Rolling mill vibration theory is critical for sheet quality and equipment stability. This work addresses horizontal nonlinear vibrations through fractional-order modeling and introduces a hydraulic intelligent lining plate for vibration absorption. We establish a fractional-order dynamic model considering horizontal dynamic excitation from rolling forces, nonlinear damping/stiffness between bearing seats and frames, and mechanical gaps:
$$\ddot{x}(t) + \omega_0^2 x(t) + \epsilon \left[ \alpha (x^2(t) – 1) \dot{x}(t) + \beta x^3(t) \right] + \epsilon K_1 D^p x(t) = \epsilon f \cos(\omega t)$$
where $D^p$ denotes the fractional derivative of order $p \in (0,1]$. The equivalent damping $C(p)$ and stiffness $K(p)$ are derived as:
$$
\begin{align*}
C(p) &= c – \frac{a c}{4} + \frac{a K \omega^p}{4} \sin\left(\frac{\pi p}{2}\right) \\
K(p) &= k_1 + \frac{3}{4} k_2 a^2 + K \omega^p \cos\left(\frac{\pi p}{2}\right)
\end{align*}
$$
Amplitude-frequency characteristics are governed by:
$$A a^6 + B a^4 + C a^2 + D = 0$$
where coefficients depend on $c$, $k_1$, $k_2$, $K$, $p$, and $\omega$. Parametric studies reveal:
Parameter | Effect on Amplitude-Frequency Response |
---|---|
Rolling force $F \uparrow$ | Resonance amplitude and bandwidth increase |
Damping $c \uparrow$ | Resonance amplitude and bandwidth decrease |
Fractional order $p \uparrow$ | Curve shifts left, amplitude decreases |
Fractional coefficient $K \uparrow$ | Curve shifts left, amplitude decreases |
To control vibrations, we designed a hydraulic intelligent lining plate installed between the rolling mill frame and upper work roll bearing seat. This lining plate eliminates mechanical gaps and provides controllable damping ($c_0$) and stiffness ($k_0$):
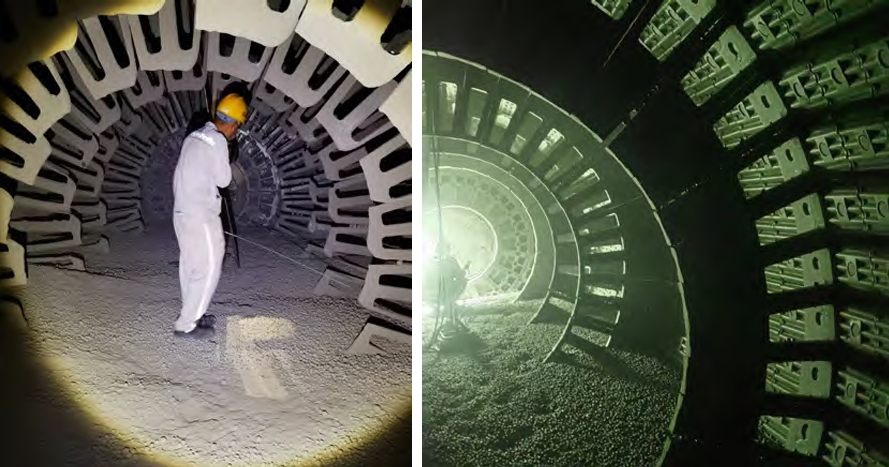
The governing equation with the lining plate becomes:
$$
m\ddot{x} + \left[ c(x^2 – 1)\dot{x} + c_0\dot{x} \right] + \left[ (k_1 + k_0)x + k_2x^3 \right] + K D^p x = F\cos(\omega t)
$$
The lining plate’s equivalent damping and stiffness are:
$$
\begin{align*}
c_0 &= \frac{16\lambda_0 \rho l’ Q_{out}}{\pi d^5} + \frac{16h_f \rho Q_{out}}{\pi d^5} \\
k_0 &= \frac{E_e A^2}{V}
\end{align*}
$$
where $E_e$ is oil bulk modulus, $A$ is cross-sectional area, and $V$ is oil volume. Amplitude reduction follows:
$$a_{\text{reduction}} = \frac{a_{\text{without}} – a_{\text{with}}}{a_{\text{without}}} \times 100\%$$
Multi-scale analysis confirms vibration suppression:
$$
\left[ -\frac{3\beta a^3}{8\omega} + \left( \sigma – \frac{K_1 \omega^{p-1}}{4} \cos\frac{\pi p}{2} \right)a \right]^2 + \left( \frac{\alpha a}{2} – \frac{A a}{2} \right)^2 = \frac{f^2}{4\omega^2}
$$
Numerical simulations demonstrate significant amplitude reduction:
Lining Plate State | Vibration Amplitude (mm) | Resonance Bandwidth (Hz) |
---|---|---|
Without lining plate | 0.82 | 8.3 |
With lining plate ($c_0$=2, $k_0$=3) | 0.61 | 5.1 |
Experimental validation on a 150mm two-roll mill shows:
Rolling Speed (rpm) | Oil Pressure (MPa) | Vibration Energy Reduction |
---|---|---|
90 | 3 | 16.5% |
5 | 21.4% | |
7 | 26.2% | |
120 | 3 | 19.0% |
5 | 22.1% | |
7 | 26.1% | |
150 | 3 | 21.5% |
5 | 25.6% | |
7 | 28.9% |
Key advantages of the intelligent lining plate include:
- 26% average vibration amplitude reduction
- Adaptive stiffness/damping via hydraulic pressure control
- Elimination of mechanical gap-induced nonlinearities
- 50% faster stabilization time during transient vibrations
This lining plate technology provides a robust solution for horizontal vibration control in rolling mills, significantly improving product quality and equipment reliability. Future work will explore multi-field coupling effects and lubrication interface dynamics.