Grey cast iron, as a foundational material in the manufacturing industry, has also witnessed advancements and new possibilities through innovation. Let’s explore some of the recent developments in grey cast iron:
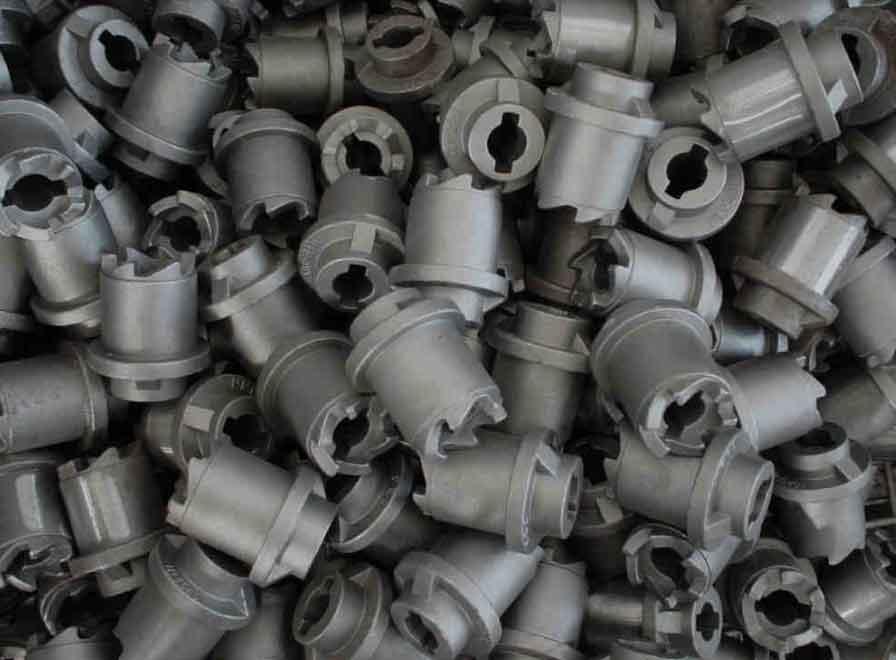
1. Alloying: The traditional grey cast iron consists mainly of iron, carbon, and silicon. However, advancements in alloying techniques have allowed the introduction of alloying elements such as nickel, chromium, molybdenum, and copper. These alloying elements can enhance specific properties of grey cast iron, such as improved strength, wear resistance, and corrosion resistance, expanding its range of applications.
2. Composite Cast Irons: Composite cast irons combine grey cast iron with other materials to create hybrid materials with enhanced properties. For example, combining grey cast iron with steel or polymers can result in materials that exhibit improved strength, toughness, or damping characteristics. Composite cast irons offer new possibilities for applications where standard grey cast iron may have limitations.
3. Surface Treatments and Coatings: Surface treatments and coatings can be applied to grey cast iron components to enhance their performance and extend their service life. Techniques such as heat treatment, nitriding, or applying protective coatings like ceramic or polymer coatings can improve wear resistance, corrosion resistance, and reduce friction. These advancements in surface treatments allow grey cast iron to be utilized in more demanding and specialized applications.
4. Enhanced Casting Techniques: Innovations in casting processes have improved the quality and consistency of grey cast iron components. Advanced casting techniques, such as computer-aided design (CAD) and computer-aided manufacturing (CAM), allow for precise control over the casting process, resulting in components with improved dimensional accuracy and reduced defects. Additionally, the use of simulation software helps optimize casting designs, reducing material waste and improving overall efficiency.
5. Sustainable Manufacturing: As sustainability becomes increasingly important, innovation in grey cast iron manufacturing focuses on reducing environmental impact. Efforts are being made to optimize energy consumption, reduce emissions, and enhance the recycling and reusability of grey cast iron. Sustainable practices, such as using recycled scrap iron or improving the efficiency of the casting process, contribute to more environmentally friendly production methods.
6. Design Optimization: Advancements in computer-aided design and simulation tools enable engineers to optimize the design of grey cast iron components. Finite element analysis (FEA) and computational fluid dynamics (CFD) simulations help predict the performance and behavior of components, allowing for design improvements and customization to specific applications. This optimization enhances the efficiency, reliability, and durability of grey cast iron components.
These advancements and new possibilities in grey cast iron have expanded its range of applications and improved its performance in various industries. By incorporating innovative techniques, materials, and design approaches, grey cast iron continues to evolve and meet the changing demands of modern manufacturing processes, offering enhanced properties, durability, and reliability.