Aiming at the problems existing in the initial process trial production of guide rail steel castings, the initial casting process plan was improved and optimized, and improvement measures were formulated. The specific improvement measures are as follows:
(1) Change the position of the pouring system and conduct supplementary pouring at the later stage of pouring. The gating system has been improved from the outer side of the steel casting to the inner side of the steel casting, and the inner runner has been introduced from the original side riser to both the side riser and the intermediate riser. This shortens the flow distance of liquid metal during the mold filling process and reduces heat loss, which is beneficial to the mold filling of the steel casting.
During the pouring process, supplementary pouring shall be conducted to avoid casting defects such as insufficient pouring of steel castings and cold shuts.
(2) Optimize riser settings and take anti deformation measures. Due to the poor feeding effect of dispersed small risers on steel castings, as well as the dispersed distribution of dispersed small risers, it is easy to cause problems such as dispersed stress concentration areas and deformation of steel castings. An integral riser is adopted, which can form a good feeding effect on the steel casting. At the same time, the solidification of the integral riser is relatively slow, and the deformation of the steel casting can be effectively reduced through the inhibition of shrinkage by the mold cavity.
In combination with the empirical design of the initial process of rail steel castings, the defects and problems reflected in the trial produced steel castings, and considering that the stress and deformation laws during solidification are difficult to actually measure, this study uses ProCAST three-dimensional digital simulation software to simulate its stress, and the results are shown in Figure 1.
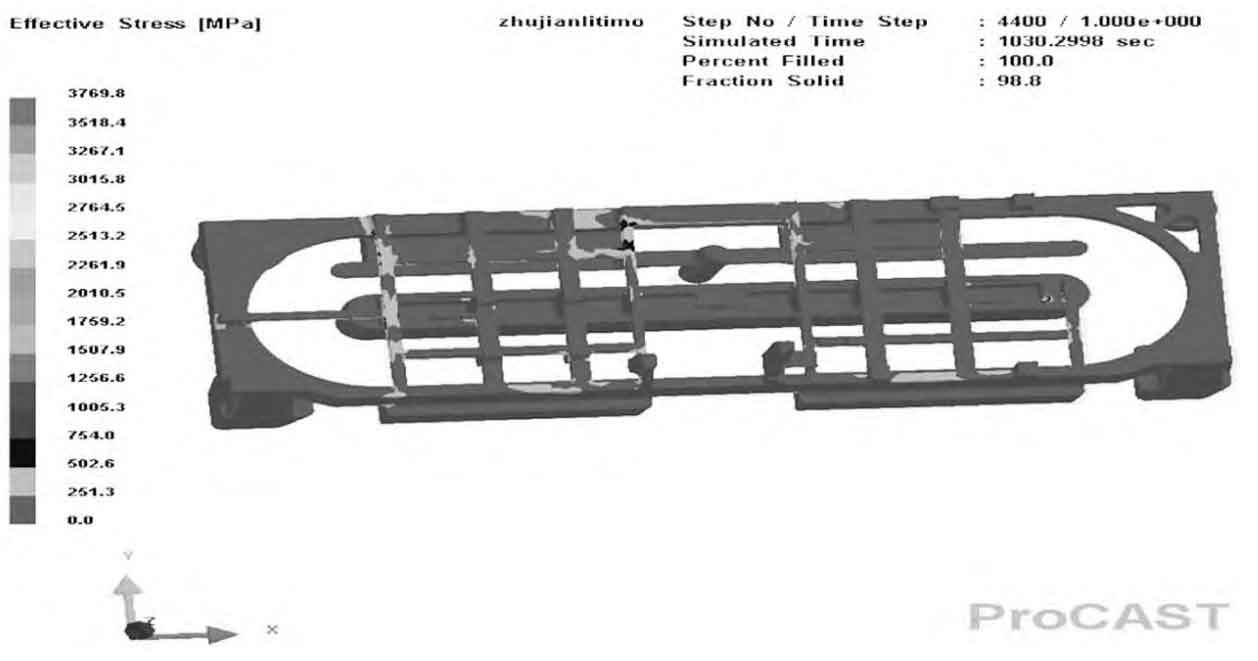
According to the effective stress distribution of the guide rail steel casting after solidification in Figure 1, after the improvement of the gating system and the overall optimization of the riser, the overall stress distribution of the steel casting tends to be consistent, with only a few rounded corners forming a stress concentration, the main stress concentration being 251 MPa. Whether the steel casting will form cracks under this stress is related to the temperature and yield stress corresponding to the material used in the steel casting during solidification. Figure 2 shows the relationship between ZG32MnMo temperature and yield strength.
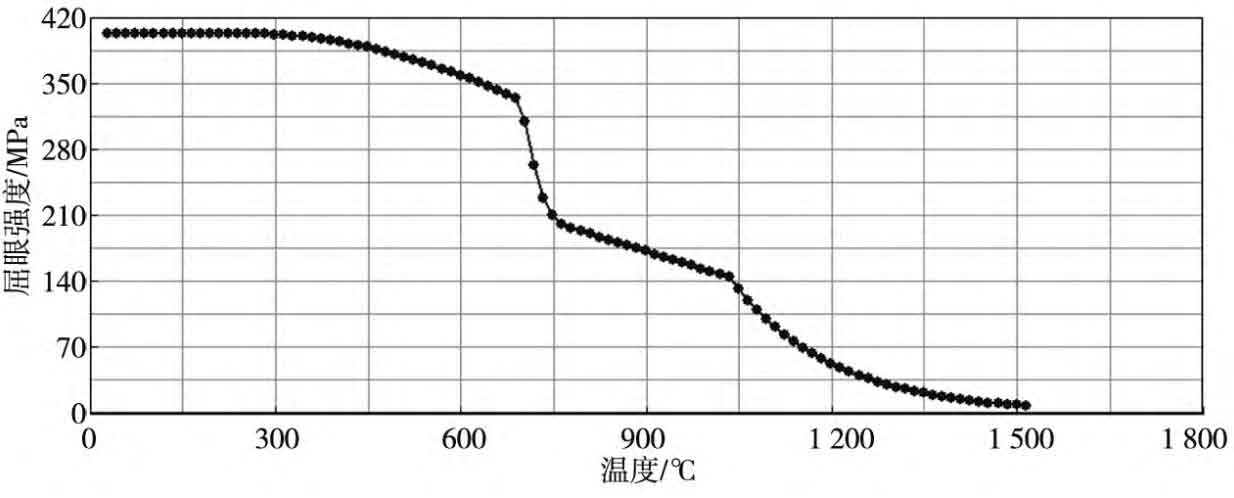
As can be seen from Figure 2, the yield strength of ZG32MnMo increases with the decrease of temperature, reaching 420 MPa eventually, which is far greater than the stress of 251 MPa after the solidification of the steel casting, indicating that the stress of the steel casting has been well resolved through the coordination between the integral risers.
Figure 3 shows the average stress simulation results of steel castings. It can be seen that at the four corners of the lower plane of the guide rail, due to the final solidification of the riser, upward tensile stress is formed at this position, causing upward warping and deformation here.
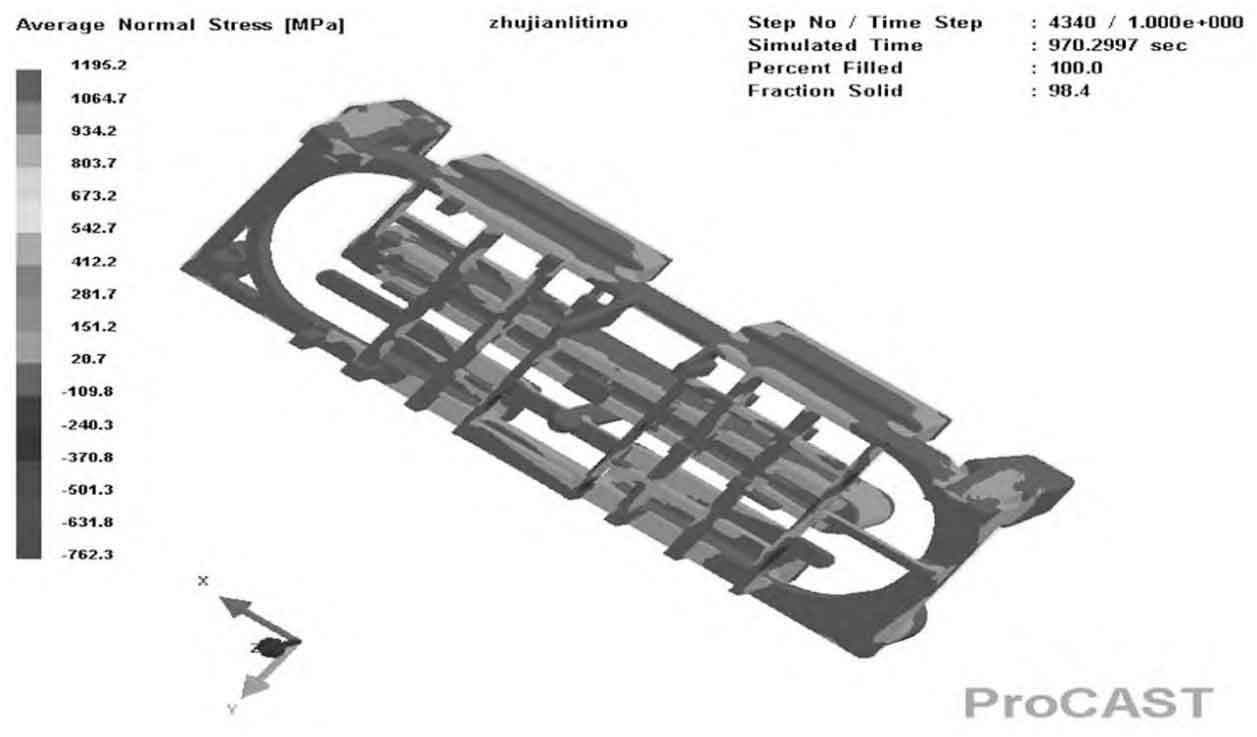
According to the simulation results, tie bars are added between the two sides and the middle riser, and a 4 mm counter deformation amount is added at the bottom of the four corners to offset the dimensional out-of-tolerance caused by the deformation. The optimized casting process is shown in Figure 4.
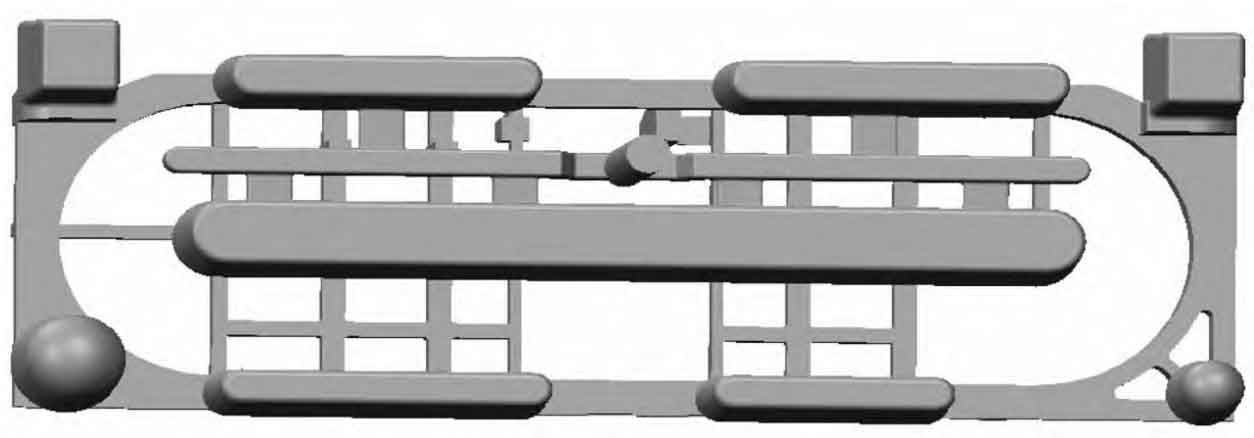
(3) Improvement measures for oversize of steel castings. According to the conversion ratio between the mold size and the actual size of the trial produced steel castings, the shrinkage rate of the inner cavity in the length direction is set to 1.5%, and the mold is adjusted accordingly. At the same time, the placement method of the steel castings for heat treatment is improved, from horizontal to vertical. The steel castings and pallets are welded and reinforced with steel bars to prevent secondary deformation caused by heat treatment. The steel castings are removed after heat treatment, and the specific placement method is shown in Figure 5.
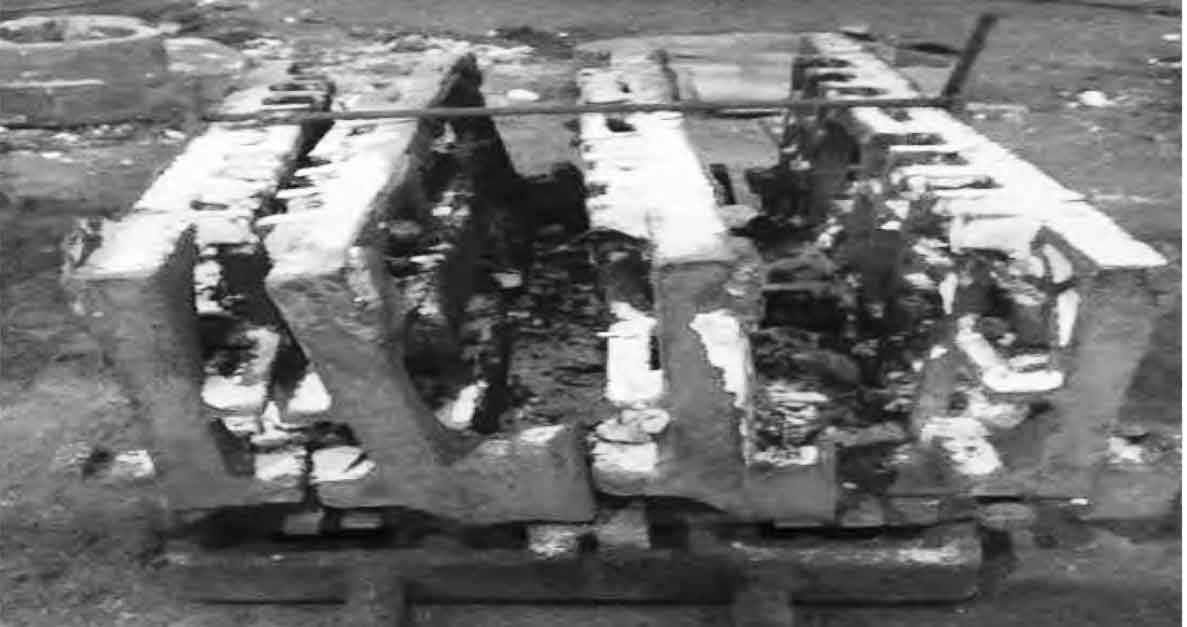
(4) Preventive measures for hot cracking of steel castings. In view of the thermal cracks at the corners of individual connecting ribs of guide rail steel castings, which are caused by the inability to obtain liquid metal shrinkage, the casting rounded corners (increased from R5 to R10) are increased at the crack defects and chromium ore sand is placed to form a chill at this location to avoid stress concentration at the rounded corners.