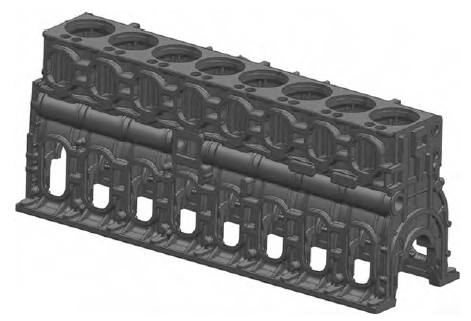
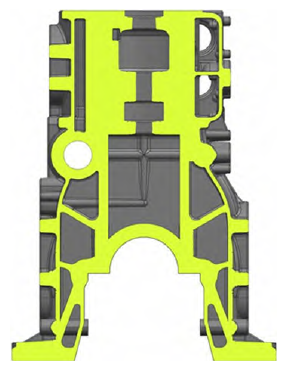
The engine body is an 8-cylinder in-line structure. Its appearance is shown in Fig. 1 and its sectional view is shown in Fig. 2. The total length of the body is 2152 mm, the width is 658 mm, the height is 873 mm, the body weight is 1477 kg, and the material is HT250 gray iron, which belongs to large frame casting. There is a cooling circulating water jacket around the cylinder liner of the engine block. The inner cavity adopts the structure design of wet cylinder sleeve water jacket. The outer wall directly contacts with the cooling water, and the double water channel design is adopted. The water inlet hole with a cross section of 60mm × 40mm is designed between the outer water channel and the cylinder liner water jacket structure, as shown in Fig. 3. The body size is large, the sand core has a large amount of gas, and it is difficult to exhaust gas. It is easy to produce shrinkage cavity, shrinkage porosity and other casting defects. The external water channel is long and flat structure, so it is very difficult to locate and fasten the double channel sand core, so it is easy to float the core in the casting process.
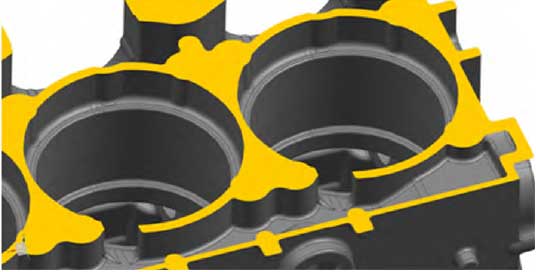
The horizontal casting process is mainly to place the machine body horizontally and divide the mold into upper and lower parts with the horizontal plane of the cylinder hole as the parting surface. The horizontal casting process is adopted. The sand core of the water channel is placed horizontally. The water inlet and outlet at both ends of the channel sand core are respectively designed with cylindrical core heads, and the bottom surface of the channel sand core is designed with multiple sand core heads for supporting and fixing, as shown in Fig. 4. In the horizontal pouring process, the lower core assembly of water channel sand core is easy to operate, and the sand core positioning is accurate. Through the assembly of sand core at the front and rear end faces, the water channel sand core can be compressed and the sand core can be prevented from floating during the pouring process. The disadvantages of horizontal casting process are: the static pressure head of molten iron is small, the filling speed is slow in the later stage of pouring, the feeding capacity is poor, and the exhaust gas is not smooth during pouring; the gas in the mold cavity and sand core can only be discharged by the exhaust channel at the core head and the upper mold, which is easy to form air hole defects.
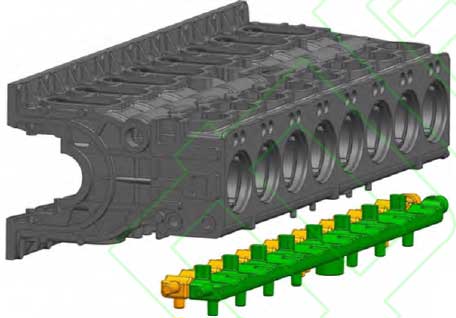
The vertical casting split box process scheme is that the cylinder hole face downward, the outer shape of the body is formed by the left and right sand cores, the front and rear ends sand cores, the upper and lower boxes, and the inner shape of the body is formed by the main body sand core and water channel sand core respectively. The vertical pouring split box process is adopted, and the sand core of the channel is placed vertically, as shown in Fig. 5. The channel sand core positioning is concentrated on the right side of the sand core, and the cylindrical core heads at both ends of the channel sand core are clamped by the front and rear ends of the sand core assembly to realize the positioning and fastening of the channel sand core. The disadvantages of the vertical casting split box process scheme are: the sand core of the waterway should be fixed on the right side of the sand core first, and then be assembled with the sand core at the front and rear ends. The sand core assembly operation is difficult, the process is many and complex, the efficiency is low, the labor intensity is high, and the operation skill requirements are high.
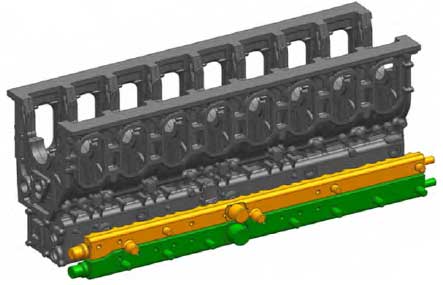