1. Calculation of centrifugal speed by empirical formula
In the production practice of horizontal centrifugal casting, the centrifugal speed of casting casting is calculated according to Konstantinff’s empirical formula. The formula is as follows:
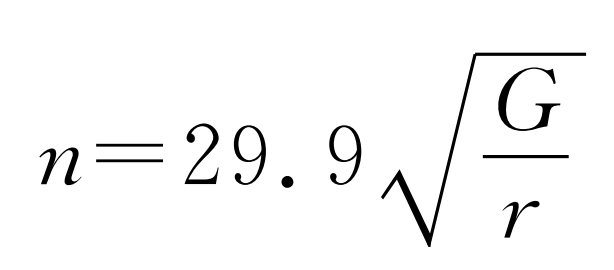
In the formula, n is the rotational speed of the mold (r/min), G is the gravity coefficient, r is the radius of the inner surface of the casting (m), and the general gravity coefficient is 40~110. The casting speed range is 840~1380r/min, and the casting speed of horizontal centrifugal casting is 1200r/min according to production experience.
2. Boundary conditions and physical parameters
The horizontal centrifugal casting cylinder liner is made of pearlitic ductile iron. The chemical composition of the material is shown in Table 1. The mold and baffle material are HT250.
Element | C | S | Si | Mn | Cu | Ni | Mg | Ce |
Content | 3.4-3.9 | <0.02 | 2.4-2.9 | ≤0.5 | 1.0-1.3 | 0.1-0.3 | ≥0.035 | <0.4 |
The water-cooled multi station centrifugal casting process is adopted, and the wire feeding spheroidizing method is adopted. The pouring time is 3-5 s. The other initial horizontal centrifugal casting process parameters and thermophysical parameters are shown in Table 2.
Pouring temperature (℃) | 1340-1390 |
Pouring speed (kg/s) | 2.0-2.5 |
Preheating temperature (℃) | 200-300 |
Heat transfer coefficient of casting, mould and coating (W · m ^ – 2 · K ^ – 1) | 500 |
Heat transfer coefficient of mould and cooling water (W · m ^ – 2 · K ^ – 1) | 5000 |
Heat transfer coefficient between casting inner surface and air (W · m ^ – 2 · K ^ – 1) | 20-60 |