1. Introduction
The automotive industry is constantly evolving, with a strong emphasis on improving vehicle performance, reducing weight, and enhancing manufacturing efficiency. The subframe, as a crucial component of the vehicle chassis, plays a vital role in load-bearing and vibration isolation. In recent years, the integrated die-casting process has emerged as a promising technology for subframe manufacturing, offering numerous advantages over traditional methods. This article focuses on the innovative optimization design of integrated die-casting subframes, exploring various techniques and their impact on performance, weight, and cost.
1.1 The Importance of Subframe Optimization
The subframe is an essential part of the vehicle’s chassis structure, directly influencing the vehicle’s overall performance and safety. By optimizing the subframe design, it is possible to enhance structural strength, stiffness, and NVH (Noise, Vibration, and Harshness) characteristics, while also reducing weight. This not only improves the vehicle’s handling and ride comfort but also contributes to fuel efficiency and emissions reduction.
1.2 Overview of Integrated Die – Casting Technology
Integrated die-casting is a manufacturing process that involves injecting molten metal into a die to form a single, complex component. This process offers several benefits compared to traditional manufacturing methods, such as reduced part count, improved structural integrity, and lower manufacturing costs. In the context of subframe manufacturing, integrated die-casting can eliminate the need for welding or other joining processes, resulting in a more robust and lightweight structure.
2. Optimization Objectives and Constraints
Before embarking on the optimization process, it is essential to define clear objectives and constraints. These will serve as the guiding principles for the design and optimization of the integrated die-casting subframe.
2.1 Performance Metrics
The performance of the subframe is evaluated based on several key metrics, including strength, stiffness, modal analysis, and dynamic stiffness. These metrics are crucial in determining the subframe’s ability to withstand various loads and vibrations during vehicle operation.
Performance Metric | Description |
---|---|
Strength | The ability of the subframe to withstand applied loads without failure. |
Stiffness | The resistance of the subframe to deformation under load. |
Modal Analysis | The study of the natural frequencies and mode shapes of the subframe. |
Dynamic Stiffness | The stiffness of the subframe under dynamic loading conditions. |
2.2 Constraints
In addition to performance objectives, there are also several constraints that need to be considered during the optimization process. These include manufacturing limitations, material properties, and cost considerations.
Constraint | Description |
---|---|
Manufacturing Limitations | The capabilities and limitations of the die-casting process, such as minimum wall thickness and draft angles. |
Material Properties | The mechanical properties of the selected material, such as strength, ductility, and density. |
Cost Considerations | The cost of materials, manufacturing, and assembly, as well as any potential cost savings through optimization. |
3. Structural Optimization Process
The structural optimization of the integrated die-casting subframe involves two main stages: topology optimization and parameter optimization. These stages are carried out iteratively to achieve the desired performance and weight reduction goals.
3.1 Topology Optimization
Topology optimization is a powerful technique that allows for the determination of the optimal material distribution within a given design space. By varying the density of the material in different regions of the subframe, it is possible to find the most efficient structural configuration that meets the defined performance and constraint requirements.
3.1.1 Principle of Topology Optimization
The basic principle behind topology optimization is to start with an initial design domain and then iteratively remove or add material based on a set of optimization criteria. This is typically achieved using numerical methods such as the finite element method (FEM). The optimization process aims to minimize an objective function, such as the compliance (inverse of stiffness) or mass of the structure, while satisfying the defined constraints.
3.1.2 Mathematical Model for Topology Optimization
The mathematical model for topology optimization of the subframe can be formulated as follows:
Minimize: (Objective function, e.g., compliance or mass)
Subject to:
- (Volume fraction constraint)
- (Stress constraint)
- (Modal constraint)
where represents the design variables (e.g., material density in different regions), is the volume fraction of the structure, is the maximum allowed volume fraction, is the stress in the structure, is the maximum allowed stress, is the modal stiffness, is the natural frequency, and is a weighting factor for the modal constraint.
3.1.3 Results and Interpretation of Topology Optimization
After performing the topology optimization, the resulting subframe design shows a significant improvement in performance and material efficiency. The optimized design typically features a more streamlined and efficient load-bearing structure, with material concentrated in areas where it is most needed to resist loads and vibrations.
3.2 Parameter Optimization
Once the topology optimization has been completed, parameter optimization is carried out to further refine the design and achieve the desired weight reduction. This involves optimizing the dimensions and thicknesses of the subframe components.
3.2.1 Parameterization of the Subframe Design
The subframe design is parameterized by defining a set of design variables, such as the thickness of different sections, the length and width of certain features, and the angles of various components. These design variables are then used as inputs for the optimization process.
3.2.2 Optimization Algorithm and Constraints
The parameter optimization is typically carried out using an optimization algorithm, such as a genetic algorithm or a gradient-based algorithm. The optimization process aims to minimize an objective function, such as the mass of the subframe, while satisfying the defined constraints. These constraints may include strength requirements, stiffness requirements, and manufacturing limitations.
3.2.3 Results and Impact of Parameter Optimization
The results of parameter optimization show a further reduction in the weight of the subframe while maintaining or even improving its performance. By optimizing the dimensions and thicknesses of the subframe components, it is possible to achieve a more lightweight and efficient design.
4. Performance Analysis of the Optimized Subframe
After the structural optimization process, the optimized subframe is analyzed to evaluate its performance in terms of strength, stiffness, modal analysis, and dynamic stiffness. The results are compared with those of the original subframe to demonstrate the effectiveness of the optimization process.
4.1 Strength Analysis
The strength of the optimized subframe is evaluated by subjecting it to various load cases and analyzing the resulting stresses. The results show that the optimized subframe has a significantly higher strength compared to the original subframe, with a reduction in maximum stress under certain load conditions.
Load Case | Original Subframe Max Stress (MPa) | Optimized Subframe Max Stress (MPa) |
---|---|---|
Case 1 | 141.3 | 134.0 |
Case 2 | 303.4 | 207.9 |
Case 3 | 269.0 | 180.7 |
Case 4 | 318.4 | 165.2 |
4.2 Stiffness Analysis
The stiffness of the optimized subframe is evaluated by measuring its deformation under applied loads. The results show that the optimized subframe has a higher stiffness compared to the original subframe, with an improvement in the stiffness values at various attachment points.
Attachment Point | Original Subframe Stiffness (N/mm) | Optimized Subframe Stiffness (N/mm) |
---|---|---|
Arm1 – X | 58824 | 66666.66 |
Arm1 – Y | 62500 | 71428.57 |
Arm1 – Z | 610.9 | 2857.40 |
Arm2 – X | 18519 | 22727.27 |
Arm2 – Y | 23810 | 32258.06 |
Arm2 – Z | 5525 | 5780.34 |
Bar – X | 125000 | 125000.00 |
Bar – Y | 28571 | 100000.00 |
Bar – Z | 17241 | 29411.76 |
Steering Rack – X | 90909 | 142857.40 |
Steering Rack – Y | 76923 | 66666.66 |
Steering Rack – Z | 13699 | 16949.15 |
Em1 – X | 25641 | 41666.66 |
Em1 – Y | 4167 | 4878.04 |
Em1 – Z | 3410 | 3472.22 |
Em2 – X | 10870 | 16949.15 |
Em2 – Y | 2597 | 4587.15 |
Em2 – Z | 15625 | 28571.42 |
Em3 – X | 7692 | 10204.08 |
Em3 – Y | 2933 | 4672.89 |
Em3 – Z | 8929 | 11363.63 |
4.3 Modal Analysis
The modal analysis of the optimized subframe is carried out to determine its natural frequencies and mode shapes. The results show that the optimized subframe has a higher first-order modal frequency compared to the original subframe, indicating an improvement in its dynamic characteristics.
Original Subframe Modal (Hz) | Optimized Subframe Modal (Hz) |
---|---|
274.8 | 320.1 |
366.3 | 367.7 |
374.1 | 389.8 |
4.4 Dynamic Stiffness Analysis
The dynamic stiffness of the optimized subframe is evaluated by measuring its stiffness under dynamic loading conditions. The results show that the optimized subframe has a higher dynamic stiffness compared to the original subframe, with an improvement in the dynamic stiffness values at various attachment points.
Attachment Point | Original Subframe Dynamic Stiffness (N/mm) | Optimized Subframe Dynamic Stiffness (N/mm) |
---|---|---|
Arm1 – X | 119409 | 147226 |
Arm1 – Y | 23273 | 23592 |
Arm1 – Z | 72249 | 133455 |
Arm2 – X | 282524 | 1206424 |
Arm2 – Y | 183388 | 184599 |
Arm2 – Z | 2464991 | 2464991 |
Em1 – X | 1130542 | 1859280 |
Em1 – Y | 148756 | 149572 |
Em1 – Z | 2237305 | 2241147 |
Em2 – X | 35557 | 44174 |
Em2 – Y | 14151 | 17304 |
Em2 – Z | 31061 | 32862 |
Em3 – X | 33050 | 43660 |
Em3 – Y | 20478 | 22372 |
Em3 – Z | 32345 | 33047 |
5. Weight and Cost Analysis
In addition to performance analysis, the weight and cost of the optimized subframe are also evaluated and compared with those of the original subframe. The results show that the optimized subframe offers significant weight and cost savings.
5.1 Weight Reduction
The optimized subframe has a significantly lower weight compared to the original subframe. The weight reduction is achieved through a combination of topology optimization and parameter optimization, which result in a more efficient use of materials and a reduction in unnecessary mass.
Original Subframe Weight (kg) | Optimized Subframe Weight (kg) | Weight Reduction (%) |
---|---|---|
12.43 | 10.4 | 16.3 |
5.2 Cost Reduction
The optimized subframe also offers cost savings compared to the original subframe. The cost reduction is achieved through a combination of factors, including reduced manufacturing processes (due to the integrated…
6. Case Studies and Real – World Applications
6.1 Case Study 1: A Leading Automobile Manufacturer
A well – known automobile manufacturer decided to adopt the integrated die – casting subframe technology in one of its new vehicle models. The company aimed to improve the vehicle’s performance, reduce weight, and enhance manufacturing efficiency.
- Design and Optimization Process: The design team started with a detailed analysis of the existing subframe design and identified the areas for improvement. They then applied the topology optimization and parameter optimization techniques as described in this article. The optimization process was carried out in multiple iterations to achieve the desired performance and weight reduction goals.
- Performance Results: After implementing the optimized subframe design, the vehicle showed significant improvements in handling and ride comfort. The strength and stiffness of the subframe were enhanced, resulting in better load – bearing capacity and reduced vibrations. The modal and dynamic stiffness characteristics also improved, contributing to a quieter and more stable driving experience.
- Weight and Cost Savings: The integrated die – casting subframe resulted in a weight reduction of approximately 18% compared to the traditional subframe design. This led to improved fuel efficiency and reduced emissions. In terms of cost, the manufacturing process was streamlined, and the number of components was reduced, resulting in a cost savings of about 10% per vehicle.
6.2 Case Study 2: An Electric Vehicle Startup
An electric vehicle startup recognized the importance of lightweight and efficient subframe design for their vehicles. They opted for the integrated die – casting subframe technology to gain a competitive edge in the market.
- Innovation in Design: The startup’s engineering team focused on customizing the subframe design to suit the specific requirements of their electric vehicles. They incorporated advanced materials and optimized the geometry to achieve maximum performance with minimum weight. The topology optimization process was used to determine the optimal material distribution, and parameter optimization was carried out to fine – tune the dimensions and thicknesses.
- Performance and Efficiency Gains: The optimized subframe significantly improved the vehicle’s acceleration and handling. The reduced weight of the subframe contributed to increased battery range and overall vehicle efficiency. The strength and stiffness of the subframe were sufficient to handle the unique load requirements of electric vehicles, ensuring safety and reliability.
- Cost – Effective Solution: Despite being a startup with limited resources, the company was able to achieve cost savings through the integrated die – casting process. The simplified manufacturing process and reduced material waste led to a more cost – effective production of the subframe, enabling them to offer competitive pricing for their vehicles.
7. Comparison with Other Subframe Manufacturing Technologies
7.1 Traditional Welding – Based Subframes
- Strength and Stiffness: Traditional welded subframes can achieve adequate strength and stiffness, but the welding process can introduce stress concentrations and potential weak points. In contrast, the integrated die – casting subframe offers a more uniform and continuous structure, resulting in better overall strength and stiffness distribution.
- Weight: Welded subframes often require additional reinforcements to achieve the required strength, which can increase the weight. The integrated die – casting process allows for a more efficient use of materials, resulting in a lighter subframe.
- Manufacturing Complexity: Welding multiple components together is a time – consuming and complex process, requiring skilled labor and precise alignment. The die – casting process simplifies manufacturing by producing a single component, reducing assembly time and potential errors.
7.2 Composite Subframes
- Material Properties: Composite subframes offer excellent strength – to – weight ratios, but they also have some limitations in terms 荥 of cost, manufacturability, and recyclability. The integrated die – casting subframe, using traditional metals, has more established manufacturing processes and better recyclability.
- Performance in Different Environments: Composite materials may have different performance characteristics in extreme temperatures or humidity conditions. Metals used in die – casting subframes generally have more stable performance across a wider range of environmental conditions.
- Cost and Availability of Materials: Composite materials can be expensive and may have limited availability compared to metals. The die – casting process uses commonly available metals, making it a more cost – effective option for mass production.
8. Design Guidelines for Integrated Die – Casting Subframes
8.1 Geometric Considerations
- Simplify the Geometry: The die – casting process is more suitable for simpler geometries with fewer undercuts and complex features. Designers should aim to simplify the subframe geometry as much as possible while still meeting the performance requirements. This can reduce tooling costs and improve the quality of the cast part.
- Optimize Draft Angles: Adequate draft angles are crucial for easy ejection of the cast part from the die. Designers should ensure that all surfaces have appropriate draft angles to avoid sticking and damage to the part during ejection.
- Consider Wall Thickness: The minimum wall thickness should be determined based on the mechanical properties of the material and the required strength and stiffness. Too thin a wall thickness can lead to insufficient strength, while too thick a wall thickness can increase weight and material costs.
8.2 Material Selection
- Strength and Ductility: The selected material should have sufficient strength to withstand the expected loads and also have adequate ductility to avoid brittle failure. High – strength alloys are often preferred for subframe applications, but their ductility should also be considered.
- Density and Weight Reduction: Materials with lower density can contribute to weight reduction. However, the trade – off between density and other mechanical properties should be carefully considered. For example, some lightweight materials may have lower strength, so a balance needs to be struck.
- Corrosion Resistance: Depending on the application environment, corrosion resistance may be an important factor. Some metals may require additional surface treatments or coatings to prevent corrosion.
8.2.1 Common Materials Used in Die – Casting Subframes
- Aluminum Alloys: Aluminum alloys are widely used in die – casting subframes due to their good strength – to – weight ratio, corrosion resistance, and recyclability. Different alloy compositions can be selected based on the specific requirements of the application.
- Magnesium Alloys: Magnesium alloys offer even lower density than aluminum alloys, resulting in greater weight reduction potential. However, they may require more careful handling during manufacturing due to their higher reactivity.
- Zinc Alloys: Zinc alloys are another option for die – casting subframes. They have good casting properties and can provide sufficient strength for some applications. However, their density is relatively higher than aluminum and magnesium alloys.
8.3 Load – Bearing Design Principles
- Load Path Optimization: The subframe should be designed to efficiently transfer loads from the vehicle’s suspension and powertrain to the chassis. This requires a clear understanding of the load paths and the distribution of forces. The topology optimization process can be used to optimize the load – bearing structure and ensure that the loads are properly transferred.
- Stress Concentration Avoidance: Avoiding stress concentrations is crucial for the integrity of the subframe. This can be achieved by using smooth transitions between different components and avoiding sharp corners or notches. The design should also ensure that the stress levels in all areas of the subframe are within the allowable limits.
- Redundancy and Safety Factors: Designers should consider incorporating redundancy and appropriate safety factors in the subframe design. This can provide additional protection in case of unexpected loads or component failures. For example, having multiple load – bearing paths or using materials with higher safety factors can enhance the reliability of the subframe.
9. Simulation and Testing in the Design Process
9.1 Finite Element Analysis (FEA)
- Modeling the Subframe: FEA is used to model the subframe structure and simulate its behavior under different loads and conditions. The model should accurately represent the geometry, material properties, and boundary conditions of the subframe. This requires detailed knowledge of the subframe design and the physics of the problem.
- Load Cases and Constraints: Different load cases are considered in the FEA, such as static loads from the vehicle’s weight, dynamic loads from driving conditions, and impact loads from collisions. The constraints are also defined based on the actual installation and operation of the subframe. For example, the attachment points to the chassis and suspension are constrained appropriately.
- Results Interpretation and Optimization: The results of the FEA are used to interpret the behavior of the subframe and identify areas for improvement. If the stress levels are too high or the stiffness is insufficient, the design can be optimized using the topology optimization and parameter optimization techniques described earlier. The FEA process can be repeated until the desired performance is achieved.
9.2 Physical Testing
- Prototype Manufacturing: Physical testing requires the manufacture of prototypes of the subframe. These prototypes can be made using the die – casting process or other manufacturing methods depending on the availability of resources and the stage of the design process. The prototypes should be as close as possible to the final design in terms of geometry and material properties.
- Testing Procedures: Different testing procedures are carried out on the prototypes, such as static strength testing, dynamic stiffness testing, modal analysis, and impact testing. These tests are used to verify the performance of the subframe and compare it with the results of the FEA. If there are…
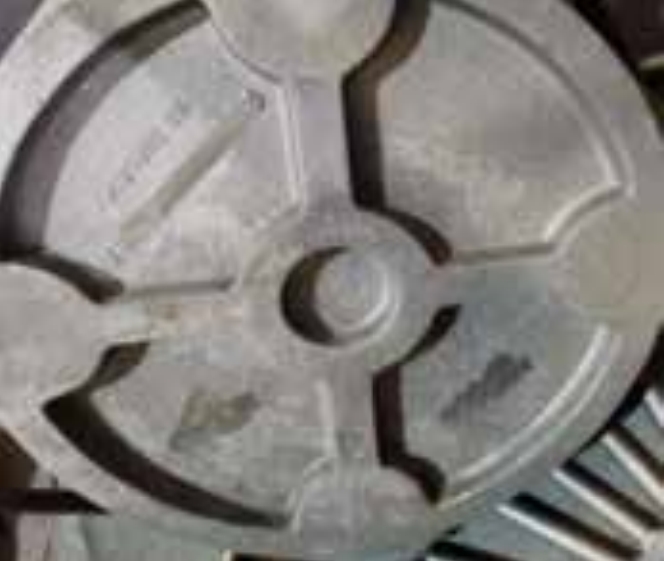