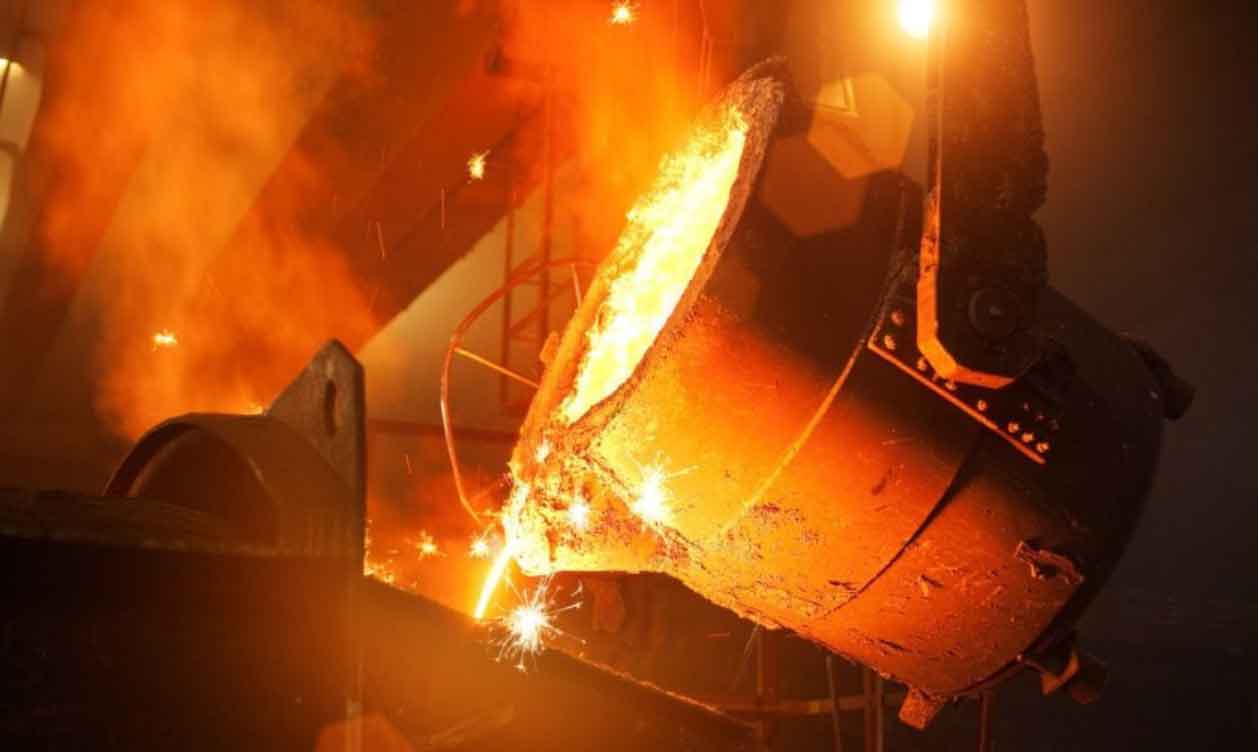
The steel casting industry has witnessed significant advancements and breakthroughs, driven by continuous innovation and technological advancements. These developments have contributed to improved efficiency, enhanced product quality, and expanded possibilities in steel casting. Here are some key areas of innovation in steel casting:
1. Advanced Simulation and Modeling:
The use of advanced computer simulations and modeling techniques has revolutionized the steel casting process. Finite element analysis (FEA) and computational fluid dynamics (CFD) simulations allow for detailed predictions of mold filling, solidification, and cooling processes. This enables engineers to optimize casting designs, minimize defects, and reduce the need for physical trial and error.
2. Additive Manufacturing (3D Printing):
Additive manufacturing, or 3D printing, is increasingly being used in steel casting. It offers the ability to create complex geometries with intricate details directly from digital models, eliminating the need for traditional pattern-making. 3D printing can produce sand molds and cores with intricate shapes, improving casting efficiency and reducing lead times.
3. Rapid Prototyping and Rapid Tooling:
Advancements in rapid prototyping techniques have accelerated the development and production of prototypes in steel casting. Technologies such as laser sintering and stereo lithography enable the quick creation of patterns or molds, facilitating faster iterations in the design and testing phases. Rapid tooling techniques also enable the production of temporary or low-volume molds, reducing time and cost for small production runs.
4. Advanced Materials and Alloys:
The development of advanced steel alloys and materials has expanded the possibilities in steel casting. High-strength and heat-resistant alloys allow for the production of components that can withstand extreme conditions. Specialized alloys with improved corrosion resistance, wear resistance, or specific properties have also been developed to cater to diverse industry needs.
5. Automation and Robotics:
Automation and robotics have transformed the steel casting industry, improving process efficiency and consistency. Automated systems for mold handling, pouring, and finishing operations reduce manual labor, enhance productivity, and ensure consistent quality. Robots are employed for tasks such as mold manipulation, pouring molten metal, and post-casting processes, offering precision and repeatability.
6. Advanced Quality Control and Inspection Techniques:
Innovations in quality control and inspection techniques have enhanced the detection and prevention of defects in steel castings. Advanced non-destructive testing (NDT) methods, such as digital radiography, ultrasonic testing, and 3D scanning, enable faster and more accurate defect identification. In-line monitoring systems and real-time data analysis contribute to proactive defect prevention and process optimization.
7. Sustainable and Energy-Efficient Practices:
The steel casting industry is adopting more sustainable and energy-efficient practices. Foundries are implementing technologies to reduce energy consumption, optimize material usage, and minimize waste generation. Additionally, the recycling and reuse of casting sand and other materials are being prioritized to minimize environmental impact.
These innovations and breakthroughs in the steel casting industry have led to improved product quality, enhanced design possibilities, reduced lead times, and increased efficiency. As technology continues to advance, the steel casting industry will likely witness further innovations that push the boundaries of what is possible in terms of design, material capabilities, and process optimization.