Thermomechanical fatigue is indispensable for evaluating the high temperature life of aero-engine components and is one of the key performance indexes for component design.The thermomechanical fatigue behavior of cast Ti-48Al-2Cr-2Nb alloy, which has been applied by GE Company in USA, was studied and compared with the related isothermal low cycle fatigue behavior to investigate the high temperature fatigue resistance and fracture mechanism of the alloy under the simultaneous action of alternating temperature load and force load.
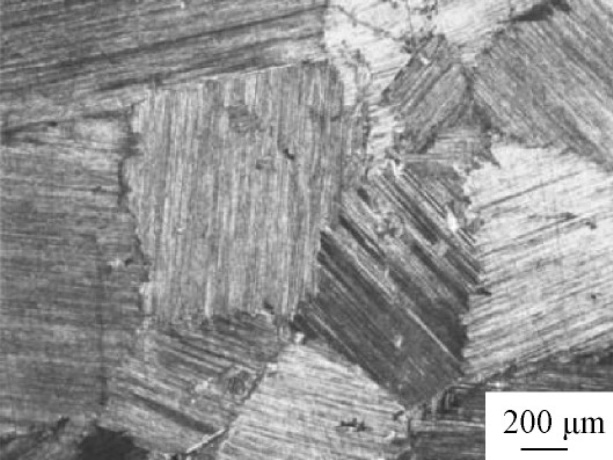
Ti-48Al-2Cr-2Nb alloy is melted in vacuum magnetic suspension furnace and then hot isostatic pressing is carried out at 1 280 C, 175 MPa and 4 h to obtain casting blank of Ti-Al alloy.The initial microstructure of the alloy is observed by means of an optical microscope (OM). It can be seen that the alloy is full lamellar (FL) structure (see Figure 1), but a small amount of gamma phase precipitates can be seen at the serrated boundary of the lamellar layer.The lamellae are relatively large with an average size of about 600 um.Figure 2 shows the transmission electron microscopy (TEM) morphology of the alloy. Two-phase lamellar structure of gamma/alpha 2 can be seen. A large number of stacking faults exist in the gamma strips, as shown by the arrows in the figure.
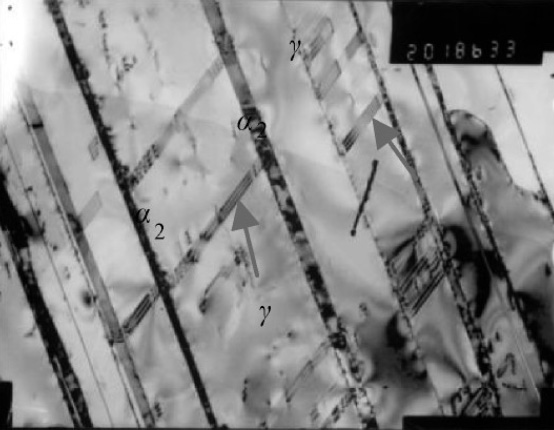