Mix gypsum and water in a ratio of 100:45, stir thoroughly until all bubbles in the gypsum slurry are exhausted, and coat the surface of the impeller mold with gypsum slurry, as shown in Figure 1 (a). Pay attention to the fact that the blades should also be filled with gypsum and wait for the bubbles in the surface gypsum to be discharged to prevent affecting the quality of the impeller investment casting during pouring. Pour the prepared gypsum slurry into a steel cup to make the bottom layer, and place the impeller model with a dry and solid surface into the steel cup to fully contact the bottom layer gypsum. Pour gypsum into the steel cup to ensure that the mold is centered in the gypsum. When the gypsum slurry is about to pass through the pouring riser, stop pouring the gypsum. The steel cup wrapped in gypsum is shown in Figure 1 (b).
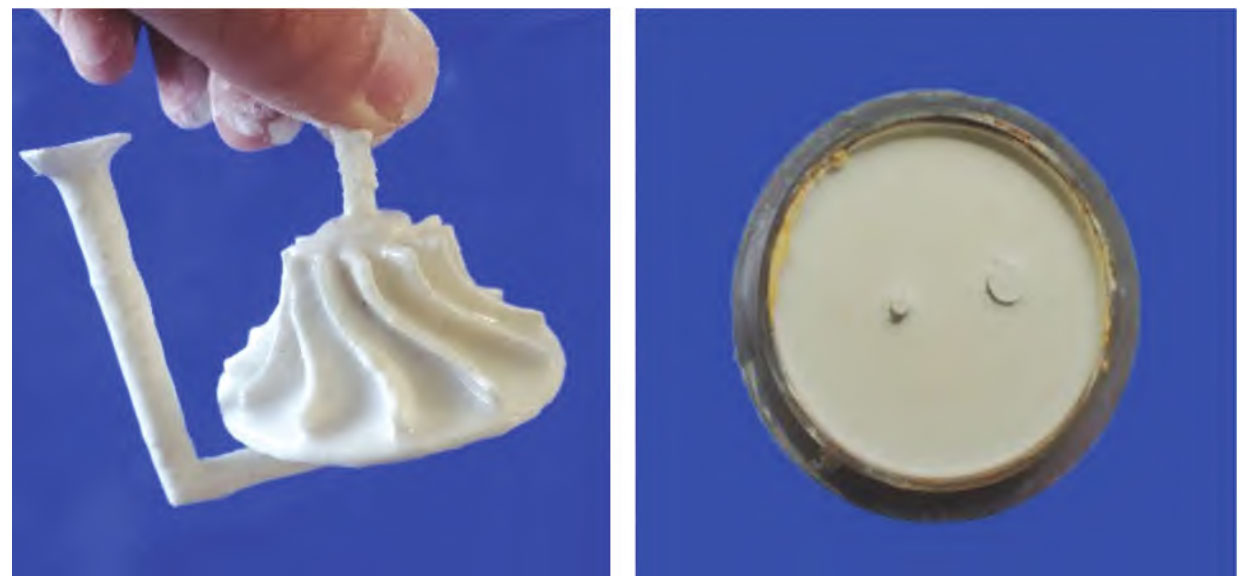
After the gypsum has hardened, remove the adhesive tape, plastic bags, and cardboard wrapped around the surface of the steel cup, and carefully inspect the bottom of the steel cup for any residual paper scraps. Place the steel cup upright in the test resistance furnace. After the temperature of the resistance furnace rises to 400 ℃, keep it warm for 15 minutes, after reaching 600 ℃, keep it warm for 30 minutes, and after reaching 750 ℃, keep it warm for 2 hours to ensure that the PLA material can be completely vaporized. Wait for the resistance furnace to cool down to 600 ℃ and start the furnace. Heat to melt the aluminum alloy, as shown in Figure 2 (a). Clamp the crucible containing aluminum alloy molten liquid with tongs and pour it against the removed steel cup while heating it. If any molten metal overflows from the pouring riser, the pouring is completed, as shown in Figure 2 (b).
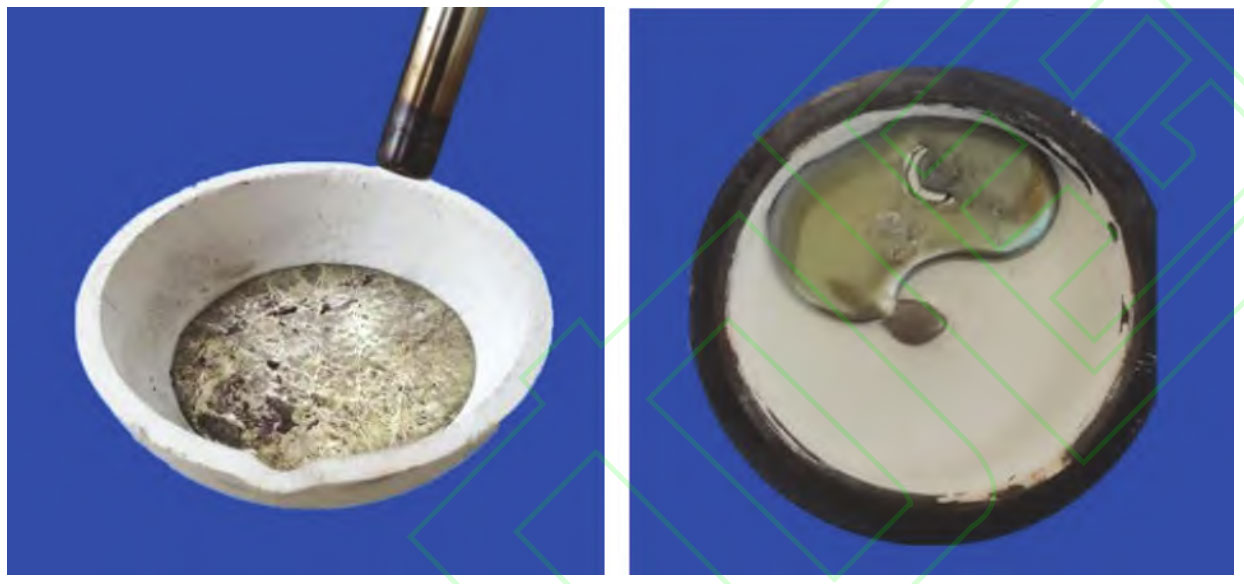
After the steel cup cools down, break the gypsum in the cup and pour it out. Take out the investment casting, and be careful not to use too much force when striking the gypsum to avoid causing deformation of the investment casting. Remove the surface gypsum and riser of the investment casting to obtain the impeller investment casting. From Figure 3 (a), it can be seen that there is a layer of oxide skin on the surface of the impeller investment casting, without defects such as fusion marks, pores, and shrinkage porosity. Grind the impeller investment casting with sandpaper, and the cleaned investment casting is shown in Figure 3 (b).
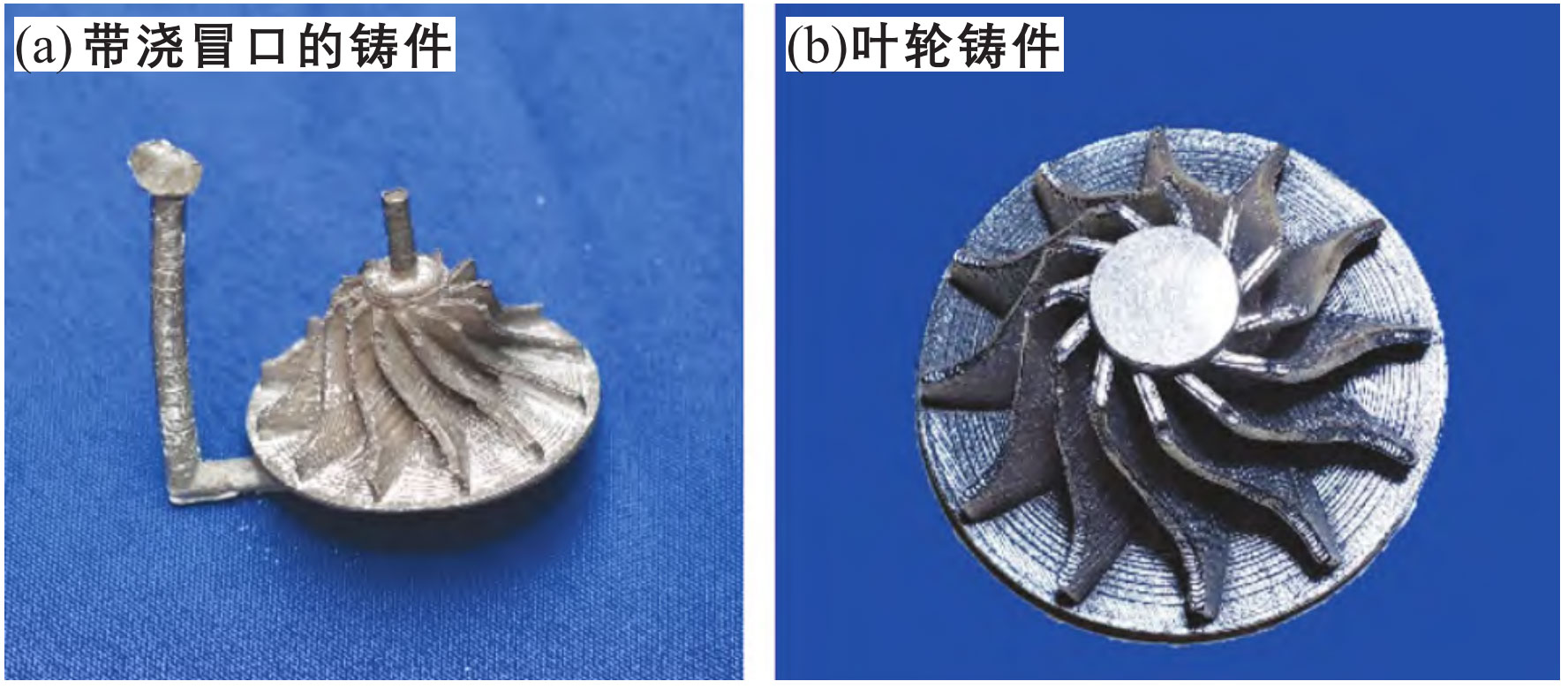