Combined with the production conditions and experience, the casting shrinkage is 1% in length direction, 0.8% in height direction and width direction, 1.5 ° in sand core draft angle, 1 ° to 3 ° in external mold draft angle, 5 mm in one side of casting machining allowance, 0.2 mm in sand core coating layer, 0.3 mm in upper and lower outer cavity coating layer, and 0.2 mm negative parting number of core box. The mold consists of 8 main cores, front and rear end cores, water channel cores, tappet chamber cores, 14 cores and upper and lower profiles, as shown in Fig. 1. Triethylamine cold box core making process is used for the main sand core, and furan resin sand is used for other cores and shapes.
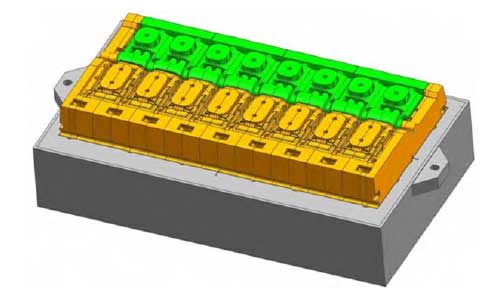
The horizontal pouring system is generally smaller than the vertical pouring head, and the gating system is located on one side of the body. In order to realize the stable filling of molten iron into the mold cavity and reduce the turbulent sand flushing of molten iron, the layered ladder casting process is adopted. The bottom runner is introduced from the machine foot flange surface, and the middle runner is introduced from the crankcase bearing seat. The molten iron flows directly from the filter screen to the bottom of the machine foot through the sprue, and a runner is added at the bottom layer. In this way, during the pouring process, the molten metal first reaches the bottom runner, and then is introduced into the mold cavity by the bottom runner, and the bottom runner is filled, When the molten iron rises to a certain height, the molten metal enters the mold cavity from the middle runner, which makes the temperature field of the molten metal in the mold more reasonable, which is conducive to the feeding of the casting, and avoids the problem that the middle pouring and the bottom pouring may be simultaneously fed into the molten iron. Figure 2 shows a schematic diagram of the gating system.
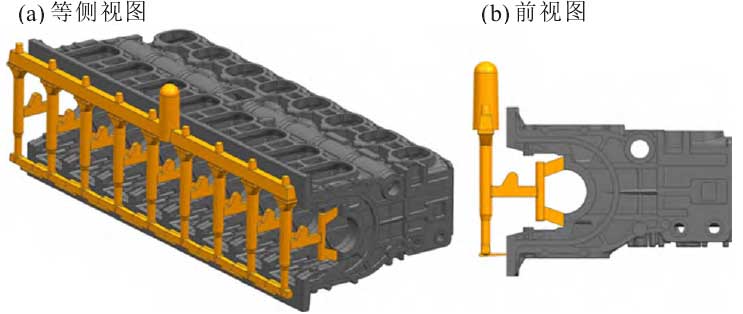