Gate valve body design has evolved over the years to enhance efficiency, reliability, and overall performance. Several innovative design features have been incorporated to address common challenges and improve the functionality of gate valve bodies. Here are some notable innovations in gate valve body design:
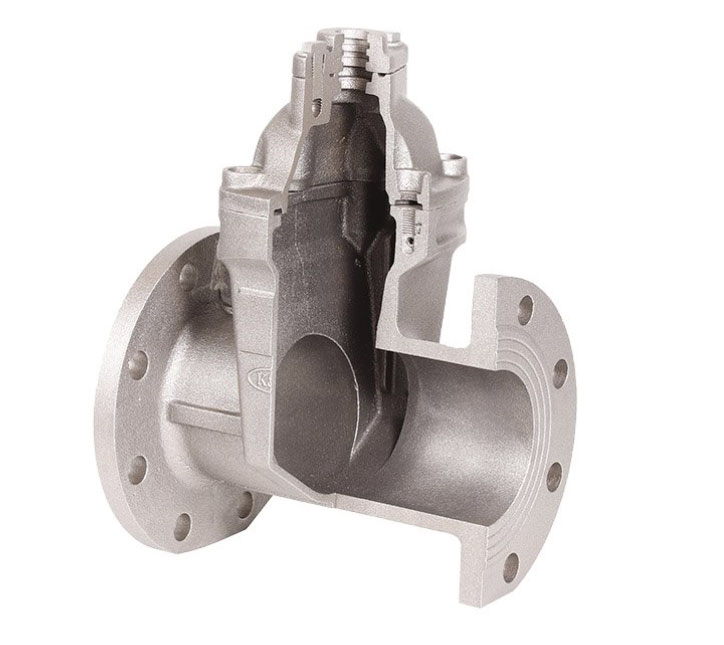
- Reduced Pressure Drop: Traditional gate valve designs often resulted in significant pressure drops across the valve, leading to energy loss and inefficiencies. To address this, modern gate valve bodies incorporate streamlined flow paths and optimized internal geometries. This helps minimize pressure drop and improves the overall efficiency of fluid flow.
- Cavity-Free Design: In standard gate valves, a cavity or pocket exists between the gate and the valve body when the valve is fully closed. This cavity can trap debris or fluid, leading to potential contamination and obstruction during valve operation. Innovative gate valve designs incorporate cavity-free or non-cavity design features, such as wedge gate or slab gate configurations, to eliminate or reduce cavity space. This improves reliability, minimizes the risk of blockages, and enhances the valve’s ability to handle solids-laden fluids.
- Self-Cleaning Functionality: Gate valves are susceptible to buildup of debris or scale on the gate and seat surfaces, which can affect sealing and overall performance. Advanced gate valve designs may incorporate self-cleaning mechanisms, such as scraping or wiping surfaces, to remove debris and maintain optimal sealing. This helps improve reliability and reduces the need for frequent maintenance.
- Improved Sealing Mechanisms: Gate valves traditionally relied on metal-to-metal seating for sealing, which could be prone to wear and leakage over time. Innovative gate valve designs incorporate advanced sealing mechanisms such as resilient or elastomeric seals, which provide effective and long-lasting sealing performance. These seals offer enhanced resistance to wear, corrosion, and leakage, resulting in improved reliability and reduced maintenance requirements.
- Modular Construction: Modular gate valve body designs allow for easier maintenance and replacement of components. The valve body is divided into modular sections, such as the bonnet, body, and seat ring, which can be individually replaced or repaired as needed. This simplifies maintenance procedures, reduces downtime, and improves the overall reliability of the gate valve.
- Advanced Materials and Coatings: Gate valve bodies are now constructed using advanced materials that offer improved corrosion resistance and durability. Materials like stainless steel, duplex stainless steel, or high-performance alloys are commonly used in corrosive or high-pressure applications. Additionally, advanced coatings, such as hard chrome or ceramic coatings, are applied to critical surfaces to enhance wear resistance and extend the valve’s lifespan.
- Smart and Remote Monitoring: Some gate valve designs integrate smart technologies and sensors to enable remote monitoring and control. This allows for real-time monitoring of valve status, performance, and predictive maintenance, enhancing overall efficiency, reliability, and operational safety.
These innovations in gate valve body design aim to improve efficiency, reliability, and performance, while also addressing specific application challenges. Manufacturers continuously strive to develop and incorporate new technologies and design features to meet the evolving needs of industries and maximize the benefits of gate valve systems.