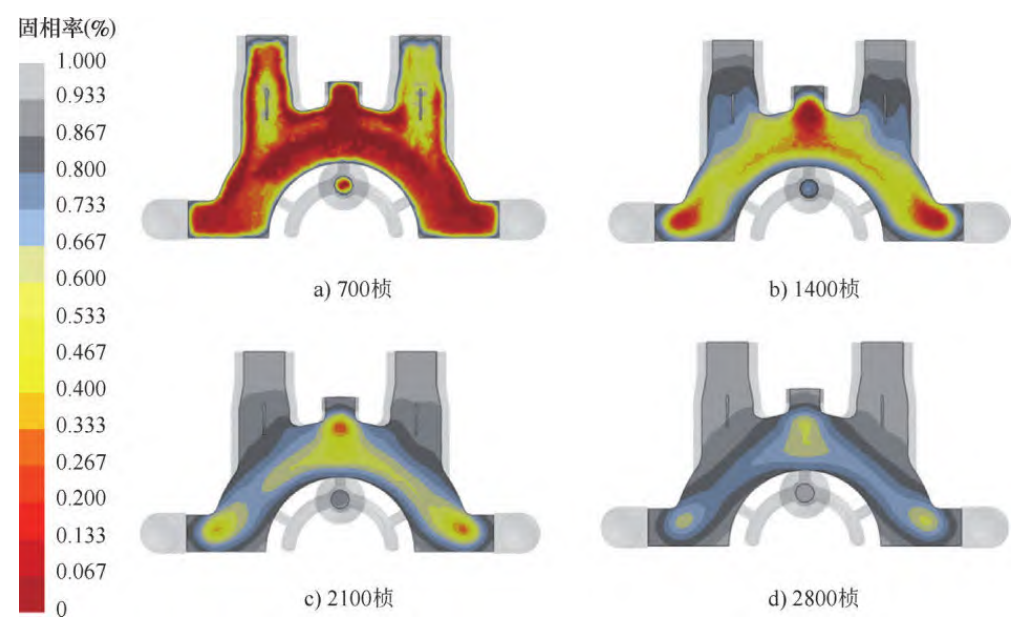
Fig.8. Temperature field at the end of solidification of castings under the optimized process
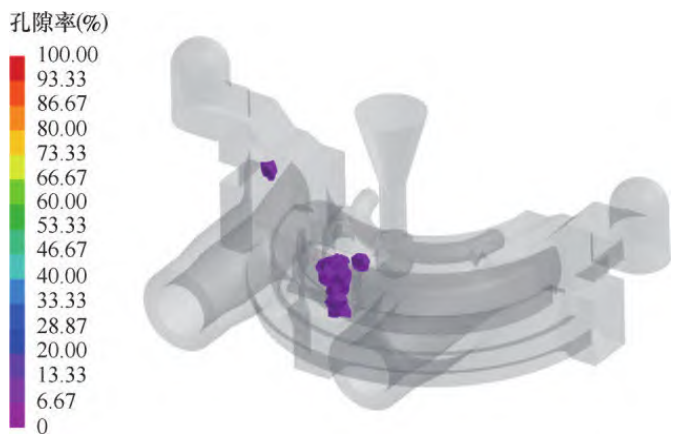
Fig.9 Prediction of porosity and porosity position under optimized process
6 Concluding remarks
1) Based on the high-pressure steam chamber ZG15Cr2Mo1 material structure
point, the casting process scheme was preliminarily designed. The simulation results show that the top boss and the thick bottom are the most prone to defects, and the porosity is 2.834%.
2) The orthogonal simulation test optimization study was carried out with the pouring temperature, pouring speed and the number of inner gatings, and the optimal casting process parameters were obtained with porosity as the performance index: pouring temperature 1600°C and pouring
The speed is 125kg/s and the number of inner runners is 3, and the porosity of the casting is reduced to 1.025%, and the casting quality is significantly improved.