The engine block is one of the most complicated parts in the cast parts, and various sand cores are needed in the mold cavity, cylinder barrel, oil duct and water channel. At the same time, the thickness of each part varies, ranging from 3 to 20mm. Therefore, during the pouring process, the solidification process of each part is different. The angle between the thin wall and the tip is the most prone to the occurrence of white mouth structure, as shown in the figure, a large range of white mouth structure is found at the staggered hole. Because the hardness of the white structure is large and the machining performance is very poor, it is easy to wear the tool and even break the tool in the machining process. 1-6 respectively correspond to the metallography at each position. Position 1-6 is from near to far away from the edge (2mm away from each two points), the degree of white mouth is from deep to shallow, and the total width of white mouth is about 15mm. The microhardness values of various parts are shown in the table. There are a lot of lath cementite in the area (edge) with serious white mouth structure. The Vickers hardness here reaches 497hv, and the machinability is very poor.
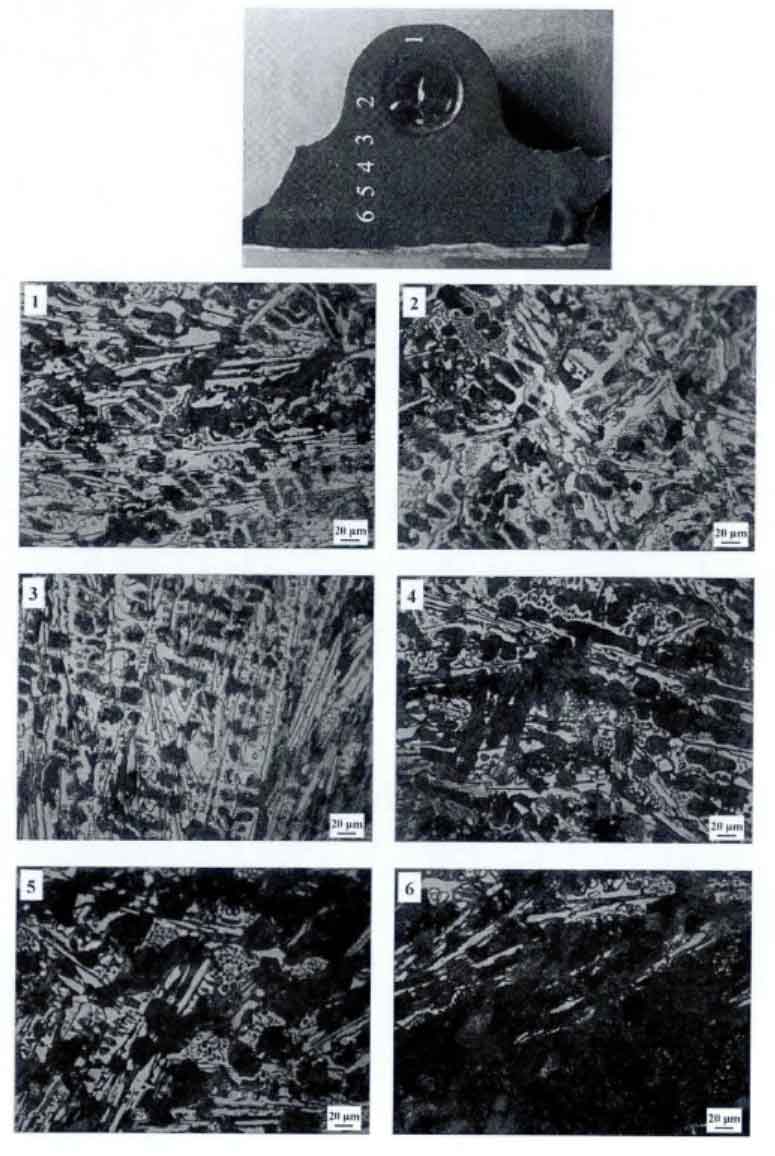
There are many factors that cause the microstructure of this kind of large white cast iron, mainly including: the inoculant is not uniformly dissolved in the molten iron, the outlet water temperature of the molten iron is high and it stays still in the holding furnace for too long, the coating in the sand mold is too thick, and the cylinder body is unpacked too early. These factors change the cooling mode of molten iron during solidification. In order to eliminate such defects, the cooperative unit has taken a series of measures.
Position | 1 | 2 | 3 | 4 | 5 | 6 |
HV | 523 | 464 | 472 | 437 | 363 | 289 |
- After the molten iron after one inoculation is introduced into the insulation pouring furnace, the inoculation effect is more uniform through repeated pressurization and pressure relief, and the furnace water temperature can be uniform at the same time;
- The molten iron in the pouring furnace shall be poured within the specified time;
- The coating of sand core shall be sprayed in strict accordance with the operation process to make the coating thickness uniform;
- For thin-walled and complex cylinder body rough, delay the unpacking time (2-2.5h).
Through the improvement of the above process measures, the white layer at the edge of the gray cast iron can meet the requirements of machining.