The casting industry, integral to numerous sectors such as automotive, aerospace, and industrial machinery, is undergoing a significant transformation. Leading casting products manufacturers are at the forefront of this revolution, leveraging cutting-edge technologies, innovative processes, and sustainable practices to redefine industry standards. This article explores the key advancements and strategies employed by top manufacturers to revolutionize casting production, enhancing quality, efficiency, and sustainability.
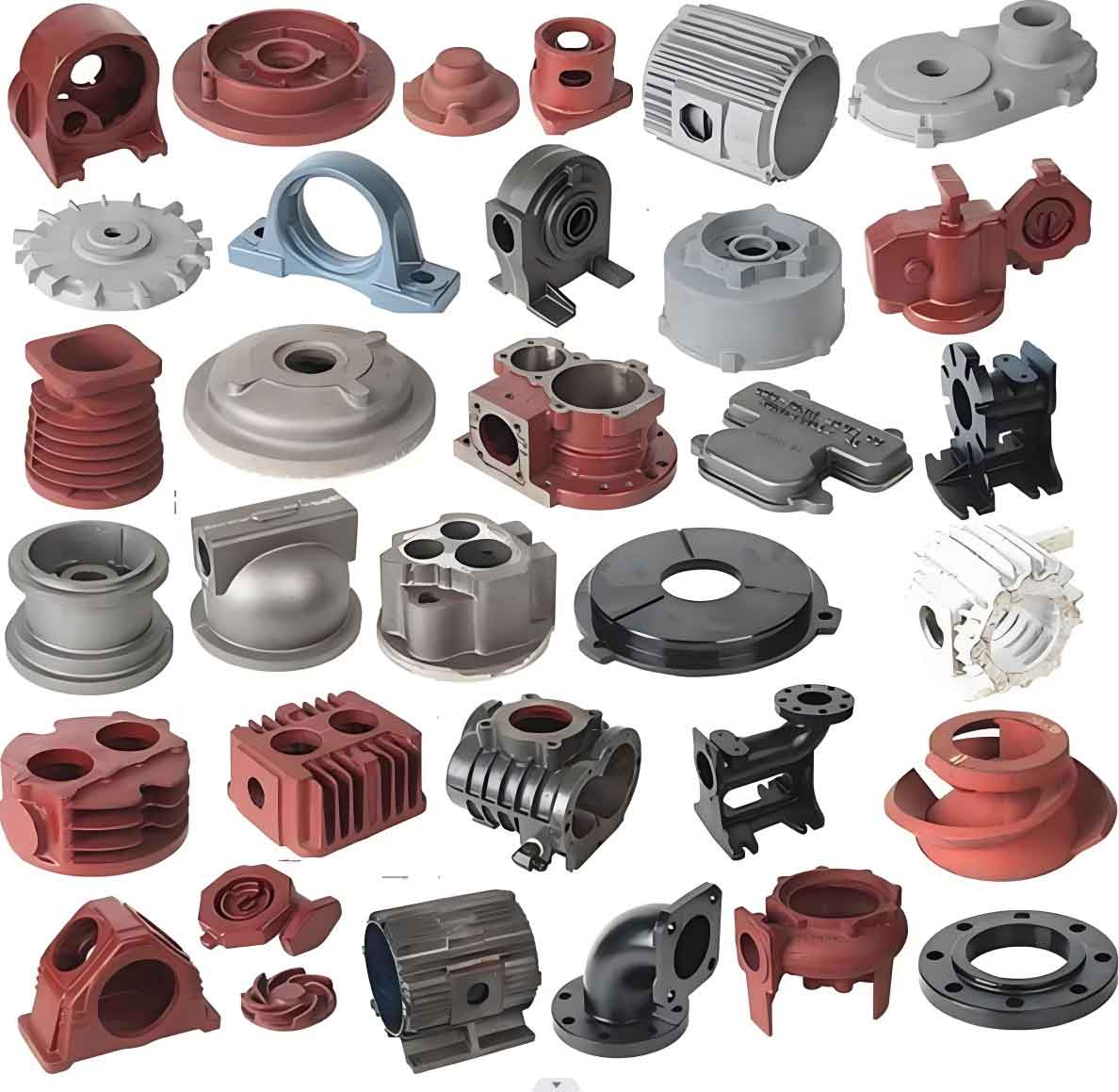
Introduction
The casting products manufacturers has traditionally been associated with labor-intensive processes and significant material waste. However, recent advancements are driving a paradigm shift towards more efficient, precise, and environmentally friendly manufacturing. Leading manufacturers are embracing these changes to maintain a competitive edge and meet the evolving demands of modern industries.
Key Advancements in Casting Manufacturing
- Adoption of Advanced Technologies:
- 3D Printing and Additive Manufacturing: The integration of 3D printing in casting products manufacturers, especially for creating complex molds and patterns, has significantly reduced lead times and costs. Additive manufacturing allows for the production of intricate designs that were previously impossible or cost-prohibitive.
- Robotics and Automation: Automation in casting products manufacturers, from mold handling to pouring and finishing, enhances precision, reduces human error, and increases production efficiency. Robotics are being used for repetitive and hazardous tasks, improving worker safety.
- Enhanced Materials and Alloys:
- High-Performance Alloys: The development of new alloys with superior properties, such as high strength, corrosion resistance, and thermal stability, is expanding the applications of cast components. These materials are crucial for industries that require components to withstand extreme conditions.
- Eco-Friendly Materials: Manufacturers are increasingly focusing on sustainable materials that reduce environmental impact. Recycled metals and alloys are being utilized without compromising on quality.
- Sustainability Initiatives:
- Waste Reduction: Advanced casting techniques such as near-net shape casting minimize material waste by producing components that require little to no machining. This not only conserves materials but also reduces energy consumption.
- Energy Efficiency: The adoption of energy-efficient furnaces and process optimization techniques is helping manufacturers reduce their carbon footprint. Renewable energy sources are also being integrated into casting facilities.
- Quality Control and Inspection:
- Non-Destructive Testing (NDT): Advanced NDT methods, including X-ray and CT scanning, ensure the integrity and reliability of cast components. These techniques detect internal defects without damaging the parts.
- Real-Time Monitoring: The implementation of IoT and AI technologies enables real-time monitoring of casting products manufacturers. This allows for immediate adjustments, reducing defects and improving overall product quality.
Table: Comparative Analysis of Traditional and Modern Casting Techniques
Aspect | Traditional Casting Techniques | Modern Casting Techniques |
---|---|---|
Lead Time | Long (manual pattern creation) | Short (3D printing and rapid prototyping) |
Precision | Moderate (manual processes) | High (automated and controlled processes) |
Material Waste | High (extensive machining required) | Low (near-net shape casting) |
Energy Efficiency | Low (conventional furnaces) | High (energy-efficient and renewable sources) |
Inspection Methods | Limited (surface inspection) | Advanced (NDT, real-time monitoring) |
Complexity of Designs | Limited (manual mold making) | High (additive manufacturing) |
Environmental Impact | High (waste and emissions) | Low (sustainable practices) |
Leading Manufacturers and Their Innovations
- Company A: Pioneering Automation:
- Robotic Integration: Company A has implemented advanced robotic systems for mold handling, metal pouring, and post-casting finishing. This has resulted in a significant reduction in production time and increased consistency in product quality.
- Automated Quality Control: Utilizing AI-powered inspection systems, the company can detect defects in real-time, ensuring that only the highest quality products reach the market.
- Company B: Advancing Material Science:
- High-Performance Alloys: Company B has developed proprietary alloys that offer superior strength and durability. These materials are being used in critical applications such as aerospace turbine blades and automotive engine components.
- Eco-Friendly Initiatives: The company is a leader in using recycled materials and has significantly reduced its carbon footprint through sustainable practices and energy-efficient production methods.
- Company C: Revolutionizing Design and Prototyping:
- 3D Printing Innovations: Company C uses advanced 3D printing technologies to create complex molds and patterns, enabling rapid prototyping and reducing development times for new products.
- Collaborative Engineering: By leveraging digital twin technology, the company collaborates with clients to optimize designs before production, ensuring optimal performance and manufacturability.
- Company D: Enhancing Sustainability:
- Energy-Efficient Operations: Company D has invested in state-of-the-art, energy-efficient furnaces and renewable energy sources to power its casting facilities. This has led to significant reductions in energy consumption and emissions.
- Waste Minimization: The company employs near-net shape casting techniques and advanced process optimization to minimize material waste, enhancing both environmental and economic sustainability.
Future Prospects
The future of the casting industry looks promising, with continuous advancements poised to further enhance efficiency, precision, and sustainability. Key trends expected to shape the industry include:
- Smart Manufacturing:
- IoT and AI Integration: The adoption of smart manufacturing technologies will enable more precise control and optimization of casting processes, reducing defects and improving overall efficiency.
- Predictive Maintenance: AI-driven predictive maintenance will help manufacturers identify and address potential equipment failures before they occur, minimizing downtime and reducing maintenance costs.
- Sustainable Practices:
- Circular Economy: The move towards a circular economy will see more manufacturers adopting recycling and reusing practices, reducing waste and conserving resources.
- Green Technologies: Continued investment in green technologies, such as renewable energy and eco-friendly materials, will drive further reductions in the environmental impact of casting operations.
- Customization and Flexibility:
- Mass Customization: Advances in additive manufacturing and digital design tools will enable mass customization, allowing manufacturers to produce small batches of highly customized components efficiently.
- Flexible Manufacturing Systems: The development of flexible manufacturing systems will allow for rapid reconfiguration of production lines, accommodating a wider range of products and reducing lead times.
Conclusion
Leading casting products manufacturers are revolutionizing the industry through the adoption of advanced technologies, innovative materials, and sustainable practices. By embracing automation, enhancing material performance, and prioritizing sustainability, these companies are setting new standards for quality and efficiency in casting products manufacturers. As the industry continues to evolve, ongoing advancements in smart manufacturing, sustainable practices, and flexible production systems will further drive innovation, ensuring that the casting industry remains at the forefront of modern manufacturing.