The figure is the schematic diagram of horizontal pouring bimetallic composite wear-resistant casting. Horizontal pouring refers to the horizontal position modeling of the mold, closing the box and pouring. The working surface of the composite wear-resistant casting adopts wear-resistant cast iron and the non working surface adopts high-quality carbon steel. In this process, two kinds of liquid metals are poured in time. When one kind of metal liquid is poured in, the second kind of metal liquid is poured after a period of time. The heat brought in by pouring the metal liquid will melt again around the solidified surface of the metal first, so as to achieve metallurgical bonding with good bonding interface. The most important process parameters for producing high-quality bimetal castings are the pouring temperature and pouring interval of molten metal. If they are not well controlled, defects such as mixing, poor bonding, cold shuts or cracks are likely to occur.
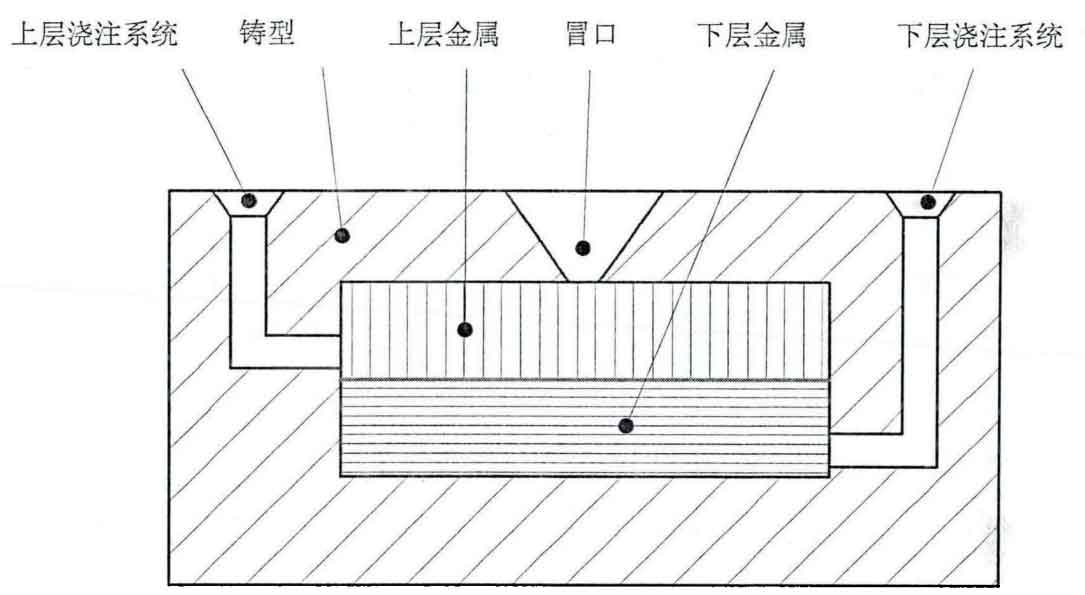
The advantages of the horizontal pouring bimetal composite casting process are that the molding and pouring system are relatively simple, the field equipment is easy to arrange, and the floor space is small. It has been widely used in flat wear-resistant parts such as crusher jaw plate and ball mill liner plate. Lijiwen et al. Further tested the double liquid triple compound pouring process on this basis, and successfully applied it to the actual production of wear-resistant plate hammer. Good metallurgical bonding between the two metals was achieved, and the interface strength was 1.3-1.5 times that of liquid-solid composite.
In actual production, the biggest problem of this process is that it is prone to cold shut-off and mixing. In the process of horizontal pouring, if the pouring temperature is too high and the interval is too short, it will cause the mixing of two kinds of wear-resistant cast iron and carbon steel, resulting in the decline of the working performance of wear-resistant cast iron; If the pouring temperature is too low and the interval is too long, it will cause cold shut, reduce the bonding strength of the composite interface between wear-resistant cast iron and carbon steel, and it is not easy to discharge gas and inclusions. At present, the choice of pouring temperature and interval time in production is mostly determined by experience, so the composite quality stability of wear-resistant castings is poor and the casting yield is not high.
In order to improve the composite quality of wear-resistant castings, Tu Xiaohui first studied the pouring sequence of two kinds of metal liquids. It is found that the process of pouring iron first is difficult to obtain good composite castings. There are two main reasons: first, the solidus temperature of high chromium cast iron is low, and then pouring high-temperature liquid steel is easy to cause large-area melting of cast iron first, resulting in two-phase mixing; Second, oxides of chromium, manganese and silicon are easy to form on the surface of cast iron, which are difficult to reduce during the compounding process, and inclusions and pore defects are easy to form under the scouring of molten steel; In order to further improve the composite quality of wear-resistant castings, puxuedong et al. Studied the pouring interval and maximum interval of two metals on the basis of pouring steel first and pouring iron later, and established a mathematical model. The measured data are very close to the calculated results.
Yang Jingguang found that the cleaner effect of sodium tetraborate can overcome the disadvantage of weak combination of two metal materials in bimetal casting process. Sodium tetraborate has low melting point (878 ° C), high gasification temperature (1540 ° C), low density (1.72g / cm3), low viscosity, low surface tension and good wettability. It can effectively prevent metal oxidation and reduce the melting point of metal oxides. According to its characteristics, when casting the base steel in the mold, the molten sodium borate cleaner is injected around the casting system of the cast steel layer. When the second layer of cast iron metal material is poured into the casting cavity, the sodium borate liquid flows with the wave under the action of the dynamic field of the high-temperature liquid metal. Due to its low density, it will naturally float to the surface of the liquid metal. After the liquid metal fills the cavity, The sodium borate cleaning liquid flows out of the mold through the overflow tank pre opened at the top of the mold cavity to complete the task of cleaning the joint. After heat treatment, the shear strength of the joint of cast steel white cast iron bimetallic castings produced with sodium borate as cleaner exceeds 700MPa, and the impact toughness exceeds 84j / cm2, up to 79.3j/cm2. Therefore, the application of sodium borate as surface cleaner in the production of bimetal composite castings can significantly improve the bonding strength, toughness and yield of composite castings.
According to the structural characteristics of castings, park Dongxue and others set up internal and external chills and external risers to ensure full feeding of wear-resistant white cast iron Φ 1000×700、 Φ 1250×1000 high chromium cast iron carbon steel bimetallic composite plate hammer is used for crushing raw materials in cement plants. Its service life reaches 40 days and 114 days, which is 3-5 times longer than that of GAOMENG steel plate hammer; Wang Congyu used cr15mo3 high chromium cast iron and zg270-500 to form a bimetallic impact plate with good toughness and impact resistance, which solved the problem of low service life of the impact plate for a long time. The mix ratio of rigidity and iron of the impact plate is the best at 2:1. The molten steel is discharged at 1550 ° C and poured at 1500 ° C, and the molten iron is discharged at 1500 ° C and poured at 1420 ° C. the composite effect is good, Its service life is more than 1 time longer than that of high strength steel impact plate; Ran Maojun uses the impact plate, armor and hook of fan coal mill, which are made of high chromium cast iron with mass fraction of 2.4%-2.8c, 13%-15%cr, 0.5%-0.8%mn, <1%si, 1.5%-2.0%mo and <1%cu and medium carbon steel. They are installed together with the original high-strength steel castings and operate under the same working conditions. The bimetal composite lining plate is only slightly worn after 1500 hours of operation and can still be used, The original high-strength steel castings have been seriously worn after 550h operation, so they must be stopped for replacement.
Based on the working principle of jaw crusher and focusing on the problems in practical application, rongshoufan has produced bimetallic liquid composite casting jaw plate. The wear-resistant working layer is made of alloy steel with high wear resistance, and the strong and tough layer is made of cast steel with good impact paving, which fully combines the advantages of the two metal materials. The service life of the single jaw and double riser casting system is at least 2 times higher than that of the original metal casting system.